Fisher
Body - Home
Fisher Body Craftsmanship Goes to War
Fisher Body - Craftsmanship
Fisher Body - Aircraft
Fisher Body - Aircraft
Instruments
Fisher Body - Guns
Fisher Body - Tanks
Fisher Body - Miscellaneous
The Plants
Fisher Body WWII Plant Database
Cleveland Plant #1, OH Plant
Cleveland Plant #2, OH Plant
Detroit Aircraft Unit,
Detroit, MI
Detroit Die and Machine Plant
Fleetwood, Detroit, MI Plant
Flint Plant #1, MI Plant
Grand Blanc, MI Tank Arsenal
Grand Rapids, MI Plant
Lansing, MI Plant
Memphis, TN Plant
Ternstedt Manufacturing Division,
Detroit, MI
Grand Blanc Tank Arsenal Built Tanks and Tank Destroyers
Grand Blanc
built M4A2 Sherman Tank Photos
Grand Blanc
Built M4A3 Tank Photos
Grand
Blanc M10 Tank Destroyer Photos
Lansing, Michigan Fisher
Body Plant - General Motors Corporation in World War Two
Recognizing a Company
from my Hometown that contributed to winning World War Two
Lansing, MI
1922-2007
Rest in Peace
Gone but not Forgotten!!!
This page updated 12-24-2021.
Other Lansing Companies that
contributed to winning World War Two
Lansing Fisher Body had an important place
in the first 23 years of my life. My parents met while working in
the plant after World War Two. My
father worked there six days a week on his particular job in the plant
while my sister and I were growing up, He worked not only Saturdays and Sundays, but holidays
as well. He spent a lot of time in "The Shop", as he
called it. It dominated our lives because he was gone so much.
My family's association with Lansing Fisher
Body started with my grandfather going to work there sometime after
1937, when he had been a participant in the Lansing Reo sit-down strike.
More than likely, he was hired into Fisher Body because he was a
musician. Fisher Body had a brass band in which he could play.
Reo was not at all in good financial standing, so moving to a GM plant
was more secure for him. Playing in the Reo Brass Band was the
reason he was hired into 'The Reo'. However, with the United
States entrance into World War Two in 1941, he lost his job when
automotive production stopped at Lansing Fisher Body. Most of the
workers were laid off until war work could be brought into the Lansing
plant. (There is more on this history of the plant below.)
Actually, for my grandfather, this probably worked out for the better,
as he got a job at the Nash-Kelvinator plant propeller plant as a
foreman in charge of blade balancing. As the new job was within a
short walk of his house, he was able to save on gasoline and tires which
were both rationed during the war. After the end of the conflict,
he returned to Lansing Fisher Body and retired from there.
On May 23, 1942, after traveling
400 miles from his hometown in Marquette, MI, my father walked into the Lansing
Fisher Body plant and was hired. How did this happen while
thousands of previous workers were laid off? This is a classic
case of "it's not what you know, but who you know!" My father was
looking for a better job, and there was not much opportunity in
Marquette. His high school football coach knew someone at Lansing
Fisher Body and was able to arrange the job for him. My father
therefore came down to Lansing and hired into Plant Protection, which
had a different union than the UAW that represented the majority of the
workers. Plant Protection was used by management to place persons
they wanted into the plant. In later years, plant management would
offer these positions to UAW Local 602 committeemen who were giving management headaches. That way it would not have
to deal with them anymore. Several of the committeemen took the
positions. I worked with two of them during several of my summers
in the plant. On October 6, 1942, my father was inducted into the
Army.
Sometime after my father left for the
service, my mother came to work in the plant as a salaried clerk in the
Materials Control Department. Her job responsibility was to keep
track of the B-29 components being made in the plant, including engine
nacelles and control surfaces. After having several depression-era low paying jobs after graduating
from Lansing Central High School, doing war work at Fisher Body was a
great opportunity for her.
My father returned to work after separating
from the Army on February 6, 1946. At some point, my parents met
while working in the plant, and were married. My mother did what
was the norm during that era. She became a stay-at-home-mother and
housewife. My father stayed at Lansing Fisher Body until he retired on
August 1, 1976.

Lansing Fisher Body circa 1973. This
is how I remember the plant; and how it looked during the "Golden Years"
of General Motors during the 1950s, 60s and early 70s. It was
because of this plant that my sister and I always had food to eat and
clothes to wear. Because my father was on Plant Protection, he
worked through several GM strikes while I was growing up. While
going to college, both my sister and I had summer jobs in the plant. During the 1960s, if your mother or father worked in the
plant, you could count on a summer job while in college. Also,
Michigan State football players who needed summer jobs were
given special consideration. There were several such athletes in the plant during the summers I
worked there.
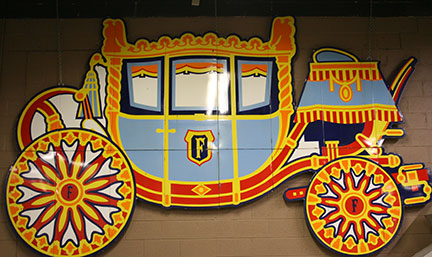
This is the Fisher Body Coach Emblem that was on the
south side of the Lansing Fisher Body Plant facing Michigan Ave and
Lansing Sexton High School. Now the emblem resides in the RE Olds
Museum in downtown Lansing. Author's Photo.
Early History: In the photos below, not only does the plant
grow over time, but the neighborhood to the east of the plant does as
well.
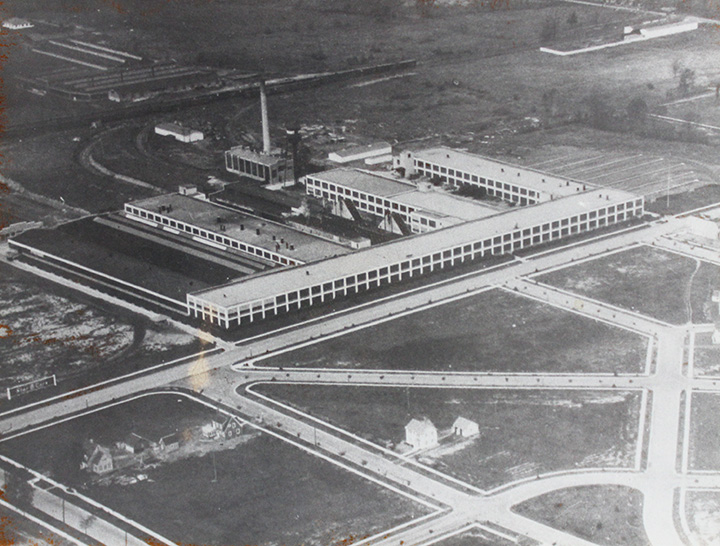
The building that later became the Lansing Fisher Body Plant was built
in 1922 as an automobile assembly plant for the Durant Motor Company.
The plant was built on 152 acres, and employed 3,000
workers when it opened. This aerial looking north-west shows what the plant looked like in 1922
after it was built. The plant was far smaller than it was when
razed in 2007, as there were many additions over the years.
Building One was the nomenclature for the long building facing Verlinden Avenue. The
empty area on the south or left end of the photo would be the location
of a post WWII two story addition known as Building 3X. It contained
the body shop on the first floor and final trim shop on the second.
The 1928 photo below shows the addition going up on the north end of the
building that is a parking lot in this photo.
Verlinden Avenue is out in front,
and Michigan Avenue is the road along the bottom of the photo.
Three houses were built across the street from the
plant, and trees have been planted in the new
neighborhood. When I was a child. this area was all houses.
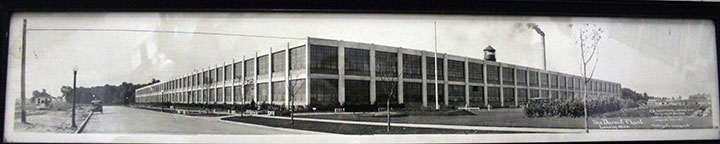
This photo, taken between 1922 and 1928, is
looking south down Verlinden Ave. while the plant was still part of
Durant Motors. The trees at the south end of Verlinden Ave. are
where my high school, J.W. Sexton, would be built during World War Two.
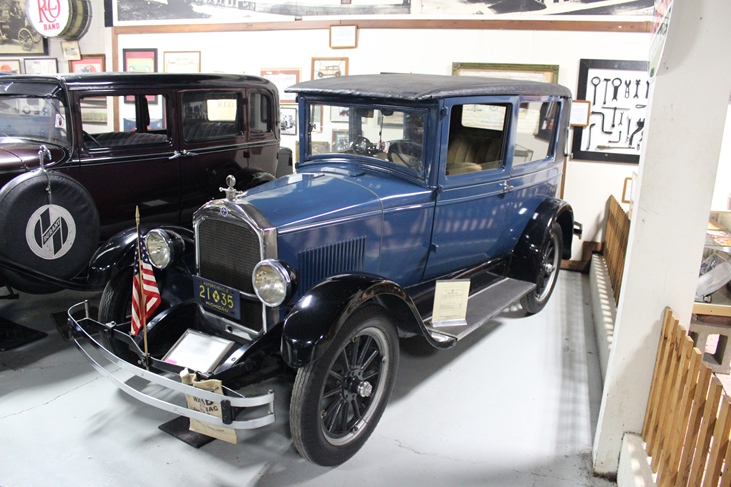
This 1926 Durant Star was built by the
Durant Motor Company in what later became the Lansing Fisher Body Plant.
The Star was the low priced line of vehicles produced by Durant, for
which production ran from 1922 to 1928 at Lansing. This particular
vehicle is on display and owned by the RE Olds Museum in Lansing, MI.
It
is an un-restored original. Author's photo.
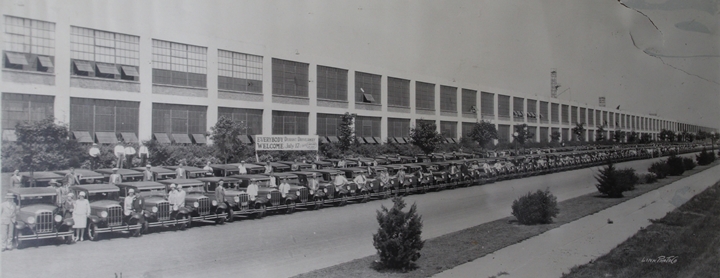
How cool is this? For as far as can be
seen looking north up Verlinden Avenue, there is a double row of Durant
automobiles lined up in front of the plant. Each car had a driver
that drove it to its new owner. Photo added 12-24-2021.
The date was July 17, 1928. Photo added 12-24-2021.
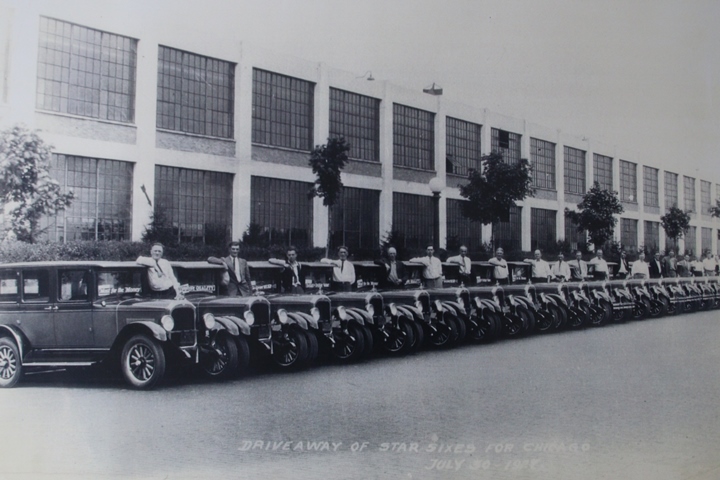
A year earlier, on July 30, 1927, at
least nineteen Durant Star Sixes were lined up in front of the Durant
Motor Company on Verlinden Avenue in Lansing, MI. These vehicles
were all on their way to Chicago, IL. Photo added 12-24-2021.
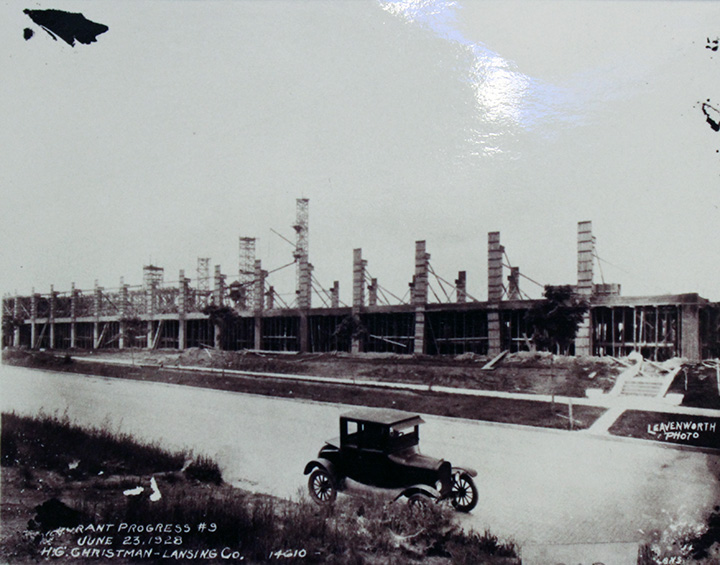
This 1928 photo shows the addition on the north end of the plant and
Building One. The stairs lead up to what would become the "front offices"
for the rest of the plant's existence.
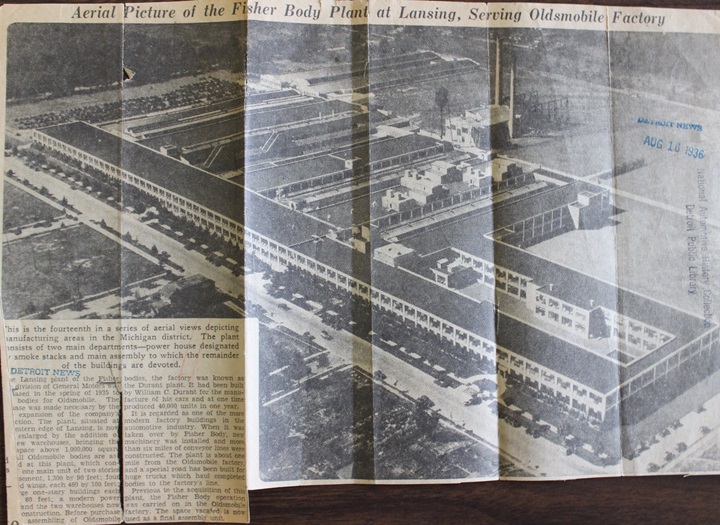
This newspaper photo shows the plant in
1936, one year after General Motors purchased it for Fisher Body.
Prior to the purchase of this plant, Fisher Body built its bodies for
Olds in leased space in the Oldsmobile plant. At this time, the
plant was 1,000,000 square feet, had six miles of conveyor, and
supplied all of the Oldsmobile bodies. There was not a direct road
between the two plants, so a road was built between them. This
would be Clare Street and Olds Avenue.
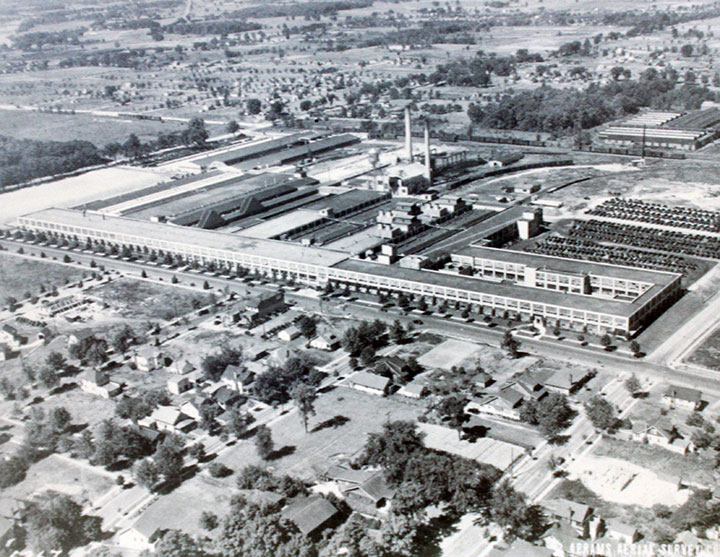
This is the Fisher Body Lansing Plant before World War Two. This
may have been taken at the same time as the photo above. The 1928
addition on the north or right end of the photo is easily visible along
with several other additions within the center of the plant complex.
During
summers while in college, I worked in this building. One of my jobs
was at the middle of the section at the right end (north) of the photo
on the second floor. There were two entrances along the front facing Verlinden Avenue.
One entrance towards the north (on the right) was
what we called "the front office" for the executives and some of the
office workers. The other entrance, in the middle of the plant at the intersection of
the two buildings facing the Verlinden Ave., was for the workers like my
father. The long buildings in the far upper left were known as
"cut and sew." Seat cushions and interior trim parts were made there until the late
1950's, when they became known as "the cushion room." "Cut and sew"
was moved to another plant and the seat cushions were then assembled
there.
On a related note, General Motors purchased the plant behind and across
the railroad tracks from RE Olds in 1940. It was originally built as a foundry in 1920 to hopefully provide
castings for General Motors. It went bankrupt several times and
was standing empty when GM
purchased it. It became Olds Plant 2 and was converted into a
forge plant to manufacture the 75mm and 155mm artillery shells
that Oldsmobile produced during World War Two. The Fisher Body Power House
supplied the steam for Olds Plant Two.
World War Two:
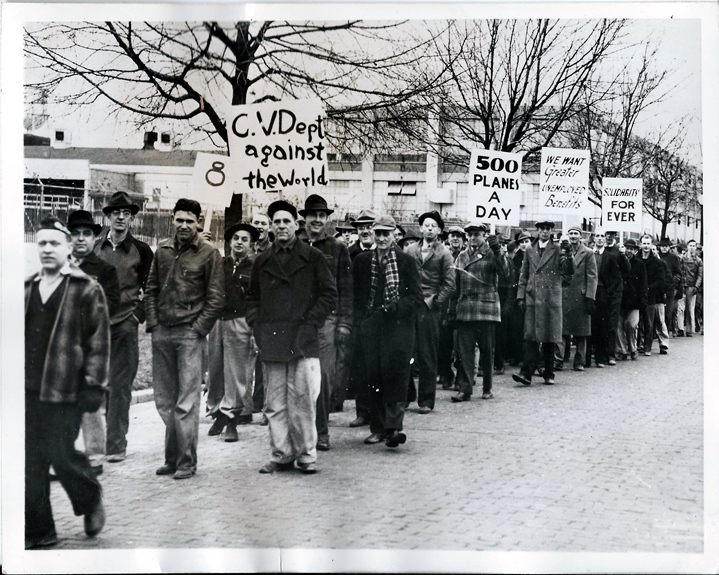
The March to the Michigan State Capital
building by 3,000 Fisher Body workers on January 20, 1942.
I had seen reference to this march of
Lansing Fisher Body workers in my early research on the plant but was
not able to obtain this photo until June of 2015. The date of this
photo is January 20, 1942. It was taken at the south end of the
Lansing Fisher Body Plant on Verlinden Avenue. It shows a small
portion of the 3,000 Fisher Body employees starting a march to the State
Capital a mile away to the east. The reason for the march was to
protest the impending job losses. Auto
production in the United States was coming to an end in February 1942. The workers were concerned for their jobs, because as of
this point in time there were no plans, or at least no plans that the
workers knew of, for war production in the plant. It was 44 days since the bombing of Pearl Harbor.
The
Arsenal of Democracy, for which the Lansing plant was later an important
part, was just starting to come to life.
The worker's concerns were not without merit.
In February 1942, 500 workers were laid off from this plant. No doubt some of
those laid off were in this photo. When the laid off workers applied
for work at The Reo in Lansing, only 95 were hired. Meanwhile, Reo
hired 400 women who had not previously worked in a factory.
Also, some of the men in this photo may not
have known it, but worrying about a job was not necessary. Uncle
Sam found jobs for them carrying M1 rifles after they were drafted into
the US Army. One of the big issues for all companies during World
War Two
was the constant drafting of experienced workers into
the Army.
My grandfather was employed at the plant in
January of 1942 and he is somewhere in this group of workers.
There are several interesting items to note in this photo. One worker is carrying a sign that states "C.V. dept
against the world". Before the advent of air conditioning along
with "flow through ventilation" being standard on vehicles, automobiles
and trucks had corner vents in the front side windows for ventilation.
The corner vents were known as C.V.s in the auto industry.
It is January in Michigan and there is no snow
on the ground.
Another worker has a sign that says "500
planes per day." This is a reference to the plan that UAW
president Walter Reuther proposed to keep auto plants running and
workers in jobs. Walter Reuther proposed this over a year
earlier when he felt that the unused capacity of the auto industry could
be harnessed to make 500 metal fighter aircraft and continue to produce
automobiles at the same time. Mr. Reuther, along with his
automobile company management contemporaries, totally
underestimated the complexity of building not only fighters, but any
aircraft during World War Two. Lansing Fisher Body would go on to produce
components for both the XP-75 fighter and B-29 bomber, while the Eastern
Aircraft Division of General Motors would produce 5,837 FM-1 and FM-2
Wildcat Fighters for the U.S. Navy over a two year period.
Note the pavement of Verlinden Avenue.
It is all hand-laid brick. Eighty years later, one may ask why was
it brick? Why was it hand laid? This was common practice
during the Great Depression, as many projects to put unemployed men to
work were to pave roads with brick, as this was labor
intensive. My
grandfather did not lay the brick on Verlinden Avenue, but he did lay the
brick on South Cedar Street in Lansing. That public works project put him back to work during
the Depression.
And speaking of the brick of Verlinden Avenue,
I can still remember driving down the street and hearing the roar of the
bricks under the tires, as I did my first of three road trips during
Driver's Training at Sexton High School in the summer of 1965. I was the first of the three students in
an Oldsmobile 88 to drive that day. Mr. James Bond (Imagine having this name in
the mid-1960s!) was the instructor, and he had to slow me down a bit, as I
was not paying any attention to my speed as I went down Verlinden.
Some years later the bricks were paved over
with asphalt.
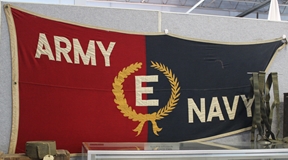
Lansing Fisher Body received the Army-Navy
"E" Award in June 1945.
Lansing Fisher Body World War Two Products: The plant produced $43 million in war products between
1942 and 1945, divided into three different product groups. The
aircraft group consisted of B-29 control surfaces and engine nacelles,
aircraft tail sections, and XP-75 aircraft parts and assemblies.
The armor group was made up of M4, M18, M24, M26, and experimental tank
parts. The last group was carriages for (2,359) 90mm
anti-aircraft guns, and components for 5 inch naval guns mounts.
Very little information is available on what
the plant specifically built during World War Two. The following two
sources have provided what information I have been able to find.
From "Fisher Body Craftsmanship Goes to War": B-29, XP-75
aircraft parts
and assemblies. M4, M8, M24, and experimental tank parts.
90mm anti-aircraft gun parts and five-inch naval gun parts. On page 35, it states:
"In September (1943) Cadillac requested further assistance on the M24 in
welding a number of major hull assemblies. The work was assigned
to the Fisher Body plant in Lansing."
From "UAW Local 602 records": 90mm gun
carriages, tail sections for aircraft, gun mounts, hulls for tank
destroyers, small parts for Army aircraft. First Navy contract was
for five-inch naval gun mounts. Parts for XP-75 aircraft.
The Lansing Fisher Body Plant World War Two
Chronology: As determined from Local 602 records.
1942-1943:
Aircraft Tail sections, gun mounts (90mm), hulls
for tank destroyers, small parts for aircraft, parts for XP-75 "Eagle".
It is unknown for which aircraft types the tail sections or small parts were
built. They could have been one and the same for the
XP-75. The hulls for the tank destroyers were most likely for the
M10 "Wolverine" being built at Fisher Body Grand Blanc, MI.
Production of the M10 lasted from September 1942 to December1943.
Lansing could have also worked on the M-18 Hellcat built by Buick
from July 1943 to October 1944. Grand Blanc built many of the hulls and
turrets for the M-18, and could very well have sub-contracted some of
the work to Lansing.
1942-1945:
B-29 control surfaces and nacelles,
five inch naval gun mounts, assemblies for various type tanks.
The Flint Journal announced on
June 6, 1945 that work on the B-29 and the heavy tank project would
cease at the Lansing Fisher Body Plant at the end of July 1945, in order
to make way for the return of automotive production. Of interest
is that the heavy tank was
the M26 Pershing, which is not noted in either the Local 602 or Fisher
Body documentation. The Lansing M26 work would have been for
Fisher Body Grand Blanc, which was building the tank.
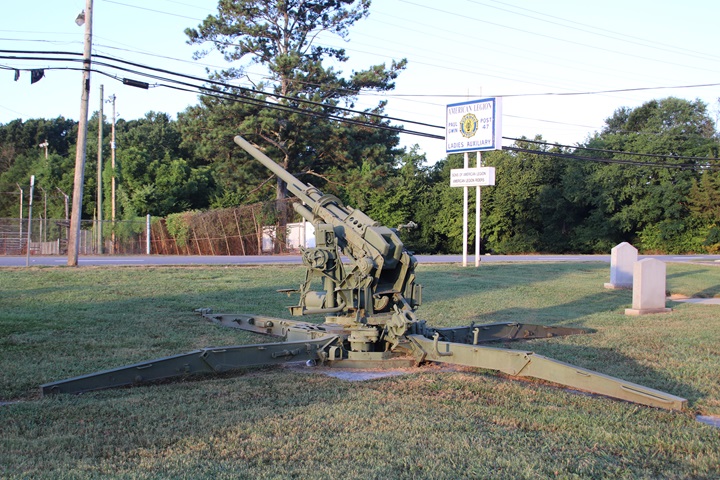
The first war contract for Lansing Fisher Body in 1942 was for 90mm
anti-aircraft gun carriages like the one seen here. Author's photo
added 11-26-2020.
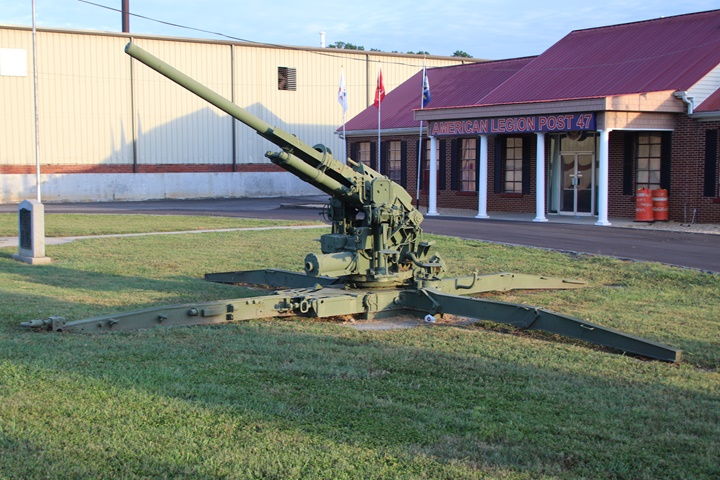
The plant had 4,500 employees
before the war and only 600 to 1,700 during 1942. The plant was idle
for several months before the work for this project came in.
The parts made at Lansing Fisher Body then went to Fisher Body Pontiac.
There, 2,359 of the weapons were produced. Author's photo added
11-26-2020.
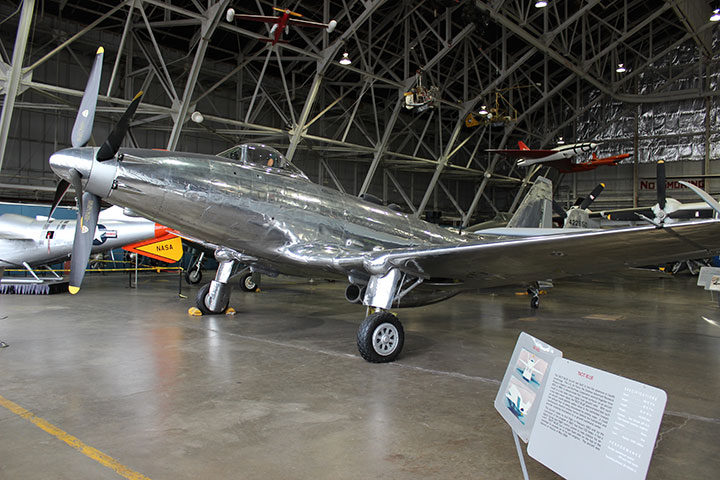
Lansing assembled the vertical stabilizer, horizontal stabilizer, tail
cone, rudder, elevator, trim tabs, ailerons, and flaps for the Fisher Body XP-75
and P-75A.
105,000 square feet, or 10% of the
plant's area, was allocated for this work. This photo shows the
only surviving P-75A at the National Museum of the United States Air
Force. This was taken when it was in the former annex hangar. Author's
photo.
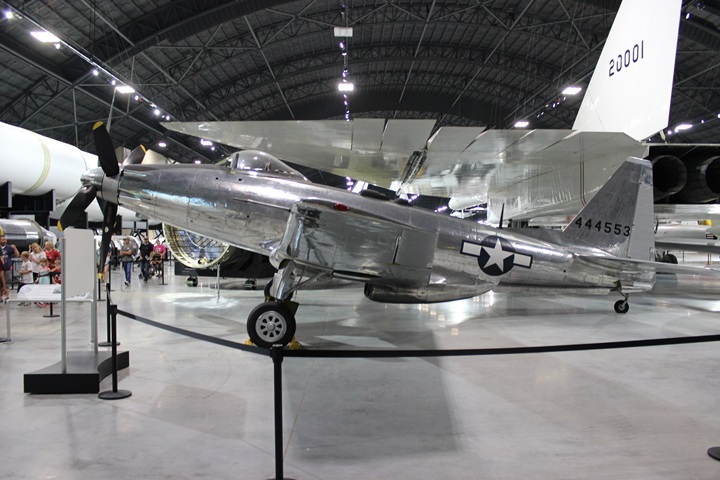
Only (8) XP-75s and (6) P-75s were built
during World War Two. While
only fourteen total airframes were built, Lansing and other Fisher Body
plants were planning and producing for a high production run. Many
more than fourteen sets of components were built. In 2015 the
Fisher P-75A was moved to the main museum complex. Author's
photo added 2-15-2021.
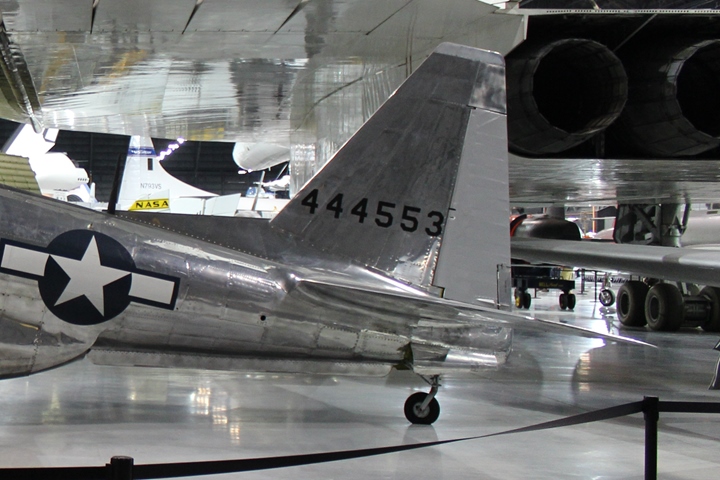
This photo shows the horizontal and vertical
stabilizers along with the rudder. The small trim tab can be seen
at the bottom of the rudder. They and the elevators were all
assembled at Lansing Fisher Body. Author's photo added
2-15-2021.
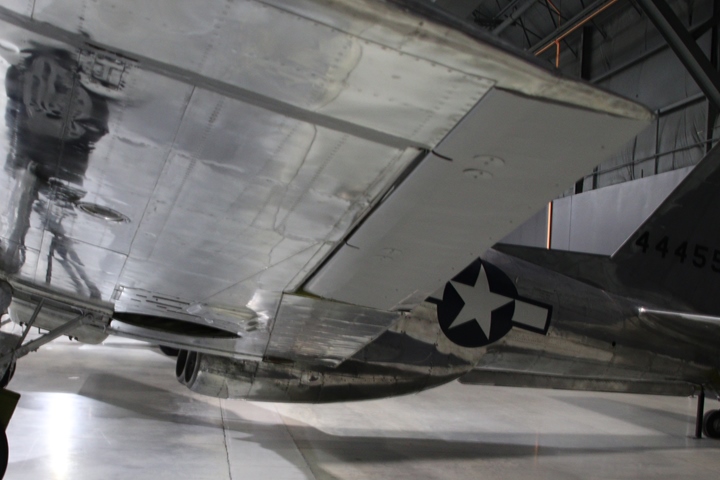
The Lansing Fisher Body-built
ailerons and flaps can be seen In this photo. The ailerons are nearest the end
of the wing. Author's photo added 2-15-2021.

Lansing built parts for the M4 Sherman. It is unknown which parts
were made in the plant. It can be assumed that whatever was made
in the plant was sent to the Fisher Body Tank Arsenal in Grand Blanc, MI,
60 miles away. Of the 49,234 Sherman tanks built by ten different
manufacturers, this particular Grand Blanc-built M4A3 Sherman is on
display in downtown Bastogne, Belgium. Bastogne was the center of
the fighting during the famous Battle of the Bulge in December 1944.
The road intersection in the town where this M4A3 now resides
was an important road junction for the German battle plan to be
successful. The road junction never fell into enemy hands; and this
tank was one of many that helped the 82nd Airborne defend the town.
It was knocked out of action during the battle and then put on display
by the residents of Bastogne. Author's Photo.
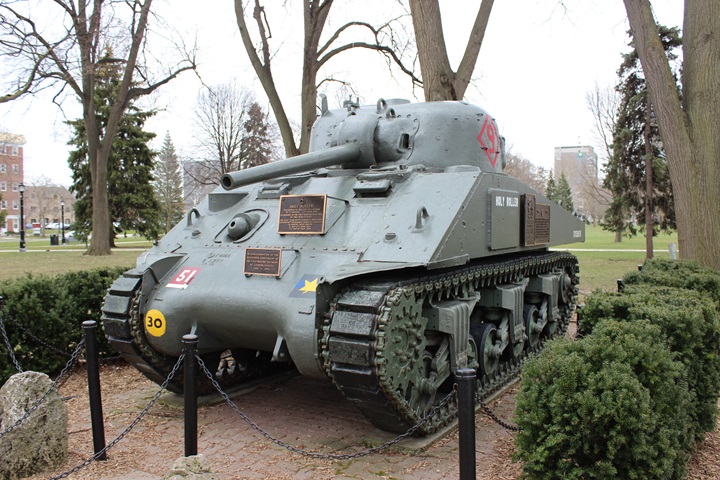
This M4A2 is the oldest Fisher Body-built tank in North America, and is on display at Victoria Park in
London, Ontario. It came off the Grand Blanc assembly line in
September 1942. It landed with the Canadian Army at Normandy, and
then fought its way across Europe until the end of the war. It
survived the many battles it was in, and then came back to Canada.
Lansing Fisher Body may have built components for this tank in 1942.
Author's Photo.
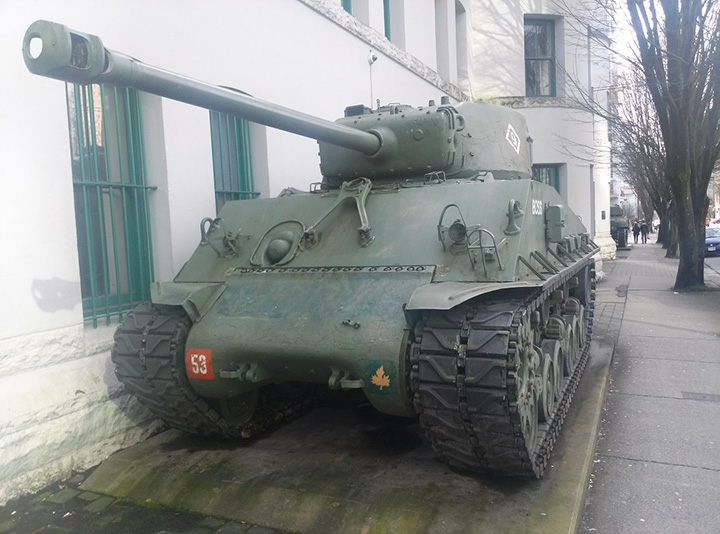
Grand Blanc also built the M4A2 Sherman, as
seen here in downtown Vancouver, BC. Lansing could have also
helped build this late model Sherman tank. Photo courtesy of David
Jackson, Jr.
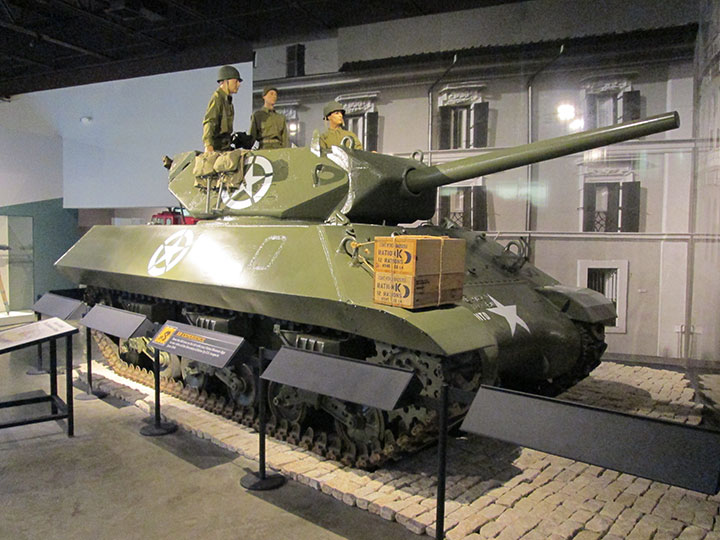
This Fisher Body-built M10 "Wolverine" tank
destroyer is on display at the Patton Museum at Fort Knox, KY. Author's
photo.
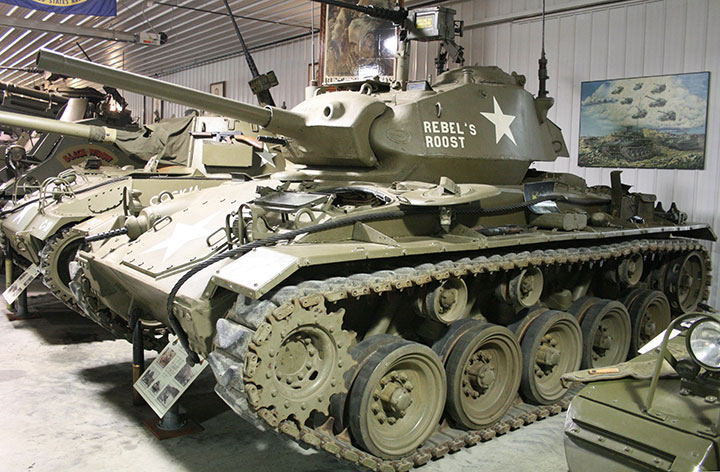
The Cadillac-built M24 Chaffee also had parts in it made by Lansing Fisher Body.
Work was assigned to Lansing in September 1943 for the welding of hull
assembly components. This particular Chaffee is actually a combat veteran from the Korean
War, where it served with the US Marines. It was captured by the Chinese,
and then recaptured by the US Marines. Author's photo from the
former Ropkey Armor Museum in Crawfordsville, IN.
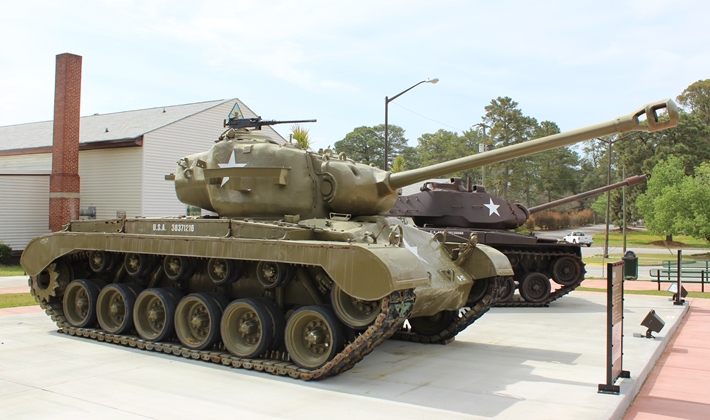
This is a Fisher Body Grand Blanc-built M26 "Pershing"
heavy tank. At the end of the war, Lansing was involved with the
heavy tank program until the end of July 1945. Author's
photo added 11-10-2017.
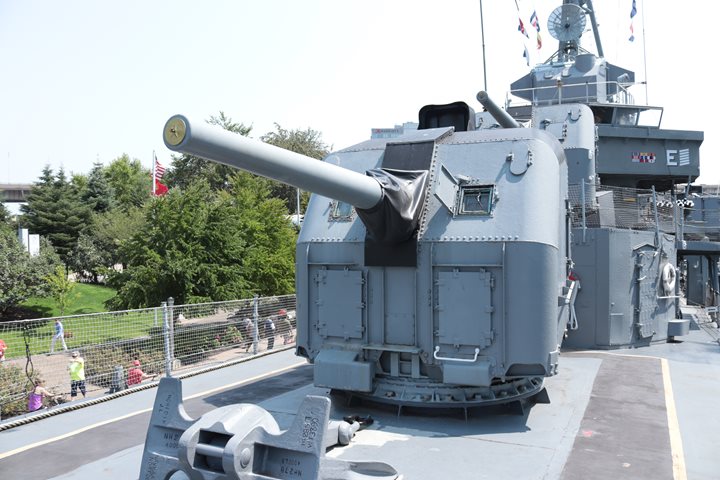
Lansing's only Navy contract was to fabricate portions of the five inch
naval gun mount. The Fisher Body plant in Pontiac did the final assembly
on the mounts. This five inch gun can be seen at the USS Sullivans
at the Buffalo and Erie County Naval and Military Park in Buffalo, NY.
Author's photo added 11-10-2017.
The B-29 Program at Lansing Fisher Body:
This is what my mother worked on. It was her responsibility in
Material Control to keep track of the assemblies being built, to assure they would be shipped to the aircraft assembly plants on time.
Originally, Lansing allocated 195,800 square
feet for the production of ailerons, rudders, and elevators. This
was 18% of the 1,066,667 square feet of the plant.
Lansing B-29 Project Scheduled Production
As of February 1944 |
B-29 Assembly Plant |
Boeing-Renton, WA |
Boeing-Wichita, KS |
Bell-Marietta, GA |
Martin-Omaha, NE |
Totals |
Nacelles (With Cleveland #1) |
2,700 |
1,464 |
400 |
200 |
4,764 |
Ailerons, Rudders, and Elevators |
300 |
|
900 |
|
1,200 |
Note that Lansing and Cleveland #1
supplied nacelles to all four B-29 assembly plants.
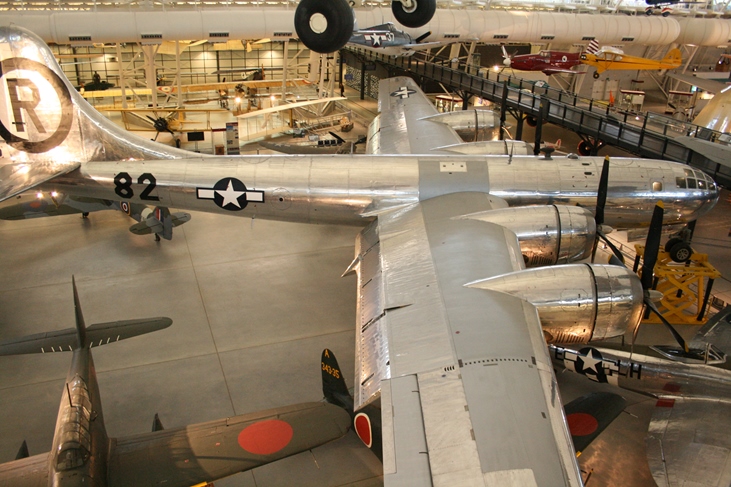
This is the B-29 Enola Gay which dropped the
first atomic bomb on Hiroshima, Japan. It is on display at the Udvar-Hazy Air and Space Museum in Virginia.
Of significance is that
Fisher Body supplied the engine nacelles to the Martin Omaha, NE plant
that built the Silverplate nuclear bombers. Both Fisher Body
Lansing and Cleveland Plant One built B-29 engine nacelles for the B-29s
built in Omaha. Therefore, there is the possibility that Lansing
built the engine nacelles on this aircraft.
Lansing built ailerons for the B-29, which is
the control surface at the bottom of the photo. Author's
photo.
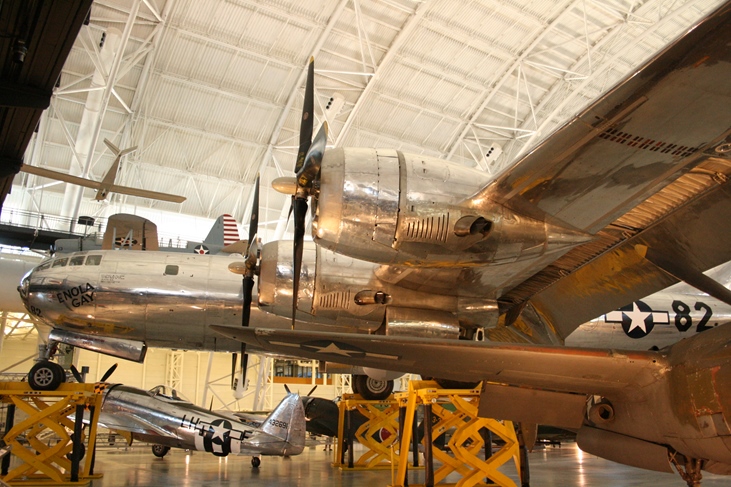
This photo gives a better look at the Fisher
Body-built engine nacelles on the Enola Gay. They were the most
complex part of the B-29 after the forward fuselage section and contained
over 1,300 subassemblies and weighed over a ton. Author's photo.
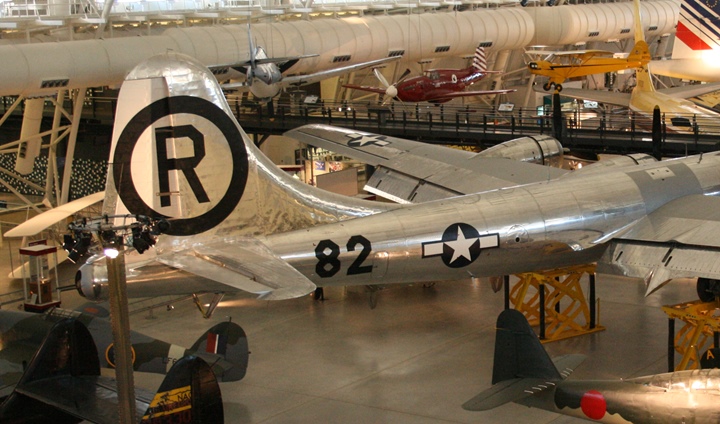
Lansing built rudders and elevators for the
B-29 bomber. Author's photo added 11-26-2020.
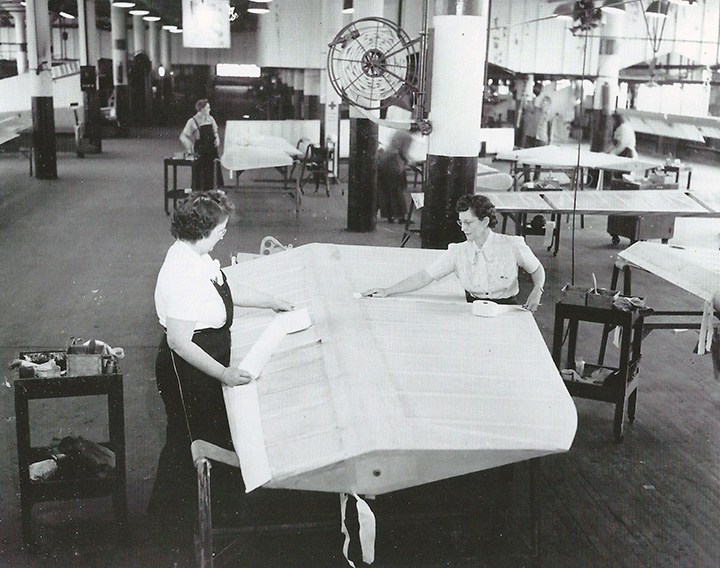
These women are working on a B-29 fabric covered rudder on the Lansing
Fisher Body plant floor. The woman on the left is applying tape
over the stitching that holds the fabric to the aluminum superstructure.
The stitching down the center has already been taped over. Once
this process is complete, a water-proof varnish is applied and then
cured.
While the B-29 was the most complex and advanced aircraft of the World
War Two
era, it still had fabric covered ailerons, elevators, and rudders.
In combat, the fabric actually had an advantage over aluminum covered
control surfaces. When enemy shells went through the fabric, it
did now leave any jagged edges like on the metal ones, which could then
jam the controls.
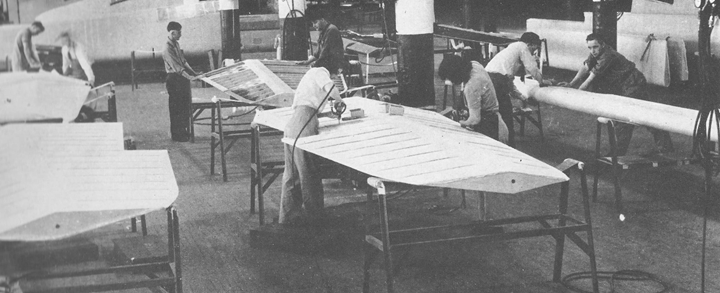
In this photo, both men and women are working
on the rudders in Lansing. They can be identified as rudders
due to the size of the cut-outs for the vertical trim tabs. The
completed rudders were then sent to the Fisher Body Plant #2 in
Cleveland, OH for assembly into the vertical stabilizer.
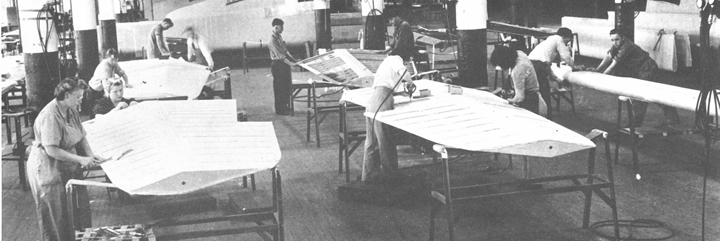
This shows a larger section of the plant
floor but is the same photo as above.
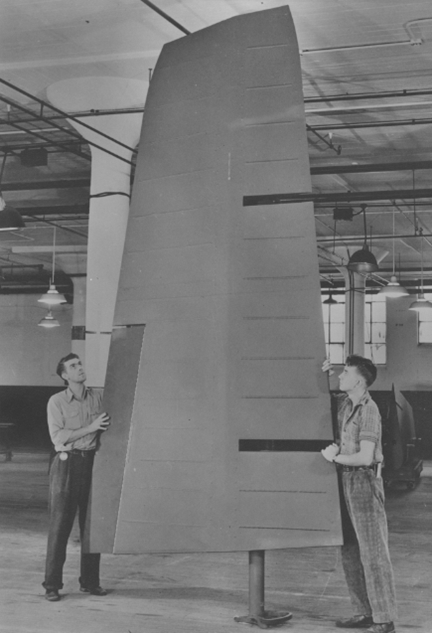
This photo of a B-29 rudder produced at
Lansing Fisher Body shows its size compared to the two workers. Photo added
11-26-2020.
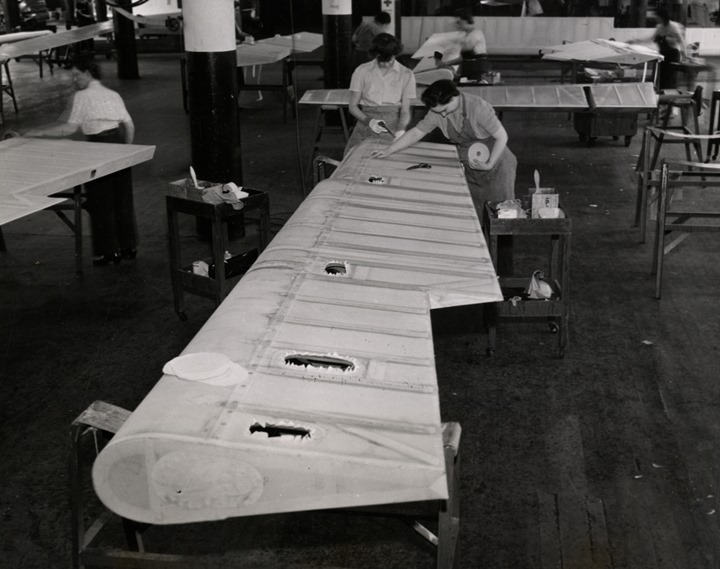
The workers In this photo are working on a
B-29 elevator. Photo added 12-25-2016.
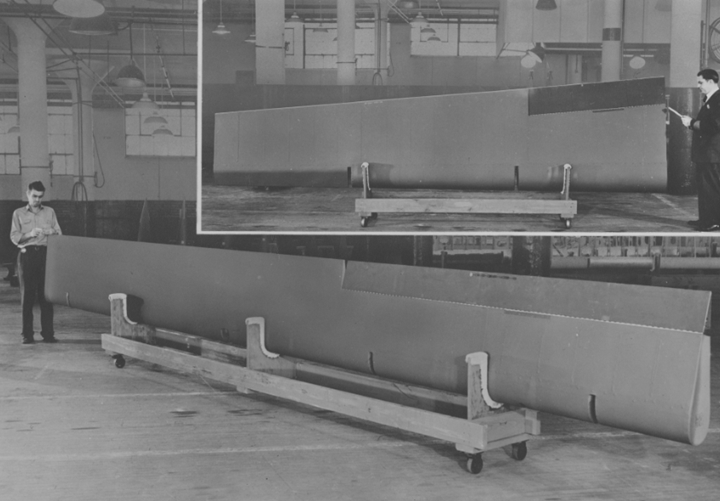
A completed B-29 aileron is in the bottom
half of the photo and a B-29 elevator is shown in the inset. Both
of these photos were taken at Lansing Fisher Body. Photo added
11-26-2020.
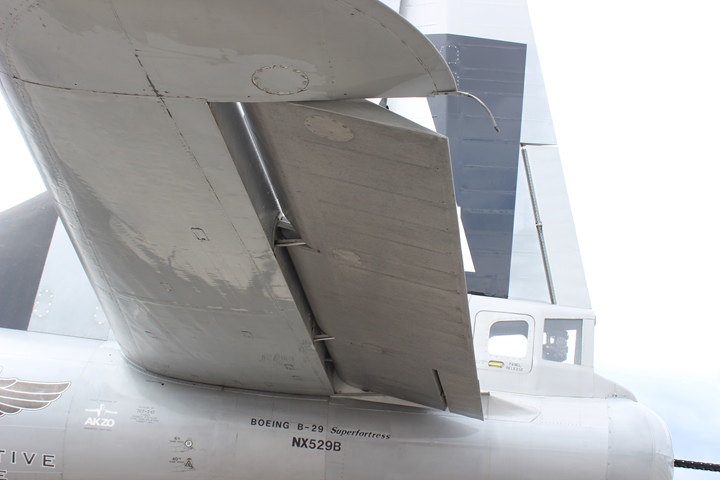
The tape covered areas where the fabric was
stitched to the ribs of the elevator can be seen on this B-29.
Author's photo.
The Lansing B-29 Nacelle Program:
Fisher Body committed to the United States Army Air Force for 290 B-29
ship-sets per month in 1945, which is 1,160 individual nacelles per
month. Fisher Body Cleveland Plant 1 had the capability of
producing 200 ship-sets and would reach that in January 1945.
Starting in December 1943, Lansing was also tooled up to
produce 90 ship-sets, or 360 individual nacelles per month. Production began
in May 1944 with full production being reached in July 1945. At
full production, Lansing produced 31% of the nacelles built by Fisher
Body.
60% of the Lansing plant was committed to
the production of the B-29 nacelles. This was 640,000 square feet.
The tooling for the B-29 nacelles in Lansing totaled 946 jigs, fixtures,
master gauges, and master plates which required 183,958 hours to build.
Lansing did not receive its Army-Navy "E"
Award until June 1945. It could very well be that it received the
award due to producing more B-29 nacelles ahead of the original
schedule.
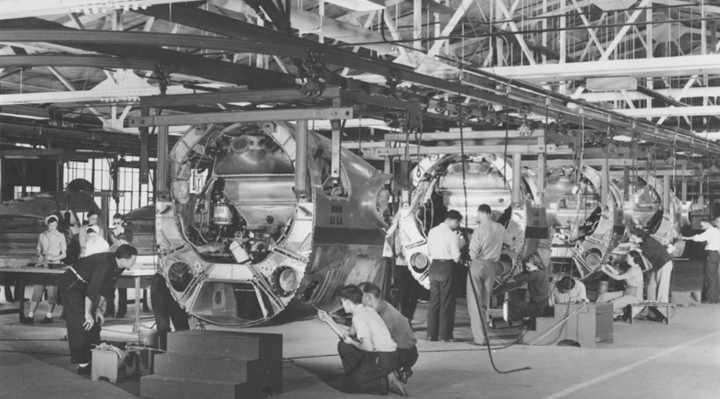
This is the only known photo of B-29 engine nacelles coming down the
monorail assembly line at Lansing Fisher Body. It is unknown what
percentage of the 13,772 Fisher Body-built B-29 engine nacelles were
made in Lansing. My mother's responsibility was to come out to this
assembly line and then verify by job number that it was on schedule to
be shipped to Omaha or one of the three other B-29 final assembly
plants in operation during World War Two.
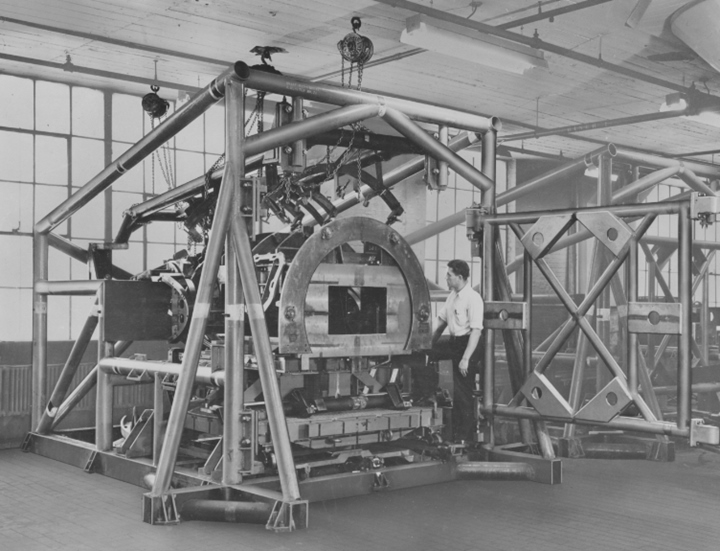
This master gauge is one of the 946 pieces
of equipment that needed to be built for Lansing to go into B-29 nacelle
production. Photo added 11-26-2020.
Post-World War Two:
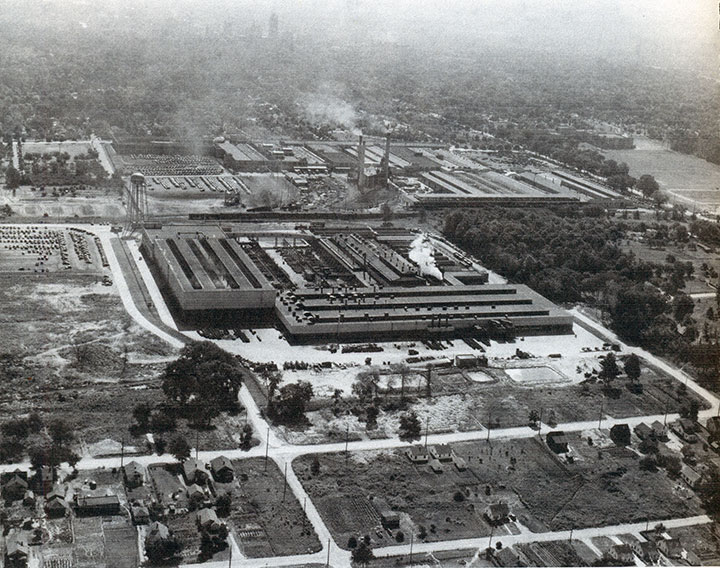
Oldsmobile Plant Number Two in 1945.
The photo is looking
east with Lansing Fisher Body behind it. The newly completed J.W.
Sexton High School, that I would attend 20 years later, is located in
the right hand corner. The gymnasium is visible on the south end. The
Fisher Body plant's power house supplied steam to both plants.
Downtown Lansing is in
the distance through the smoky haze.
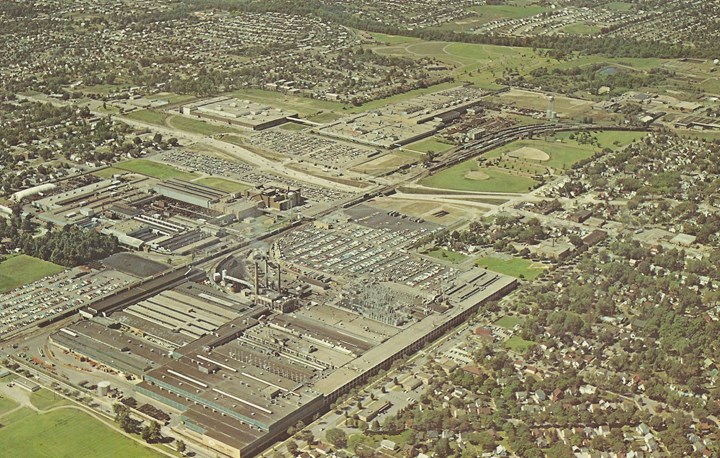
Fisher Body Lansing in 1973.
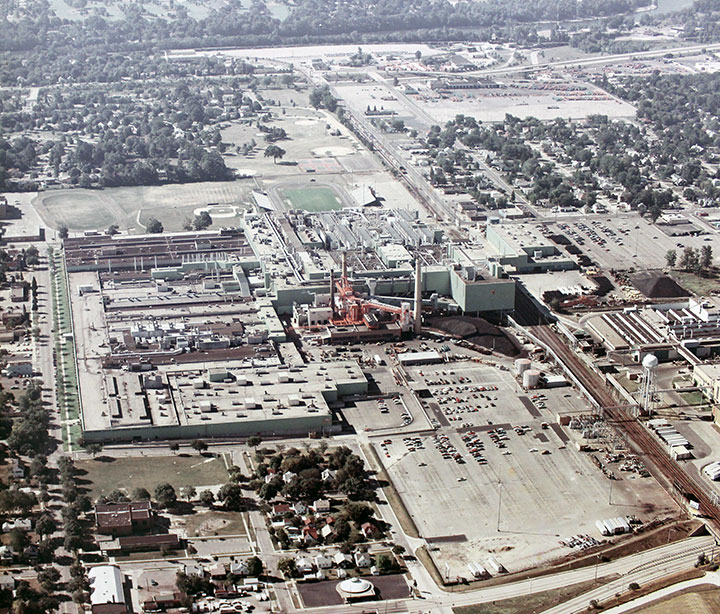
This is a post-1975 photo looking south. Verlinden Avenue is on
the left. J.W. Sexton Memorial Stadium can be seen to the south of
the plant along with the high school track. At this point, all of
the additions to the plant have been made.
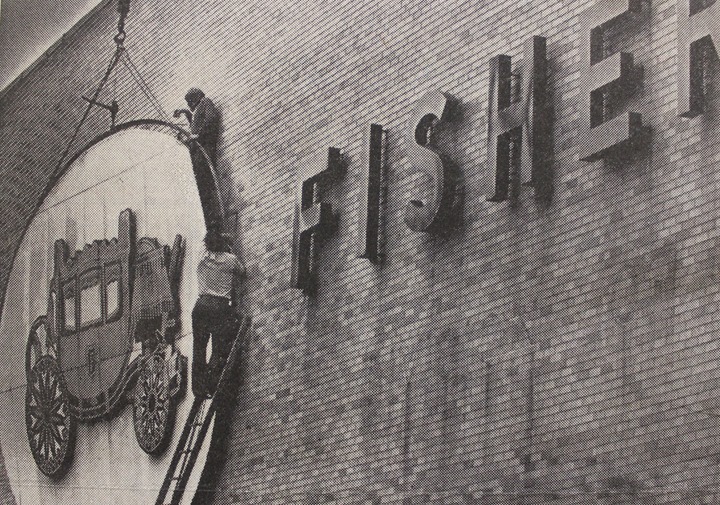
The Fisher Body Coach had been on the south side of building 3X since it
was added in 1960. Plant millwrights are removing both the sign and the name
"Fisher Body" on August 1, 1985. It then became the BOC Lansing Body
Assembly Plant.
How times have changed. The millwrights
do not have any safety harnesses on in case they were to fall.
Today's safety protocols require harnesses for this type of job.
Today the work would be done from a bucket truck.
The travesty of eliminating Fisher Body did not have to happen! In
1981 Roger Smith became Chairman of GM after being a bean counter for GM
in New York City. He wouldn't have known a body in white if one had
been shoved up his... ! Well you know what I mean. He was a
disaster for GM. He thought he was the smartest S.O.B on the face
of earth. While everyone could agree with the S.O.B part, only his
mother thought he was the smartest. And she only thought it true about half the
time! He was like a little banty rooster strutting around the GM
barnyard, making lots of noise, but not knowing how to run the world's
largest auto company. It was his harebrained idea to take Fisher
Body, the premier division in the company, destroy it, and combine it
into other divisions.
Instead of spending GM's money on new products
and technology, he went out and bought other companies to try
and fix the problems. One of the worst purchases was that of
computer software company EDS. This was the ultimate train wreck,
and caused dissention among the employees for years to come. Along
with EDS came its chairman, Ross Perot, who also thought he was the
smartest S.O.B. on the face of the earth. Because of this, he
forgot for whom he was working for, and thought he was the person running
General Motors. We ended up with two banty roosters strutting around the
GM barnyard, squabbling with each other, and screwing things up.
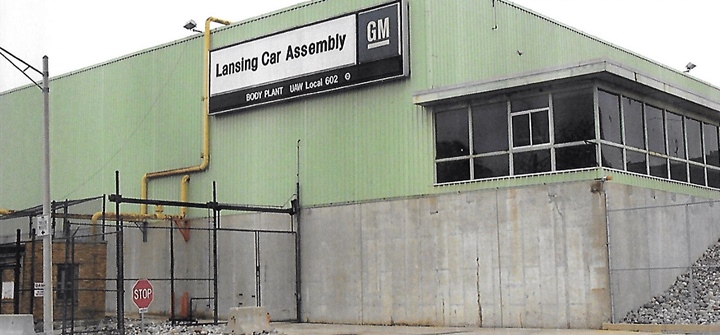
After the Fisher Body name was
gone, the plant was known as the Body Plant of Lansing Car Assembly.
The former Oldsmobile plant was final assembly. This is the
security gate after the modernization and expansion of the plant in
1975. The original security gate was formerly a stand-alone
building and was Gate 9. The area to the east of this location is
shown in the next photo.
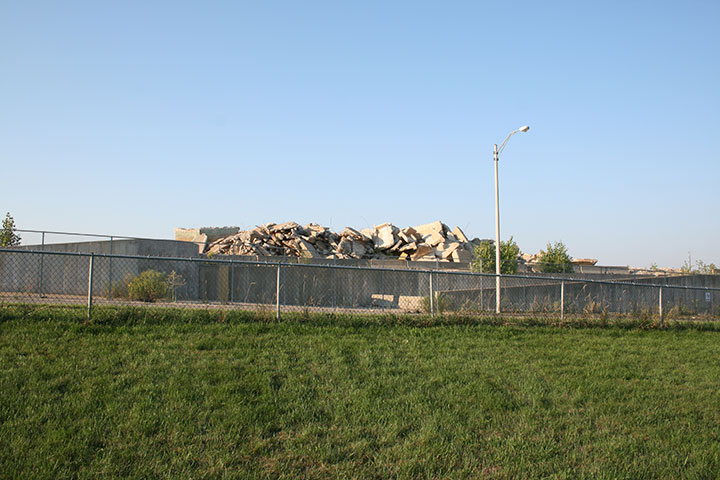
This is what is left of the north end of the
plant in 2012. I used to have
a work station where the rubble stands today, working on Olds Vista
Cruiser station wagons on the second floor. Author's Photo.
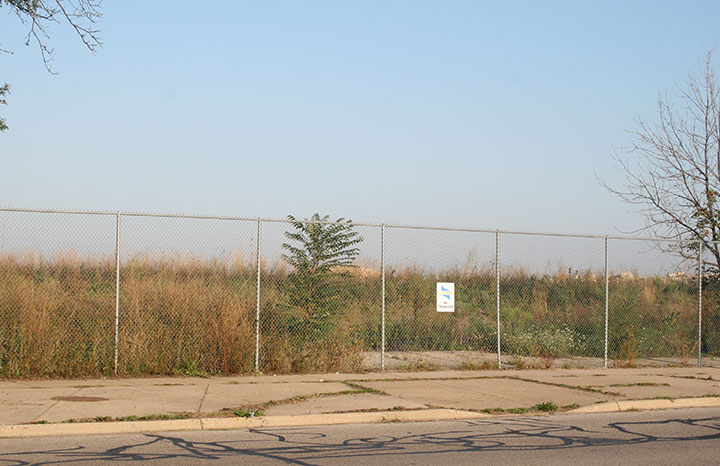
The south entrance on Verlinden Ave. was
located where the slab of concrete protrudes into the grass. Everyone who worked at the plant used this entrance to
hire in, because the Personnel Department was located here.
One went down the steps, past security, and then up into Personnel.
Many of my family members, including both of my parents, my sister, and
my grandfather, and I passed through this gate to get to work. The plant was razed in 2007.
Author's Photo from 2012.
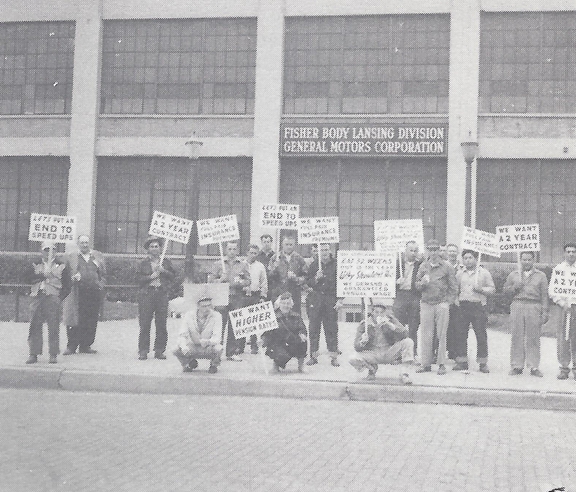
This photo shows strikers in front of the
above described entrance. Note that the bricks have not yet been
paved over on Verlinden Avenue. Photo courtesy of UAW 602.
1973 Lansing Fisher Body Open House Brochure
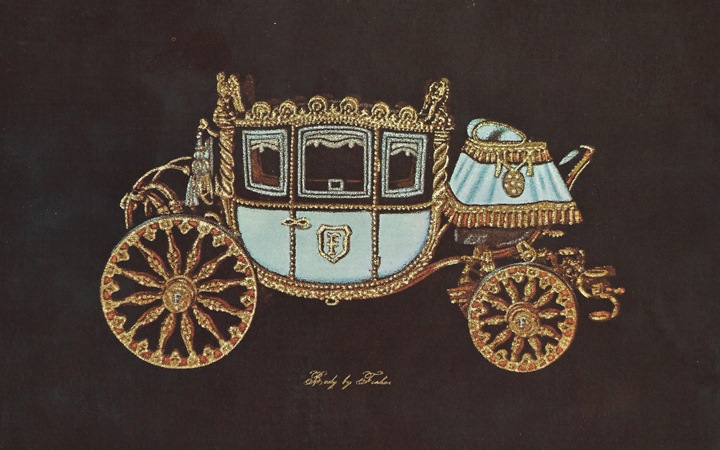
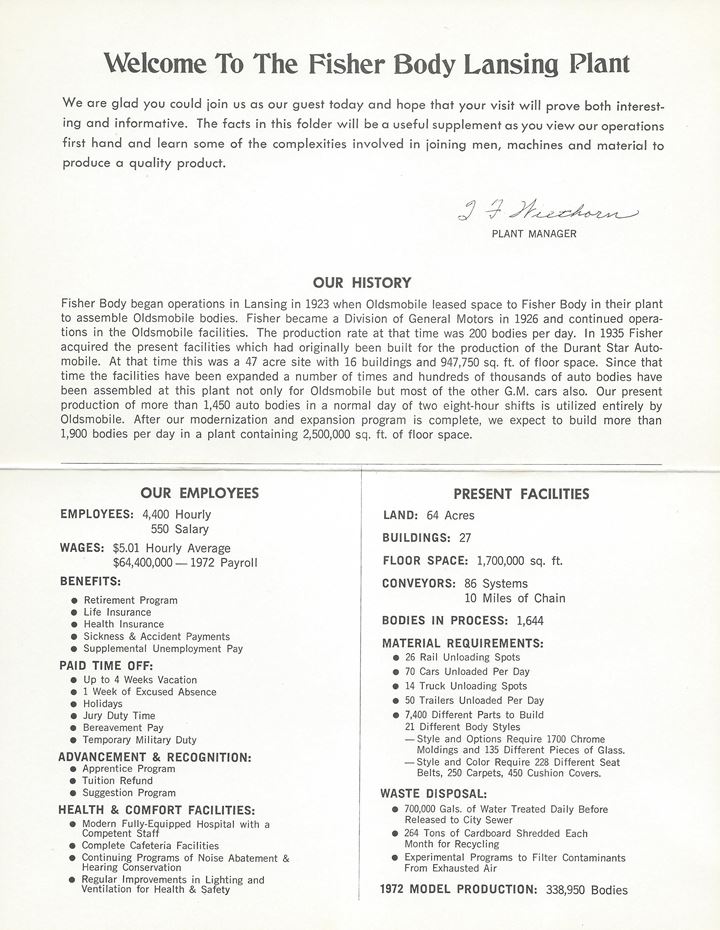
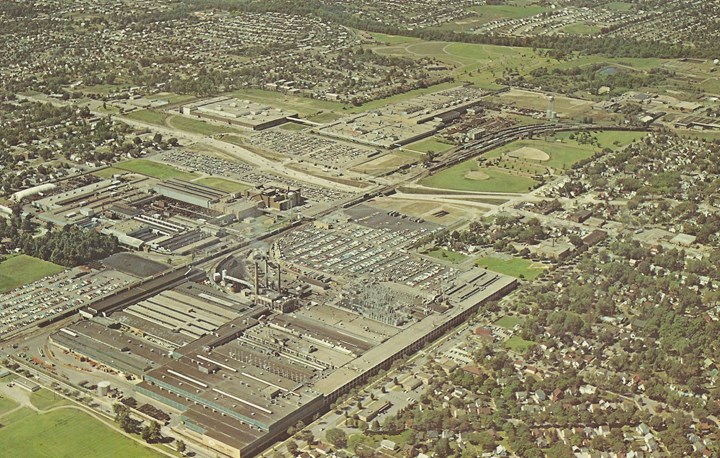
May "The Shop" Rest in Peace!
Other Lansing Companies that
contributed to winning World War Two
|