Saginaw
Malleable Iron Division of General
Motors Corporation in World War Two / WWII
Saginaw, MI
1917-1946
Rest in Peace
This page updated 10-5-2017.
Saginaw Malleable Iron Division (SMI) was
formed in 1917 and became part of General Motors in 1919, at which point
there were three plants in the Division, Saginaw Malleable Iron, a grey
iron Foundry, which became part of Chevrolet and Saginaw Steering Gear,
which became its own division in 1921. In 1946 Saginaw Malleable
Iron Division was folded into the new Central Foundry Division of
General Motors.
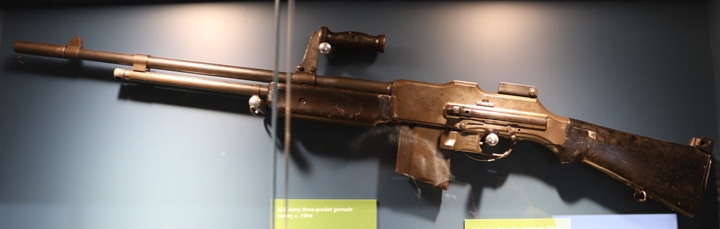
This Browning Automatic Rifle is on display
at the 4th Infantry Division and Fort Carson Museum in Colorado Springs,
CO. Author's photo
added 10-5-2017.
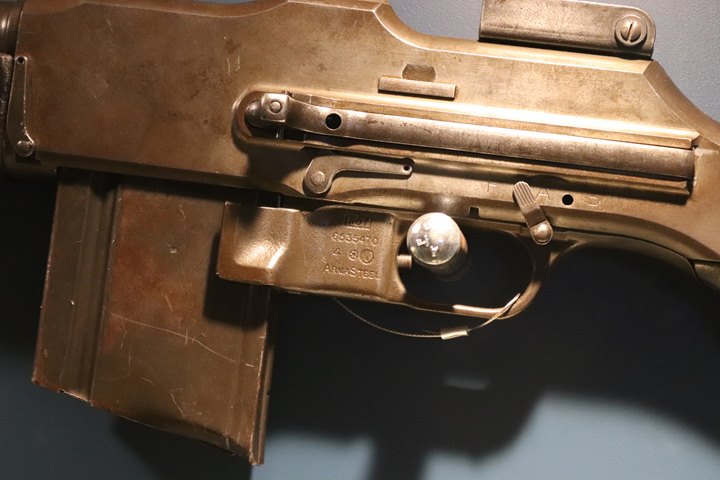
This BAR has the ArmaSteel receiver is
well marked as such. The ArmaSteel cast receiver saved over
15 pounds of material over the machined steel part. Saginaw
Malleable Iron was the
only auto company to make parts for this important weapon which brought
automatic weapons fire down to the squad level. See page 15 below.
Author's photo added 10-5-2017.
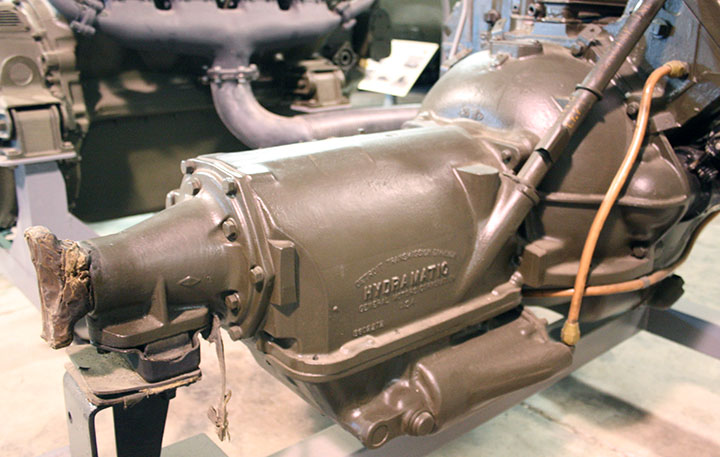
Saginaw Malleable Iron made parts for the
Hydra-Matic transmission built by the Detroit Transmission Division of
GM. Author's photo added 1-25-2017.
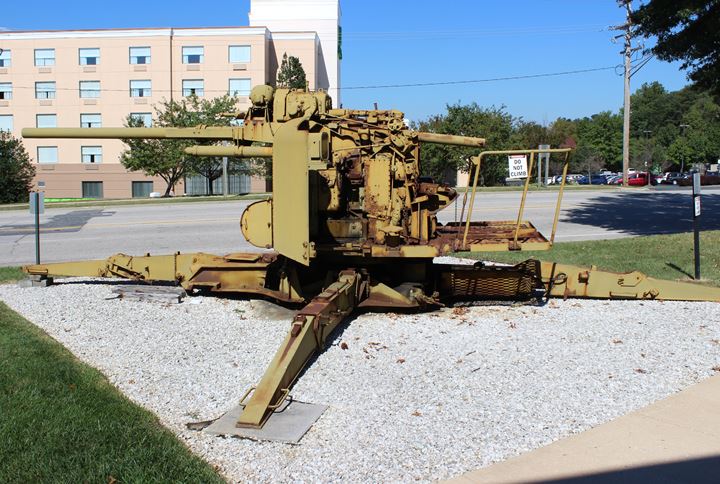
Saginaw Malleable Iron produced parts for
the 90mm anti-aircraft gun mounts. Author's photo added 1-25-2017.
The story of Saginaw Malleable Iron in World
War Two as outlined in the 48 page book published 1944 after the
Normandy Invasion on June 6, 1944 (Page 4 mentions the Normandy
Invasion) is not only a storehouse of information on the products it
produced to help win the war, but is also an insight into the state of
not only the iron and steel casting technology of the era, but gives a
comparison to the technology the company used in the First World War
some 20 years earlier. In 1944 the Division had 3,500 workers.
The book is divided into several distinct
sections:
Pages 1-19 give an excellent overview of the
many different parts that went into a large variety of weapons, from the
small M1 Carbine to the diesel engines that powered many of US Navy's
submarines and LST landing ships.
Pages 20-23 cover the Division's sponsored
employee's recreational activities, suggestion program, medical
facilities. This information was included in all of the GM
Divisional books produced in the late 1943-early 1944 time frame.
Pages 24-29 is another boiler plate section,
this one includes the name of all of the men and women that used to work
at the Division and were serving in the various US armed forces during
the conflict, including photos of those that had been killed while in
the service.
Pages 30 and 31 show the plant expansions at
the Division in Saginaw as of early 1944.
Pages 32-43 are unique in all of the GM World
War Two booklets that were published during the war in that they show
the process improvement made in producing castings between World War 1
and World War Two. This section is not only for the person
interested in WWII but the history casting technology. A great
bonus section.
Pages 44-45 explain the expansion of the
Saginaw facility to meet the demands of the increased war production.
Pages 46-47
describe the new Danville, IL plant that was owned by the government and
managed by SMI for producing axle differential castings for General
Motors produced military trucks. Chevrolet and GMC produced a
total of 854,000trucks for the war effort and Danville was needed to
keep up with the supply of castings to Chevrolet, which then assembled
them and used them for their own trucks and also supplied them to
GMC.
Page 48. The traditional last page of
the GM WWII booklets end in stating war production would not stop until
final victory.
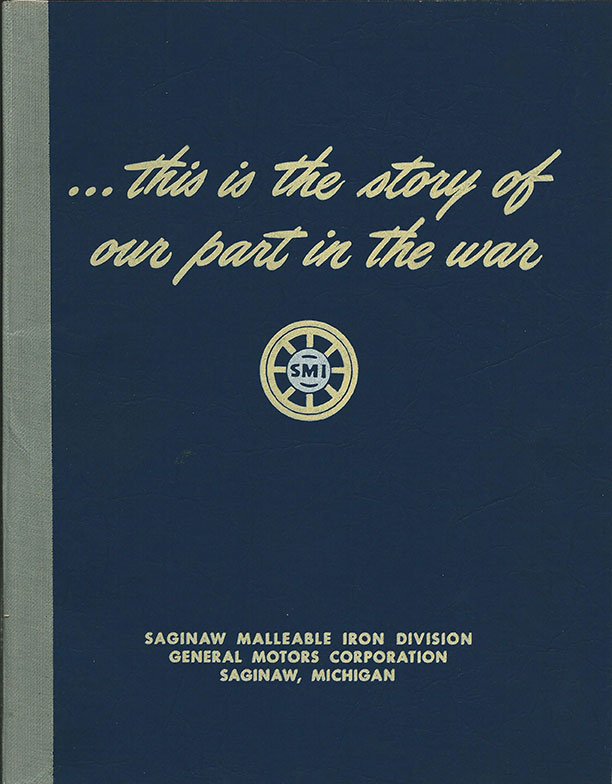
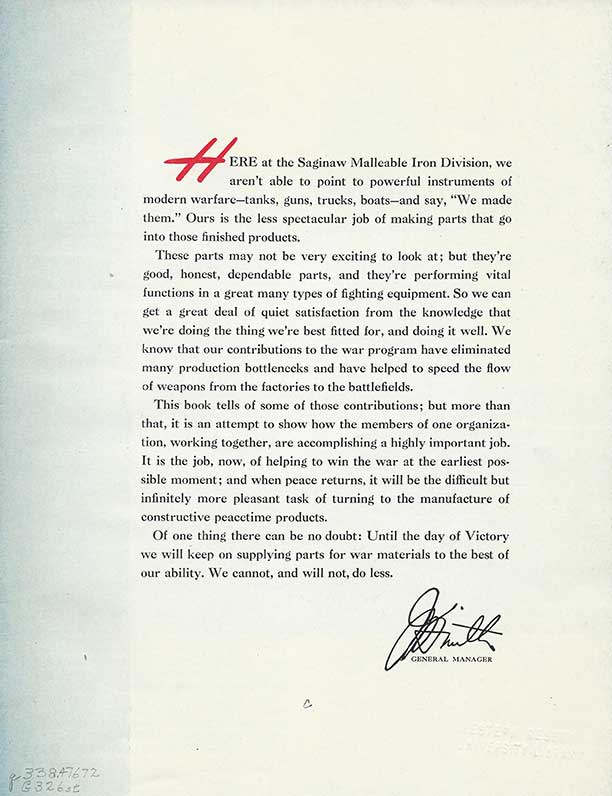
Page 1.
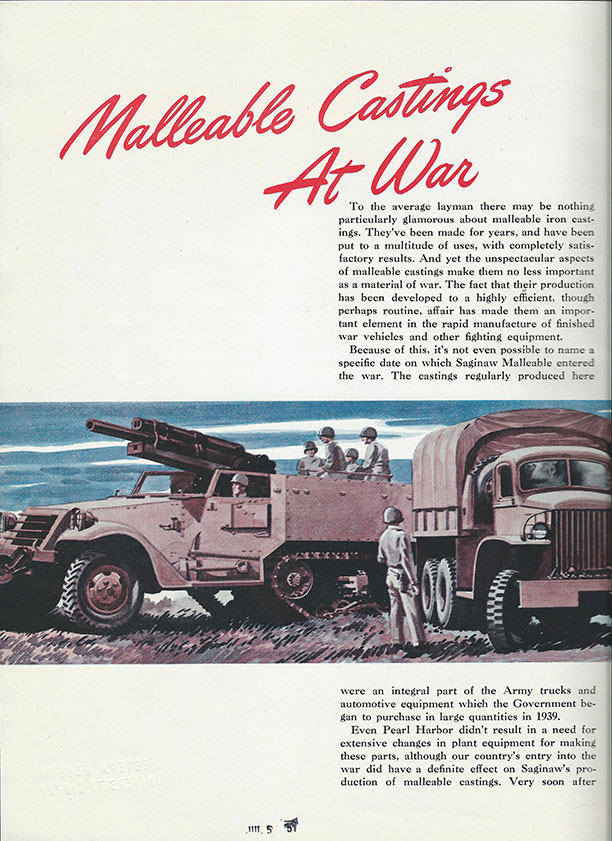
Page 2. Pictured here is the GMC 2-1/2 ton 6x6 cargo which SMI
produced many casting for this truck which was the backbone of US Army
ground transport during WWII. Also pictured is an M3 halftrack
tank destroyer of the type mentioned on page 4.
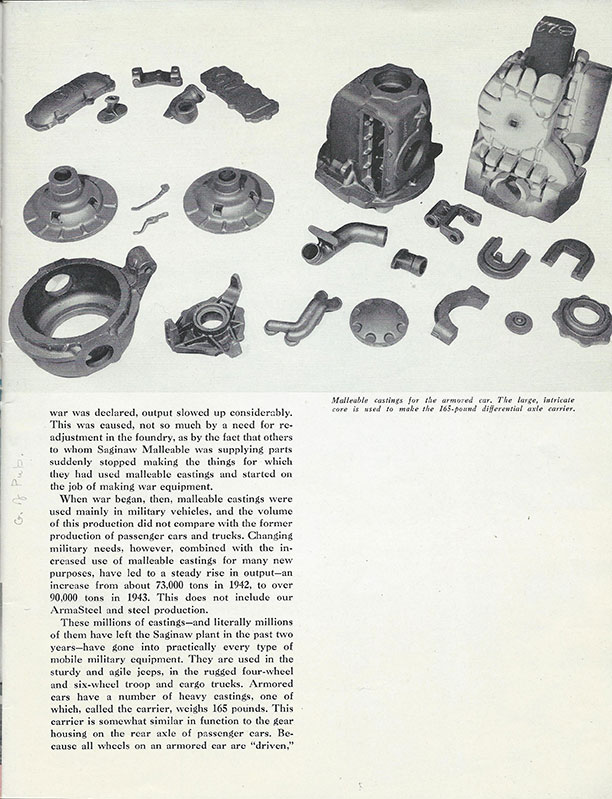
Page 3.
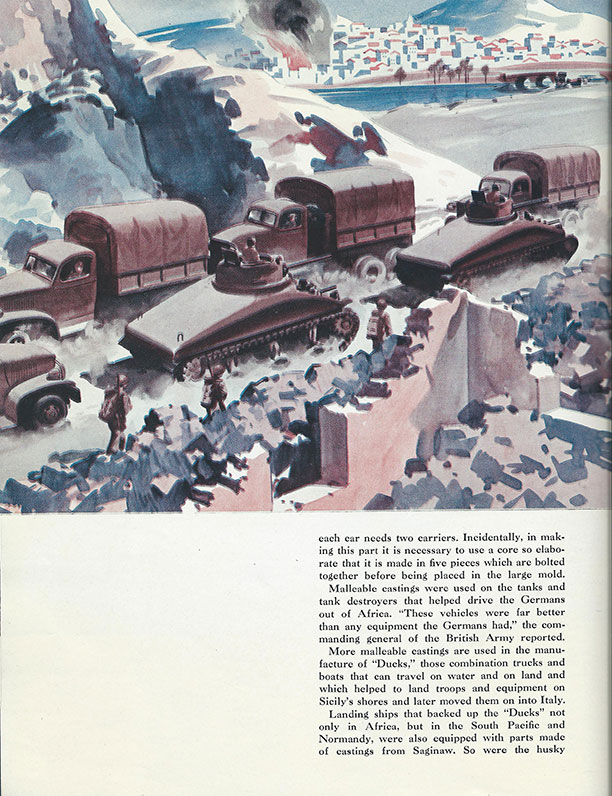
Page 4.
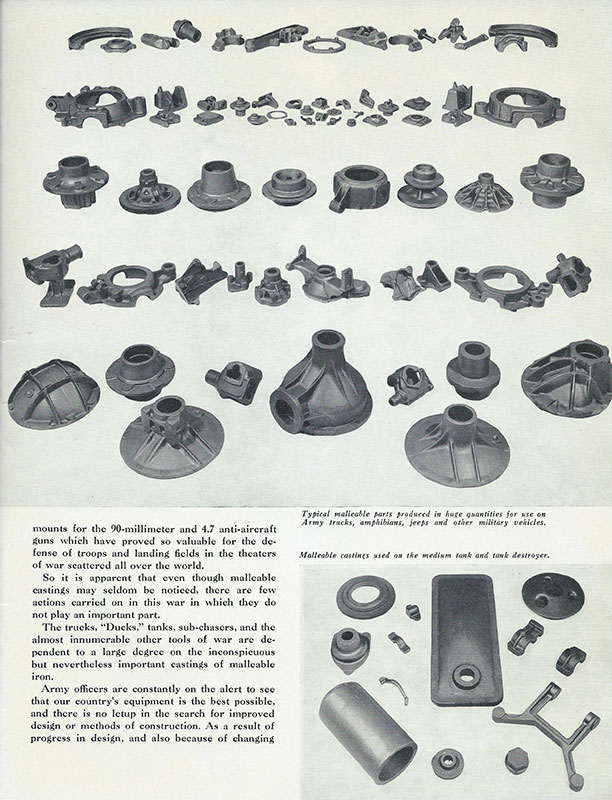
Page 5. Noted on this page is that SMI provided castings for sub
chasers, which would not be expected in the same sentence with parts
made for military ground vehicles. General Motors had three
Divisions building diesel engines for military applications, one of
which, Electromotive Division supplied the engines for (243) 110 foot
sub chasers.
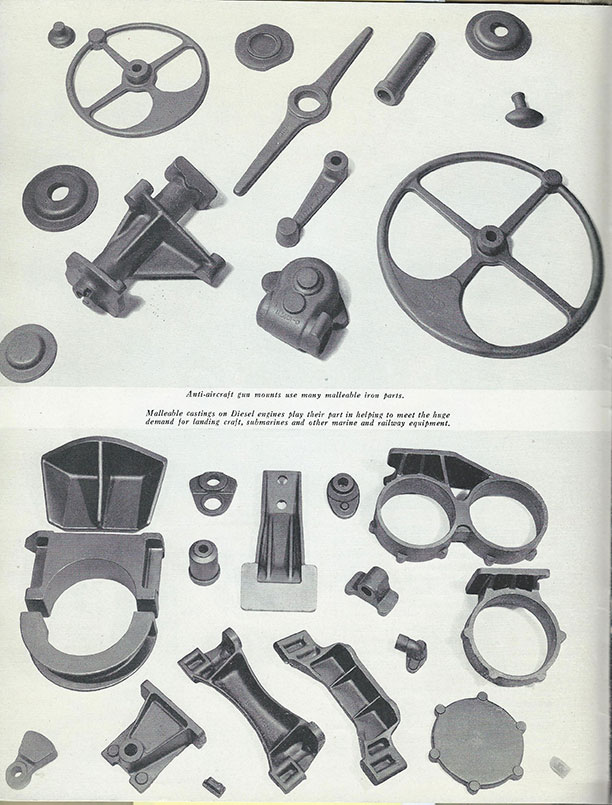
Page 6.
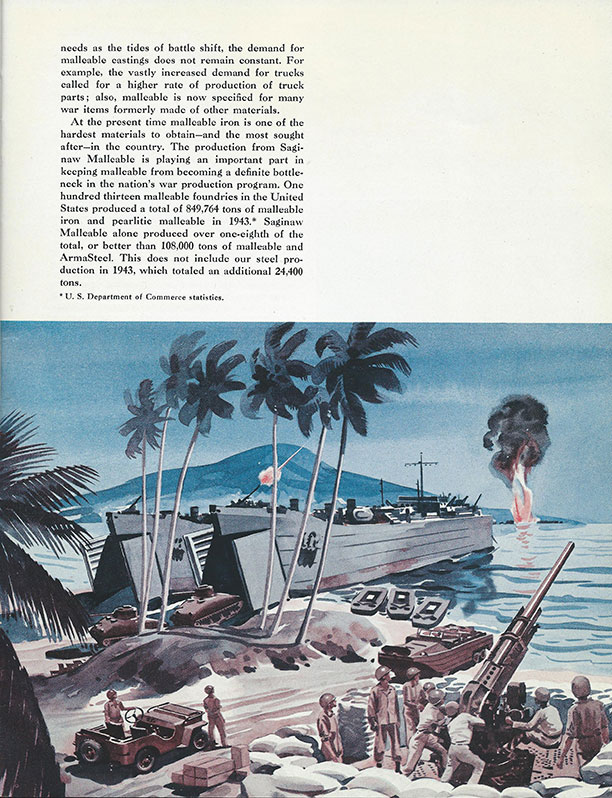
Page 7. Show in this water color rendering of a Pacific beach land
is a Landing Ship Tank (LST), M4 Sherman tanks, a Jeep, a DUKW (Duck),
which was a GMC 2-1/2 ton 6x6 amphibious truck, and a 90mm anti-aircraft
gun, all of which used Saginaw Malleable Iron castings.
Electro-Motive Division supplied half of the diesel engines for the LSTs
which utilized SMI ArmaSteel cast pistons. Steel cast tank tracks
supplied by the Division were used on the M4 Sherman tank.
(642,295) Jeeps were produced by the combined effort of Ford Motor
Company and Willys-Overland during WWII utilizing components cast in
Saginaw by SMI and as noted on pages 4-5, and shown on page 6 gun mount
castings were produced for the 90mm anti-aircraft gun.
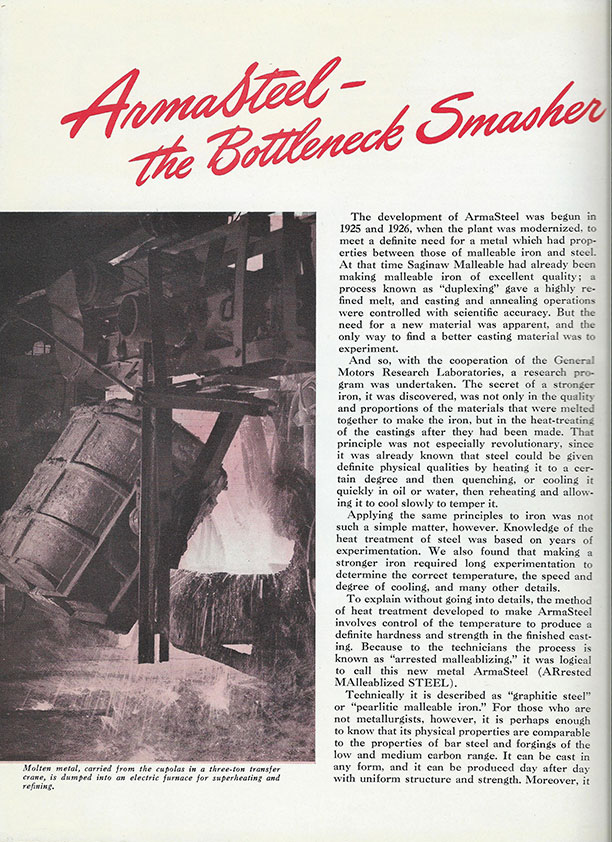
Page 8.
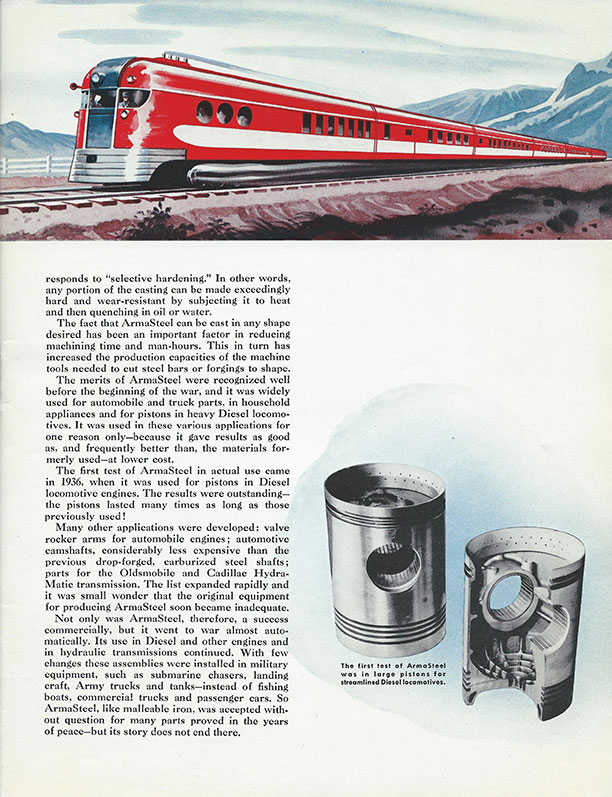
Page 9.
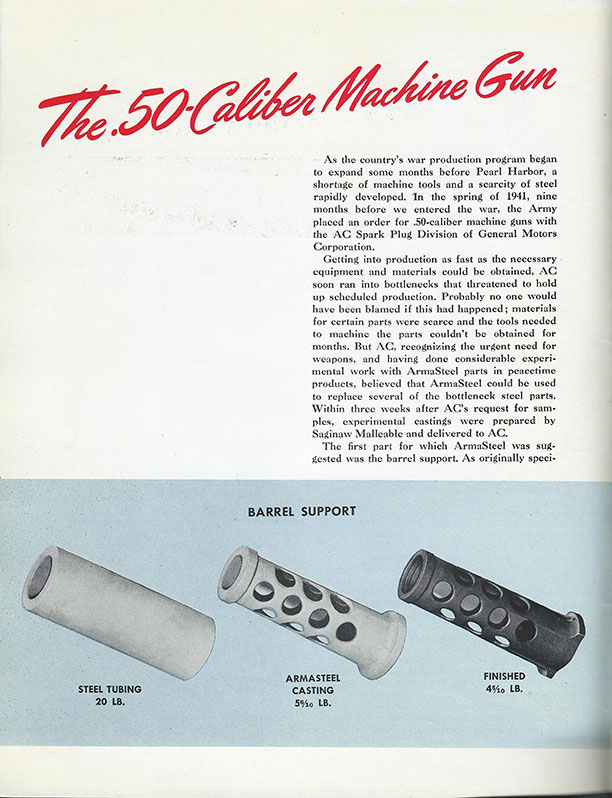
Page 10. While AC Sparkplug is mentioned specifically mentioned in
building .50 machine guns, it was one of three GM Divisions that built
the weapon during the war. Frigidaire and Brown-Lipe-Chapin
Divisions shared in this technology, as well as other companies outside
the Corporation building the weapon. More can be learned of
this endeavor by going to the General Motors page above and reading "One
Million Browning Machine Guns".
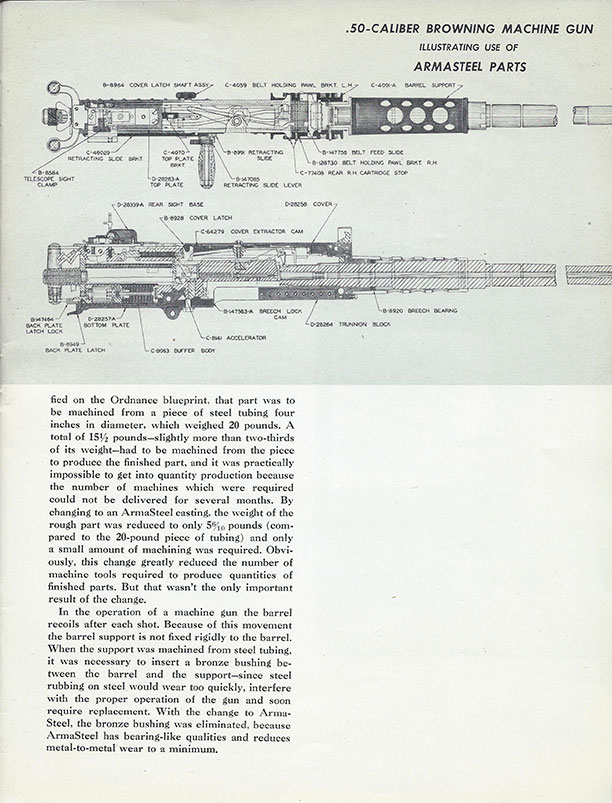
Page 11.
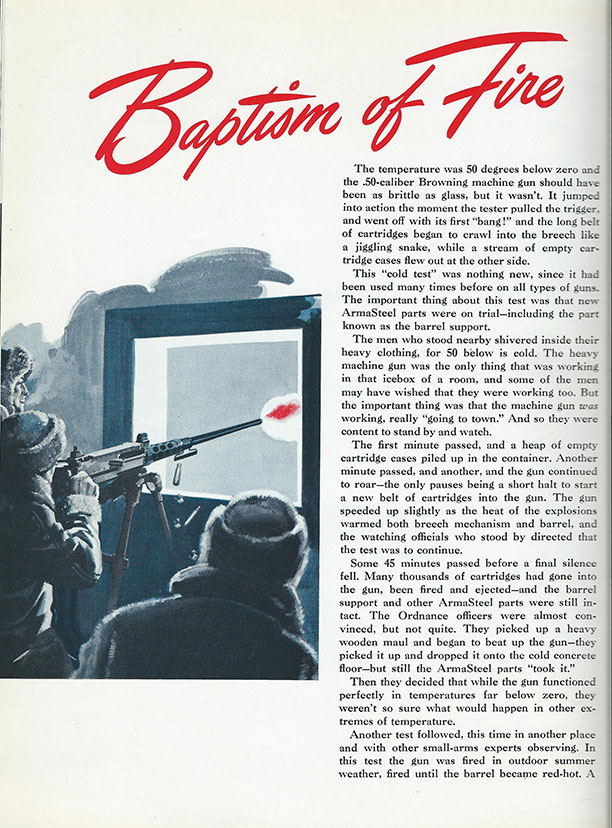
Page 12.
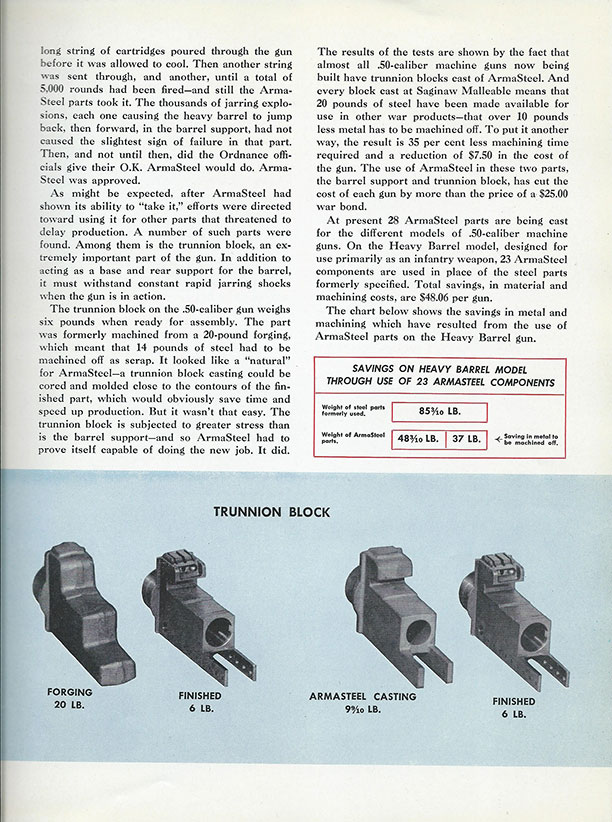
Page 13. Using what is known as "near net shape" castings on the
Browning .50 caliber machine gun Saginaw Malleable Iron was able to save
37 pounds of steel that would have ended up on the shop floor as metal
shavings in the machining process.
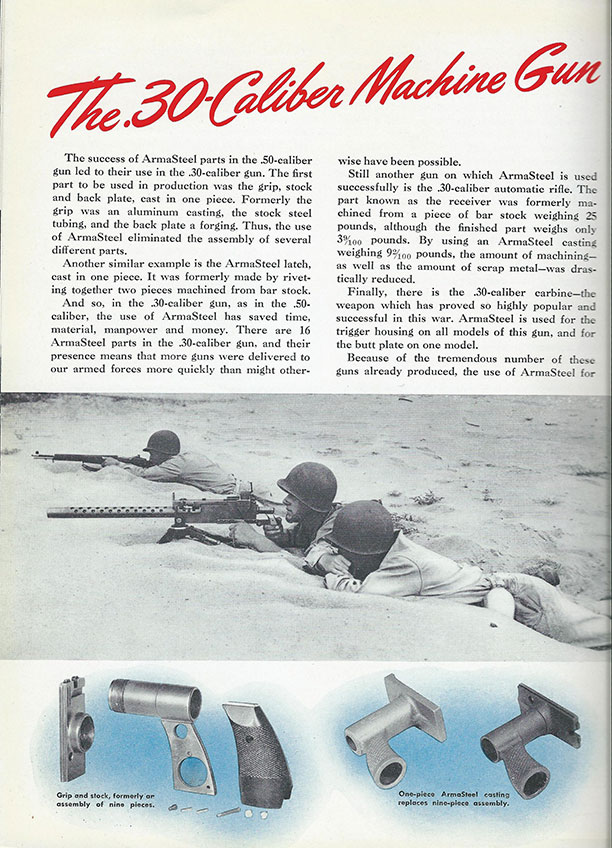
Page 14. Three machined or stamped parts replaced by one casting.
In researching the US Auto Industry during WWII, this type of process
was done by all of the industry and led to numerous costs savings and
reduced material usage of critical materials during the war. The
persons that designed the weapons did not consider during design the
most efficient manufacturing methods. But the US auto industry did
this before the war on a daily basis to make cars and trucks cost
effective for consumers to purchase, so the practice was natural for
them when it came to war production. It sill does it today.
Brown-Lipe-Chapin also built the the .30 caliber machine gun at
the beginning of WWII and then converted to the .50 caliber weapon.
Saginaw Steering Gear built .30 caliber machine guns throughout the war.
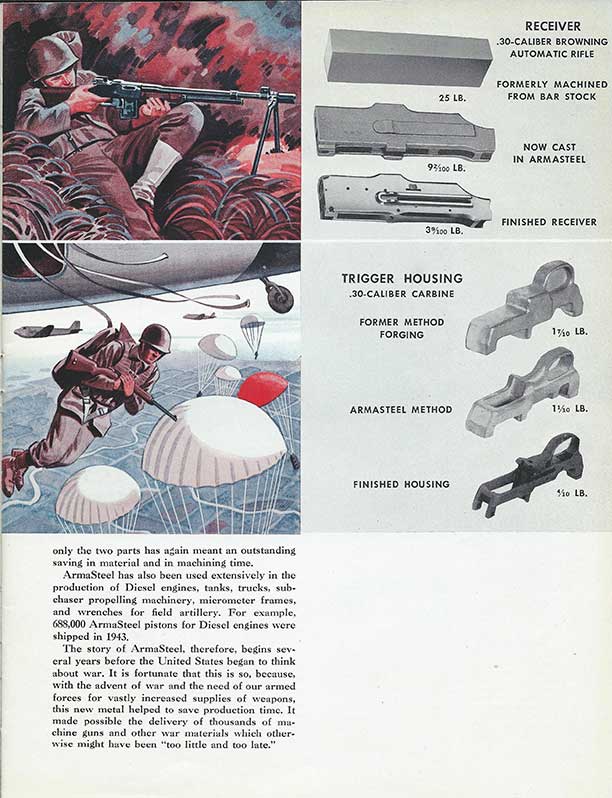
Page 15. Both the Inland and Saginaw, along with other companies
made the M1 carbine in WWII. Armasteel castings would have been
used in the over 3million carbines they produced.
During the Second World War the US Auto
Industry built all sorts of guns; carbines, submachine guns, machine
guns, anti-aircraft guns and cannon. But Saginaw Malleable Iron's
reference to making net shape Armasteel castings for the Browning
Automatic Rifle (BAR) is unique within the industry. Saginaw
Malleable Iron was the
only auto company to make parts for this important weapon which brought
automatic weapons fire down to the squad level.
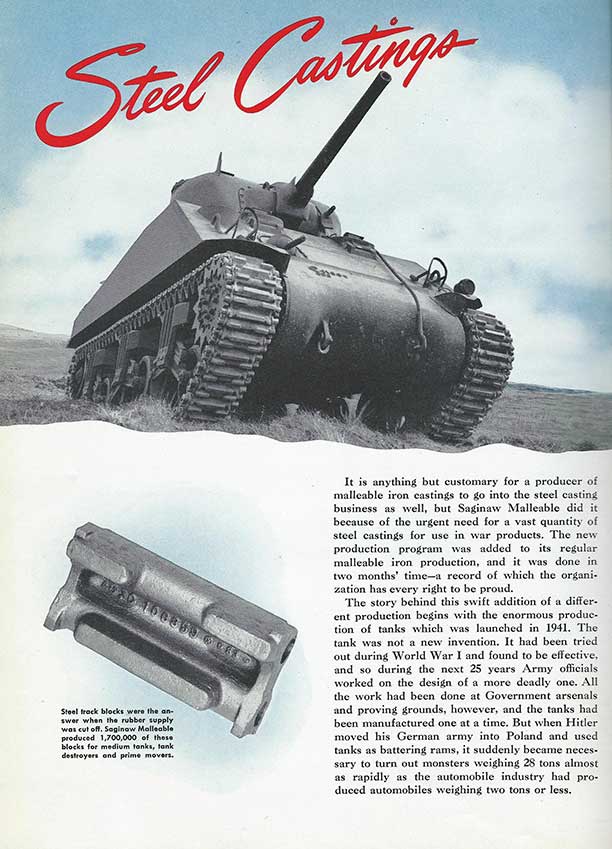
Page 16.
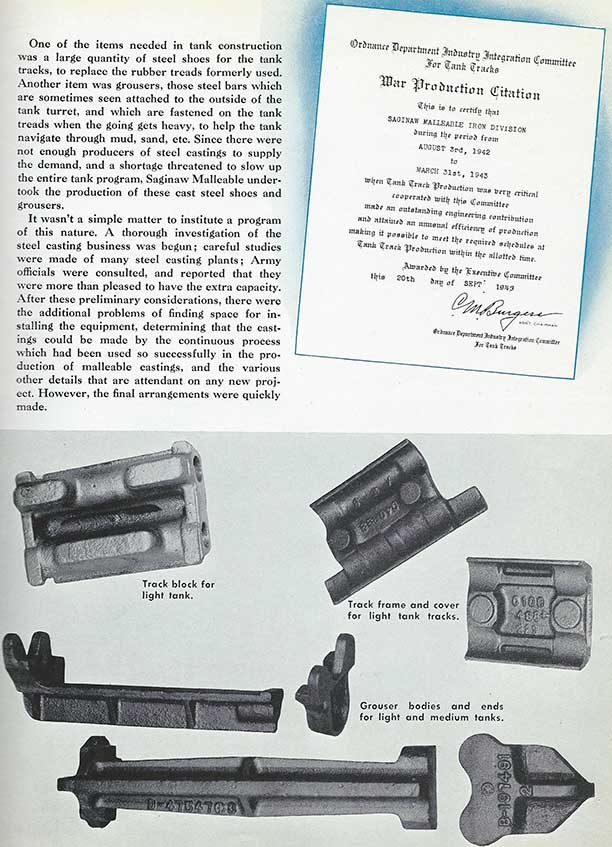
Page 17.
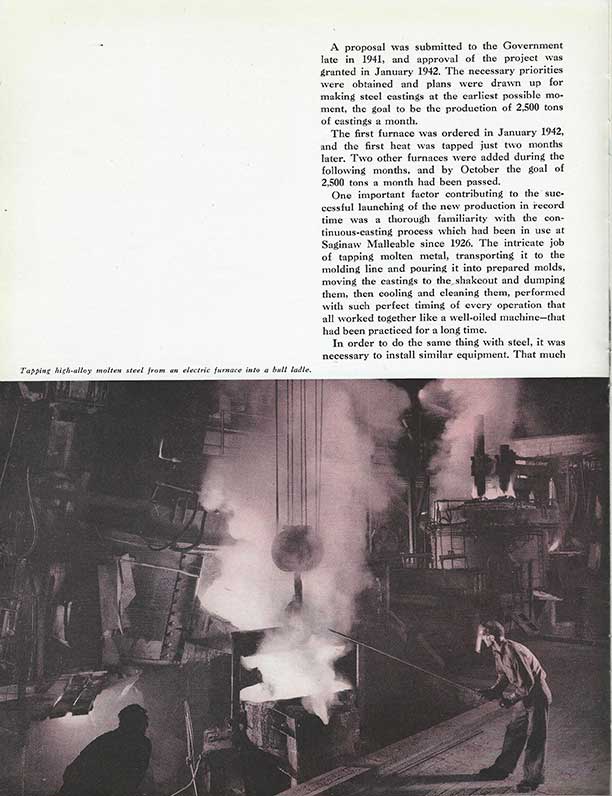
Page 18.
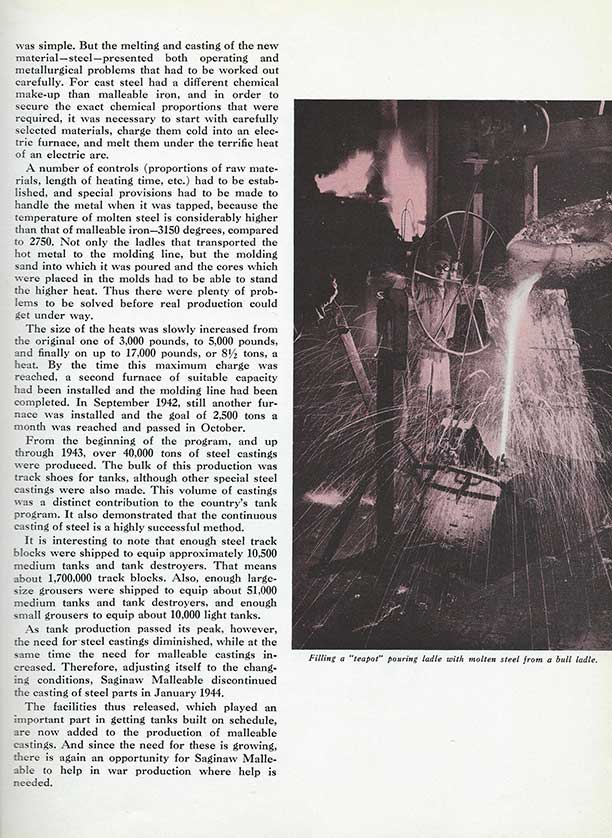
Page 19. The 1.7 million track blocks produced from steel castings
were enough to outfit 20% of the 49,234 M4 Shermans produced during
WWII. Production my have stopped at SMI as its sister Inland
Division had made 4 million track blocks (Inland called them shoes.)
during the same time period
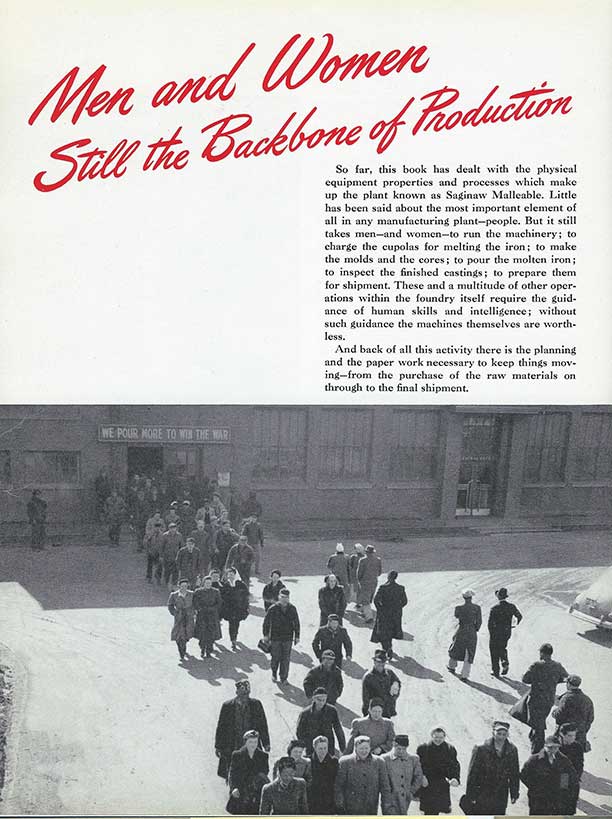
Page 20.
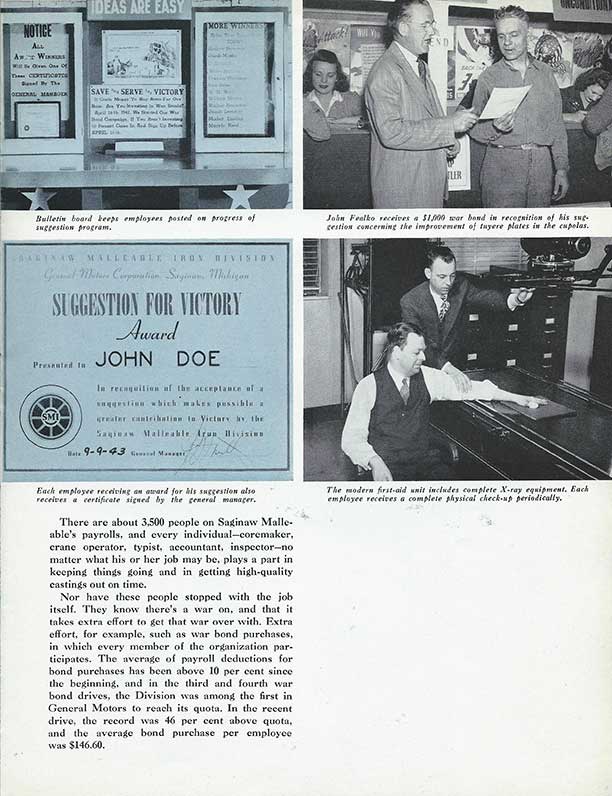
Page 21.
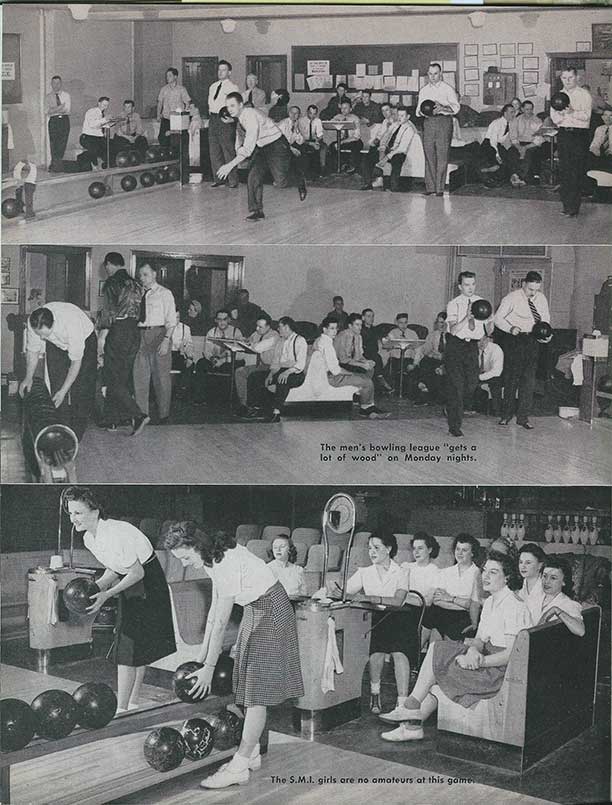
Page 22.
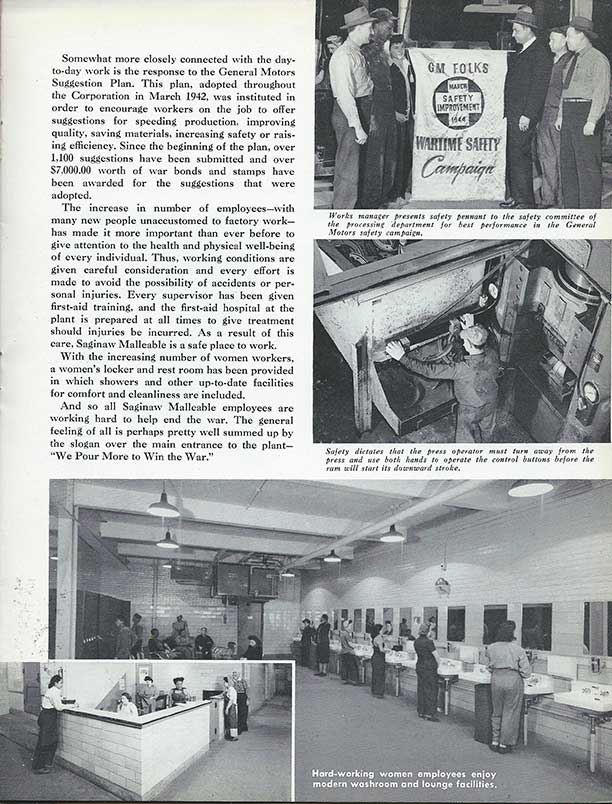
Page 23.
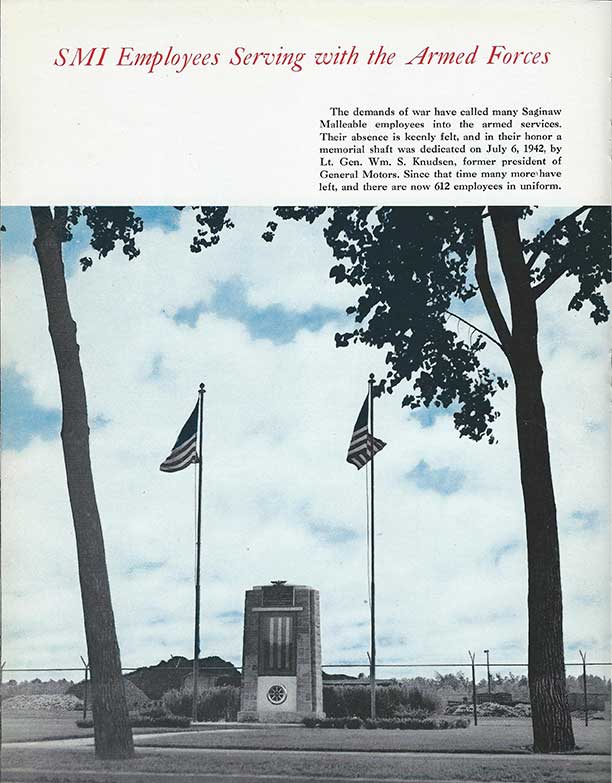
Page 24.
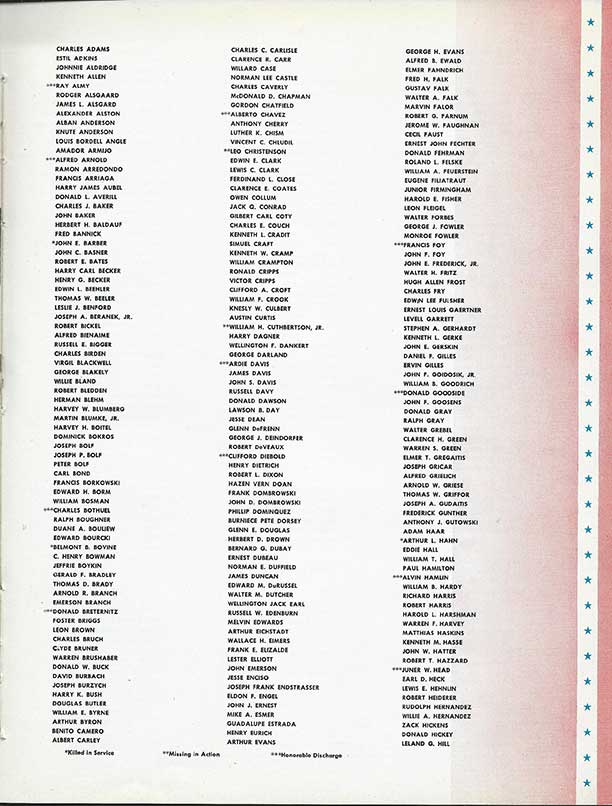
Page 25.
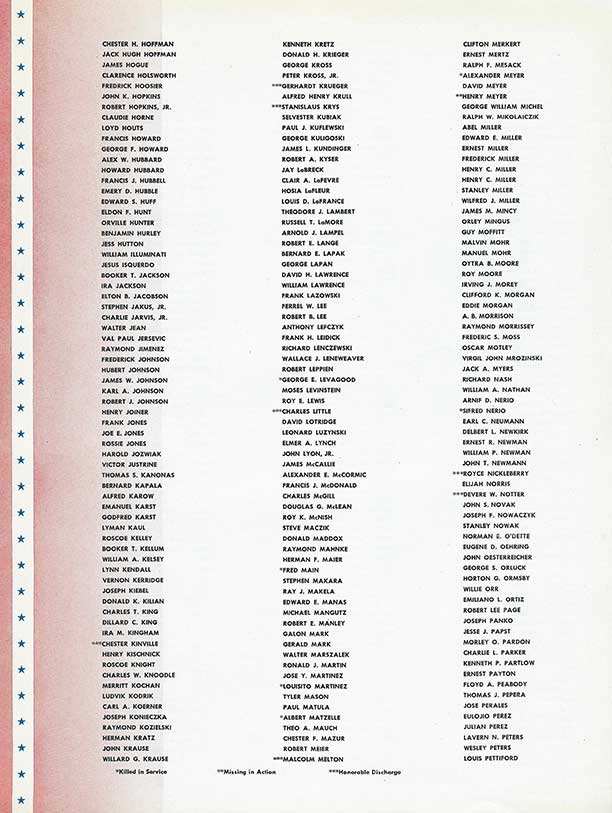
Page 26.
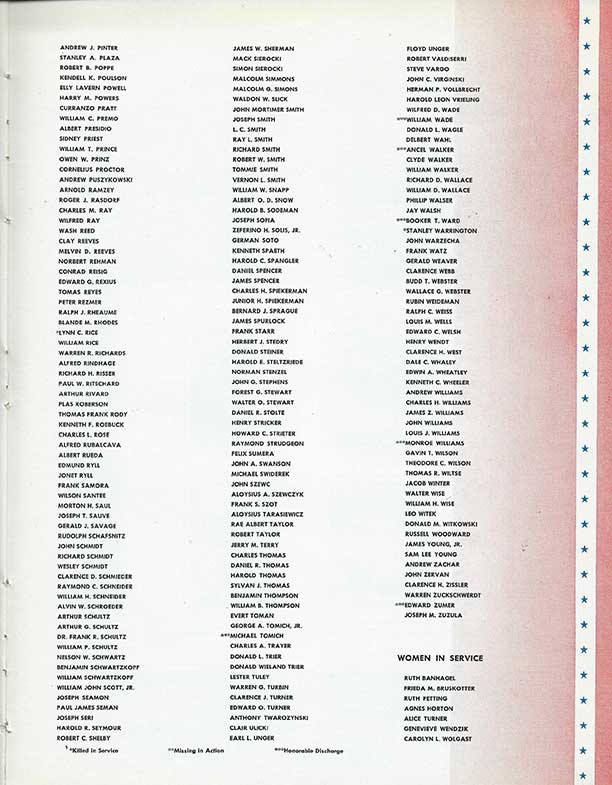
Page 27.
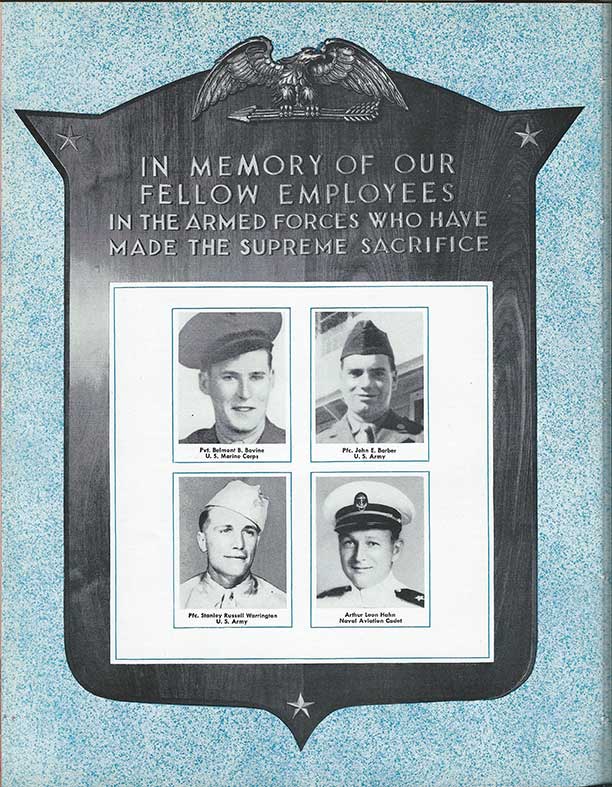
Page 28.
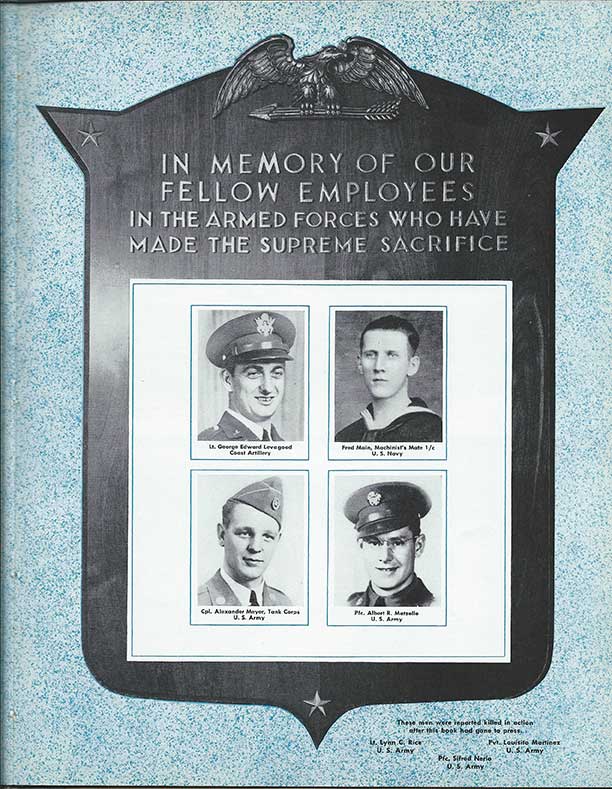
Page 29.
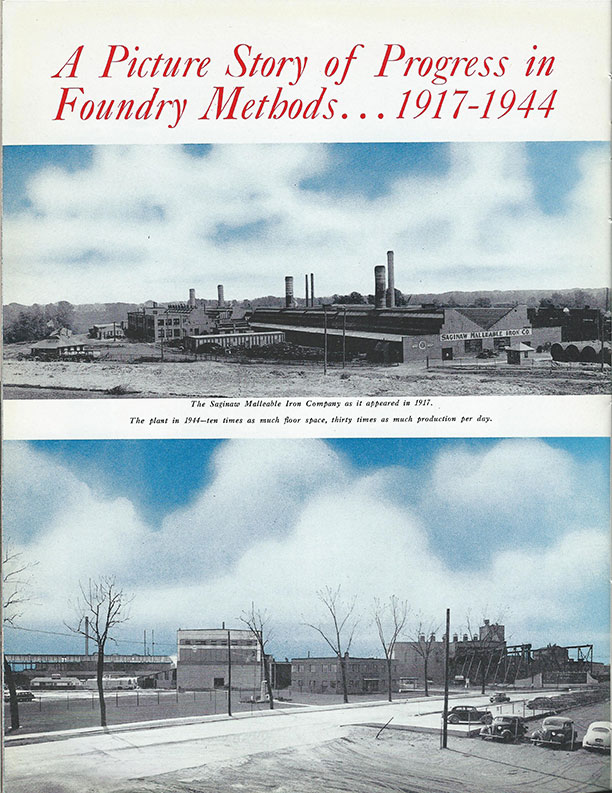
Page 30.
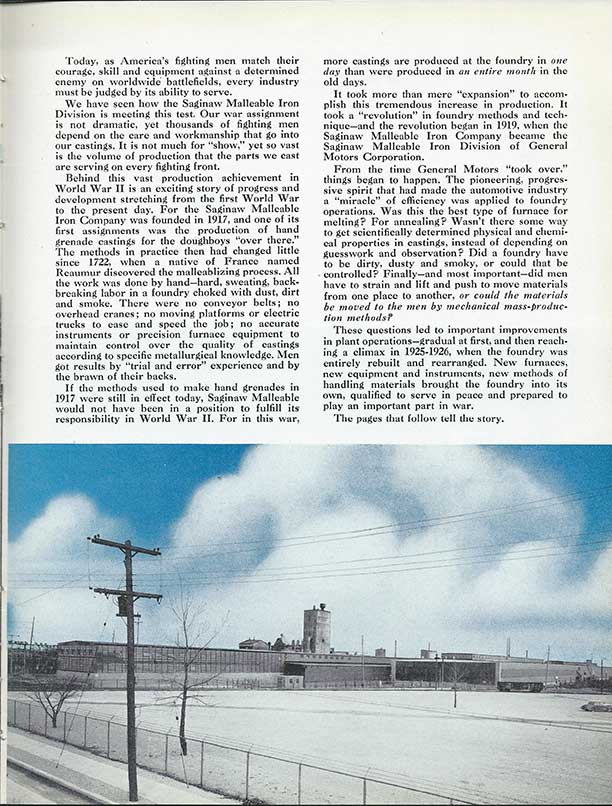
Page 31.
The next twelve pages are unique among the
WWII booklets produced by GM Divisions during that conflict in that
Saginaw Malleable Iron compares the casting technologies it used in WWI
to that of WWII. The following pages are well worth the time
reading.
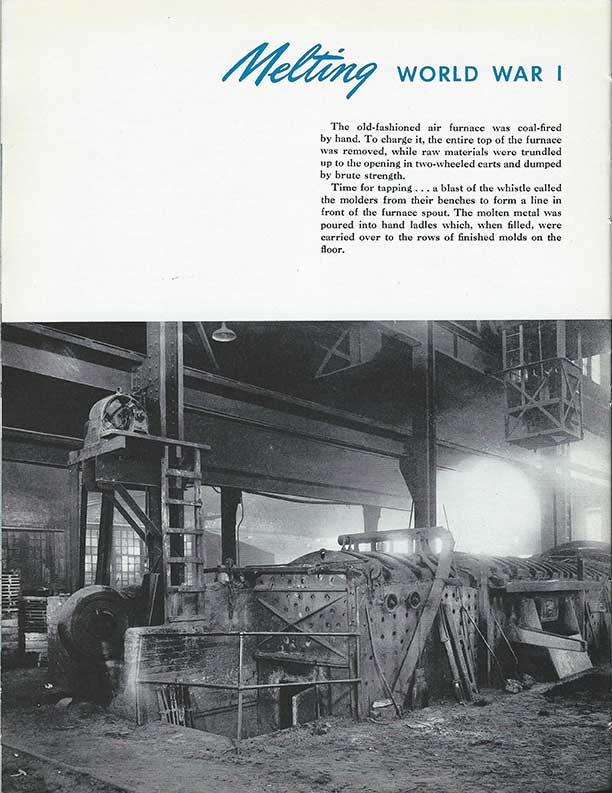
Page 32.
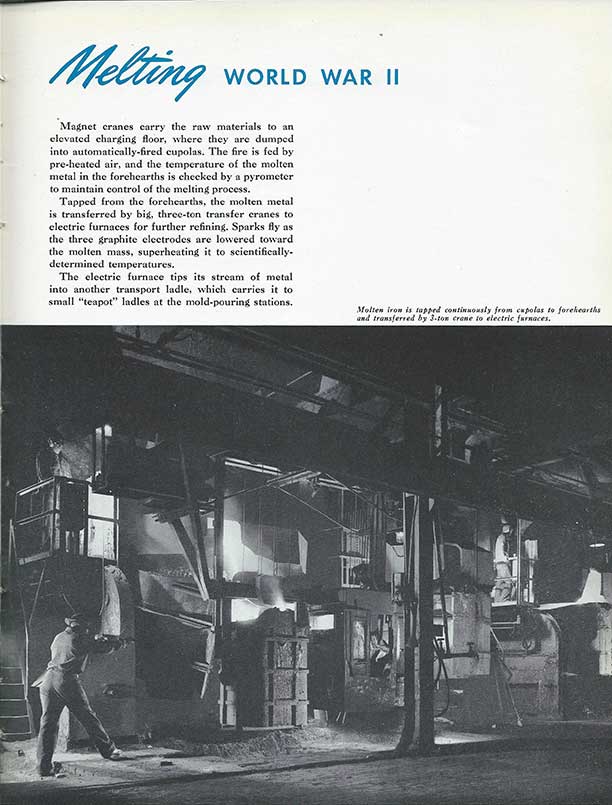
Page 33.
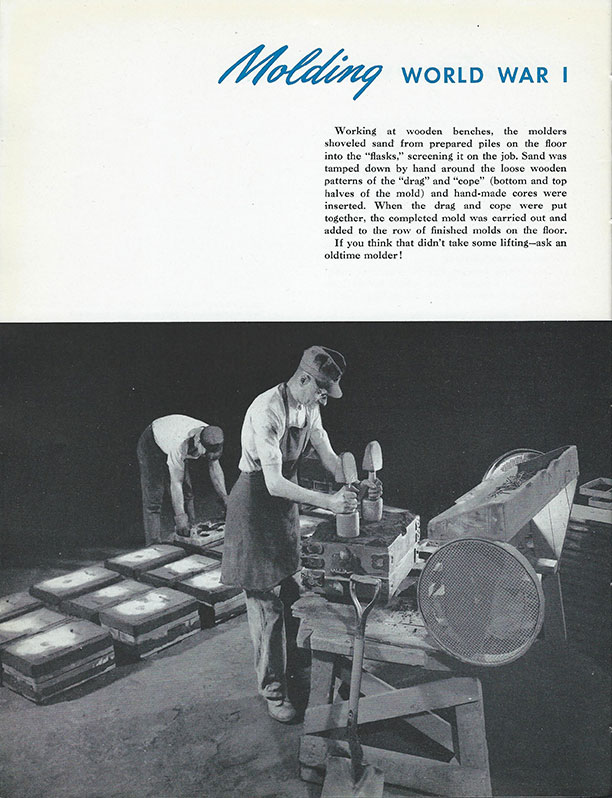
Page 34.
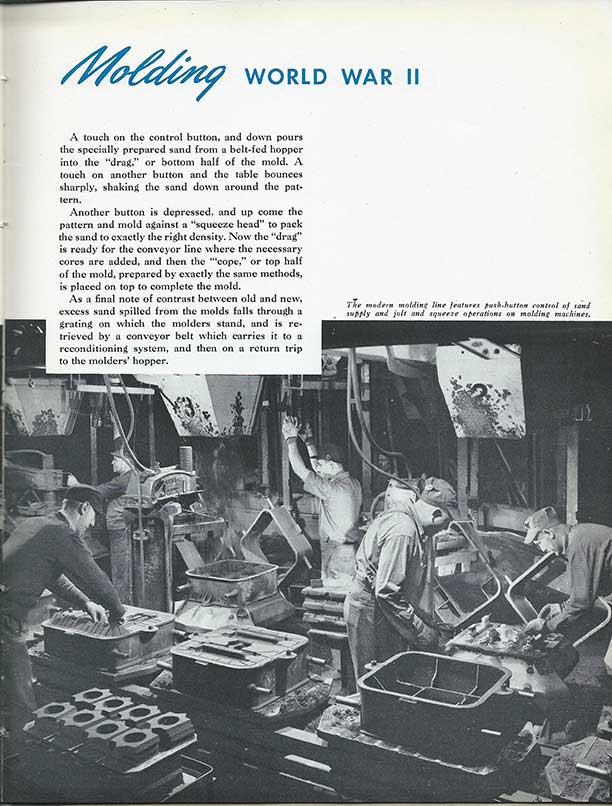
Page 35.
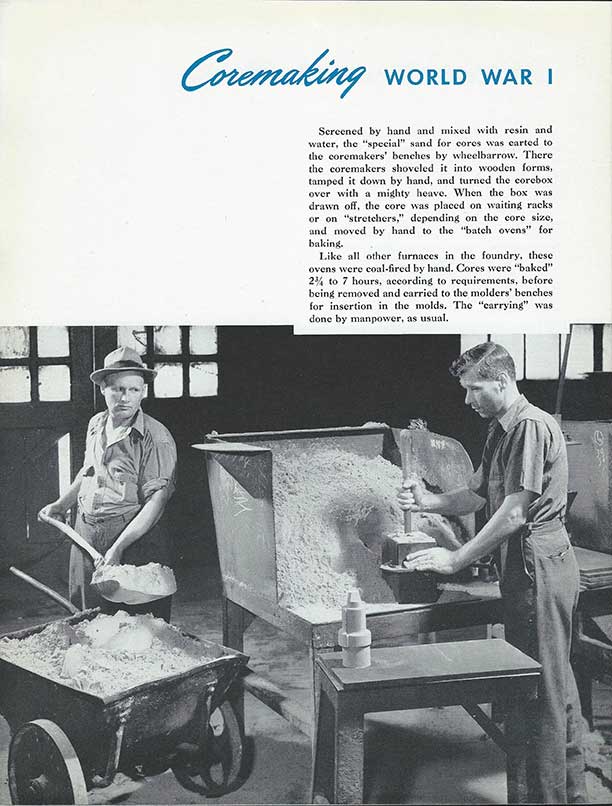
Page 36.
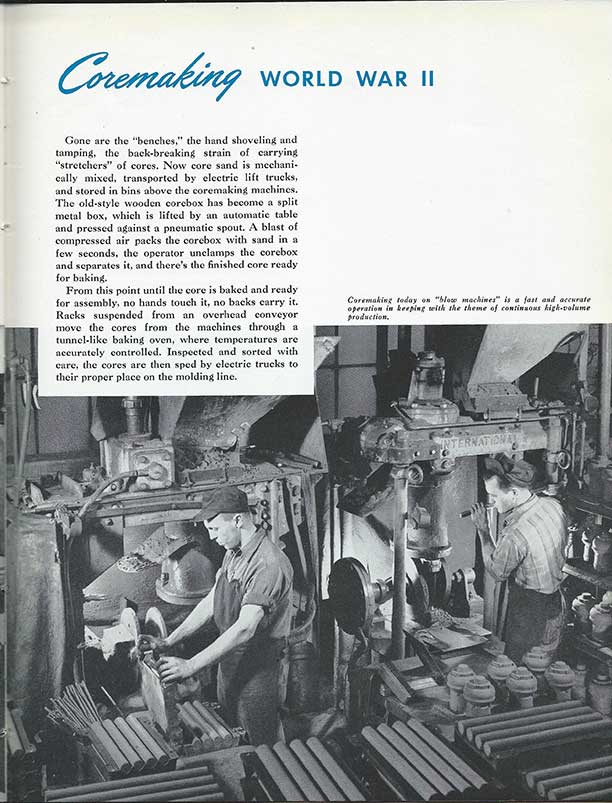
Page 37.
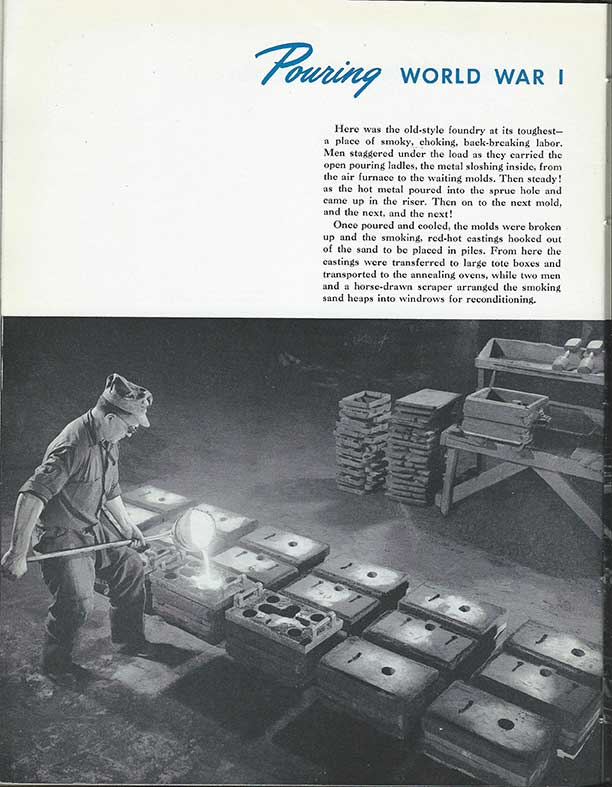
Page 38.
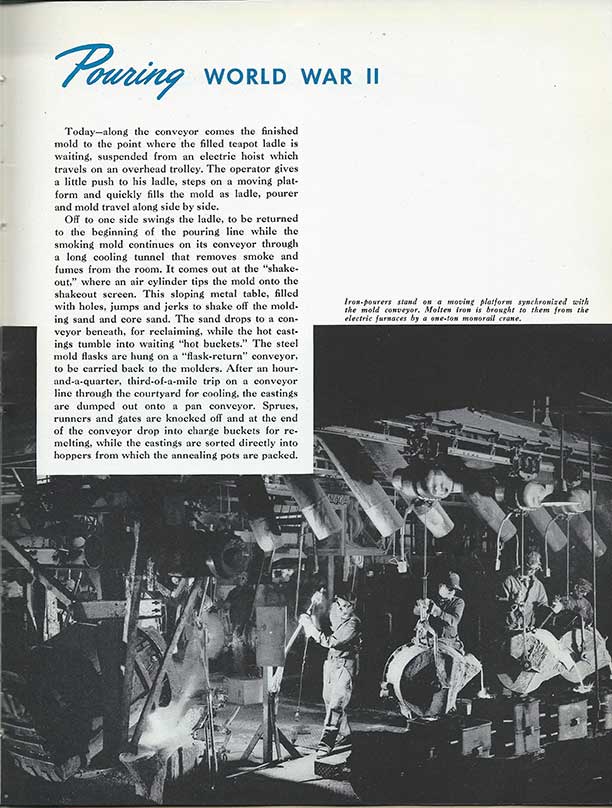
Page 39.
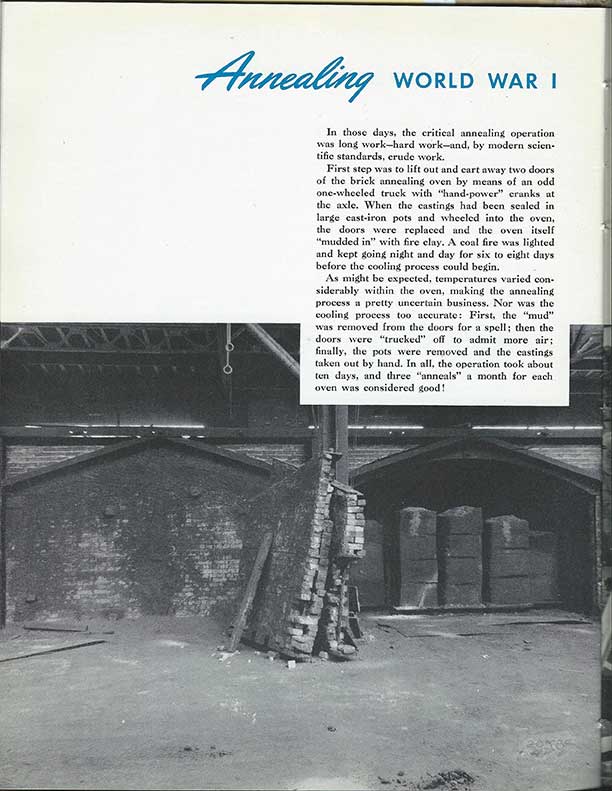
Page 40.
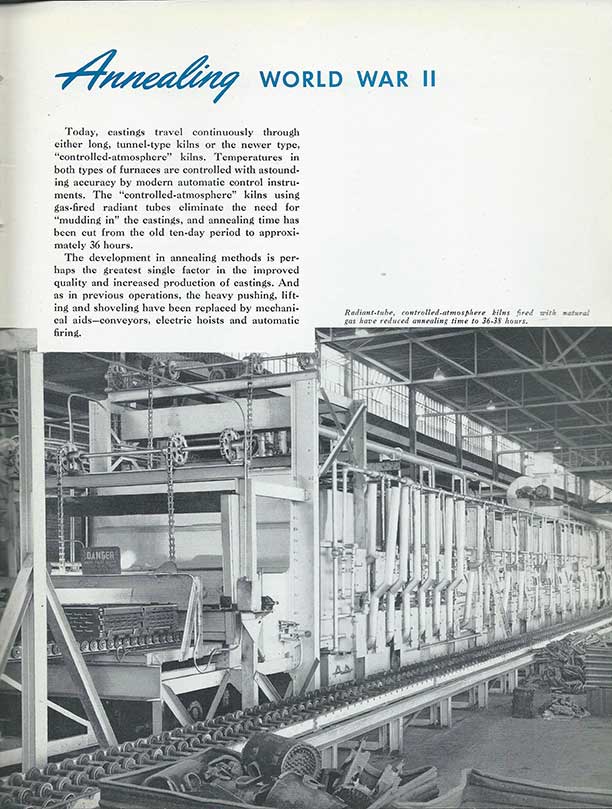
Page 41.
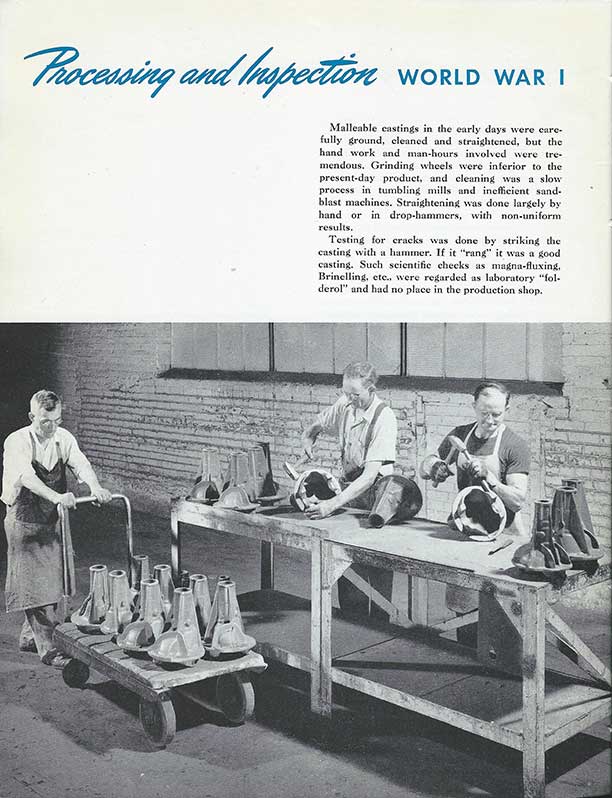
Page 42.
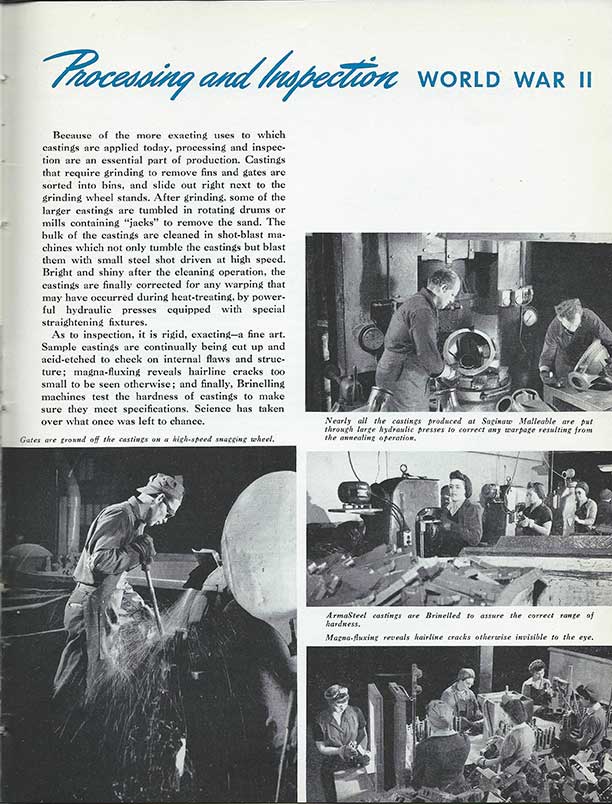
Page 43.
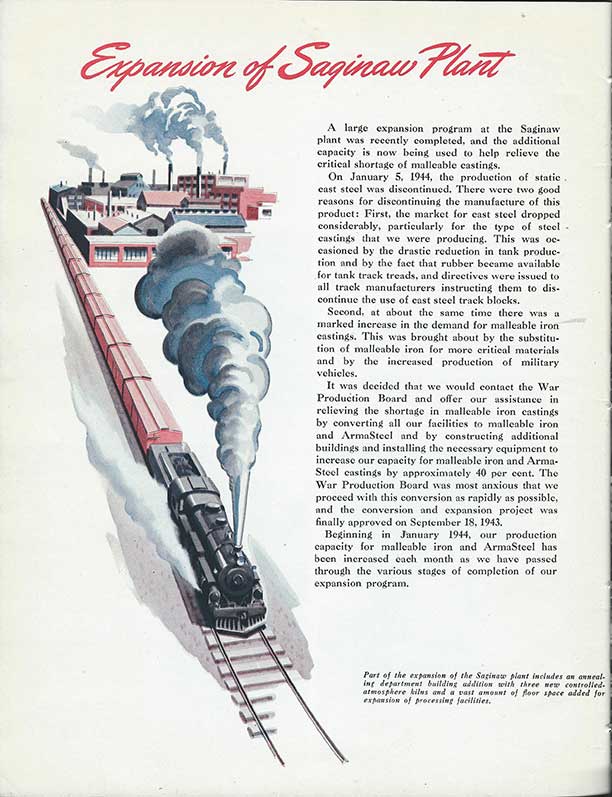
Page 44.
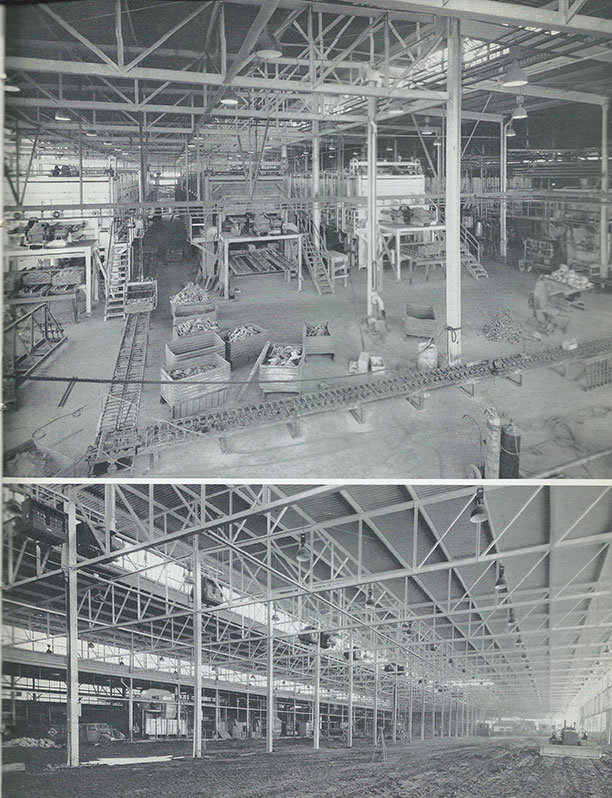
Page 45.
The Saginaw Malleable Iron Division Plant in
Danville, IL. This plant was owned by the US Government and
managed by SMI for the production of truck axle castings. With the
end of the conflict SMI vacated the facility and it was put up for sale
by the government. With the creation by General Motors in 1946 of
the Central Foundry Division, the Danville plant was purchased by the
company for the new Division. In 1996 the plant was closed by GM
and parts of it were razed. Today the remnants that still stand
can be seen by travelers on the north side of I-74 just east of
Danville, IL.
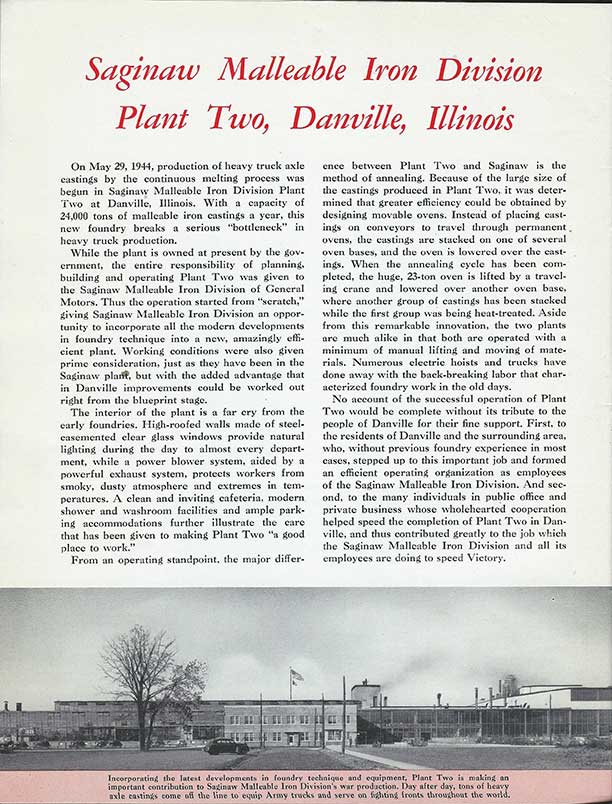
Page 46. The heavy truck castings described here were used in both
the Chevrolet 4x4 1-1/2 ton trucks and the GMC 2-1/2 ton 6x6 trucks
produced during WWII. The castings were shipped to Chevrolet which
not only produced axles for its trucks, but was the main supplier of
axles for the GMC 6x6 truck. GMC did not produce its own axles for
its trucks during WWII and relied on Chevrolet and others for the
components.
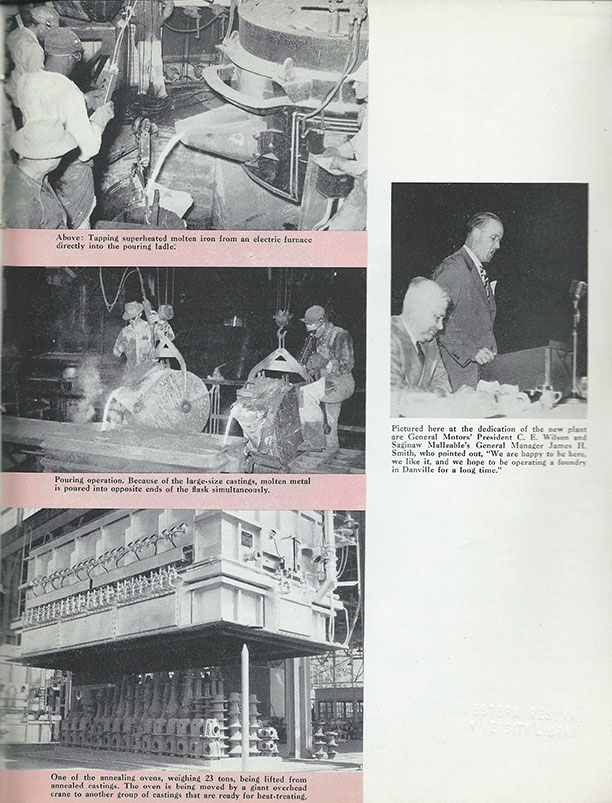
Page 47. The photo directly above is an excellent example of a 25 ton
heat treat oven being lowered down over truck axles and differential
housings.
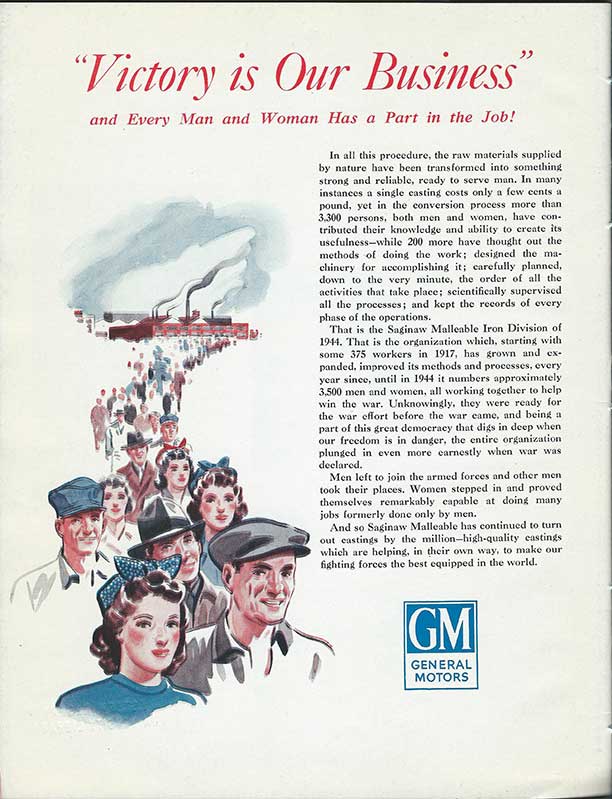
Page 48.
|