Portland
Forge and Foundry in World War Two
Portland, IN
1880's - 1909 as Moffitt and Sees Company, Founders and Machinists
1909 - Current as
Portland Forge and Foundry/Portland Forge
This page added 12-8-2022.
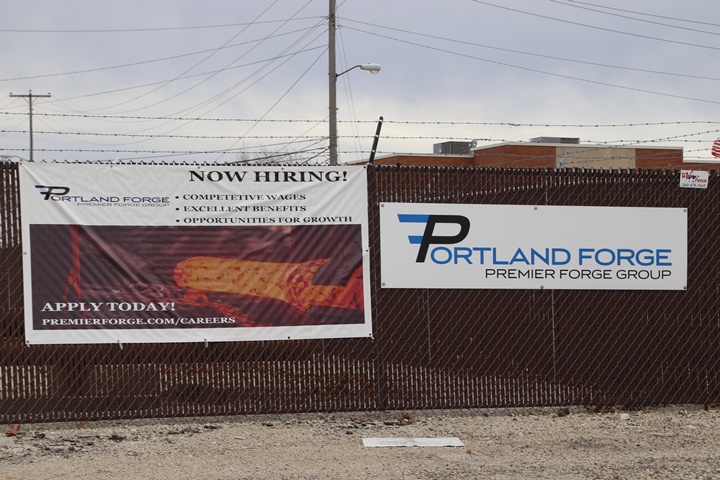
It is extremely rare that a
company that helped win World War Two is still in business in the same
factory it was during the war. But for the Portland
Forge and Foundry of Portland, IN, this is an exceptional case.
Most times when I find a company's factory still standing from World War
Two, the company no longer exists, and the factory has been divided up
and repurposed among several small companies. This is not the case
for the current Portland Forge. While the ownership of the factory
has changed over the years, the company's plant still makes forgings in
Portland, IN. Author's photo.
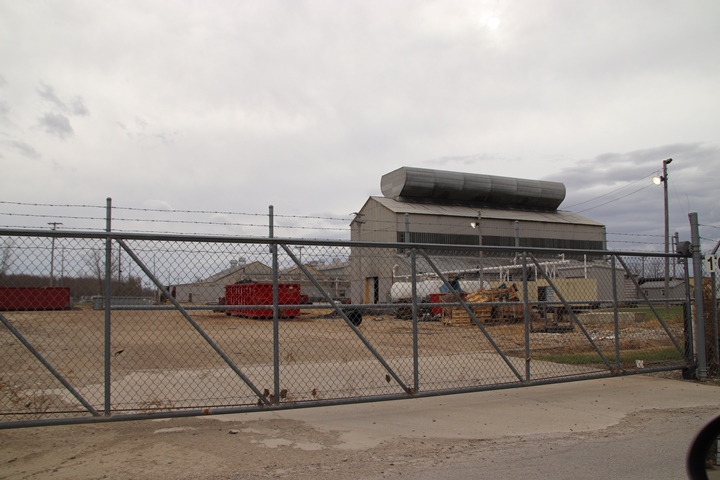
This image is looking south at the northeast
corner of the factory. Author's photo.
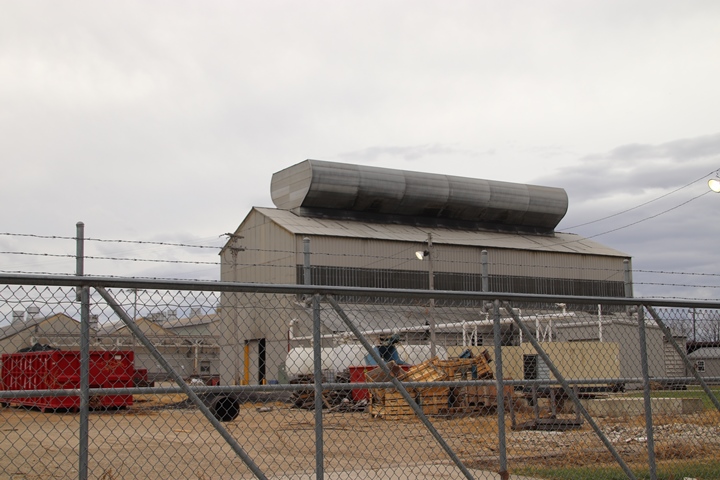
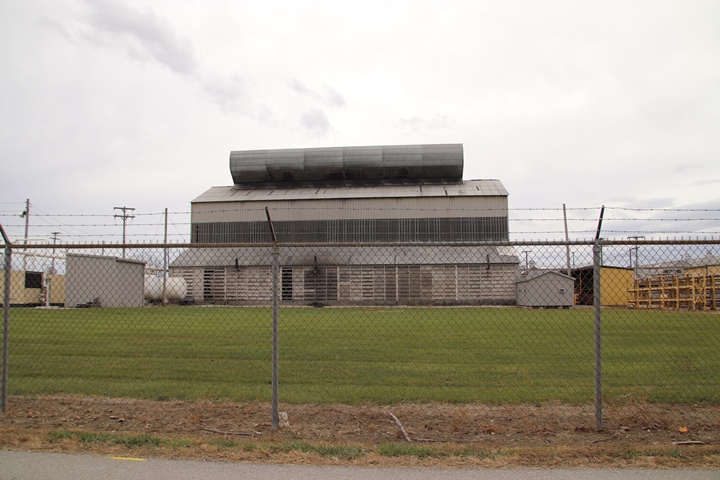
Author's photo.
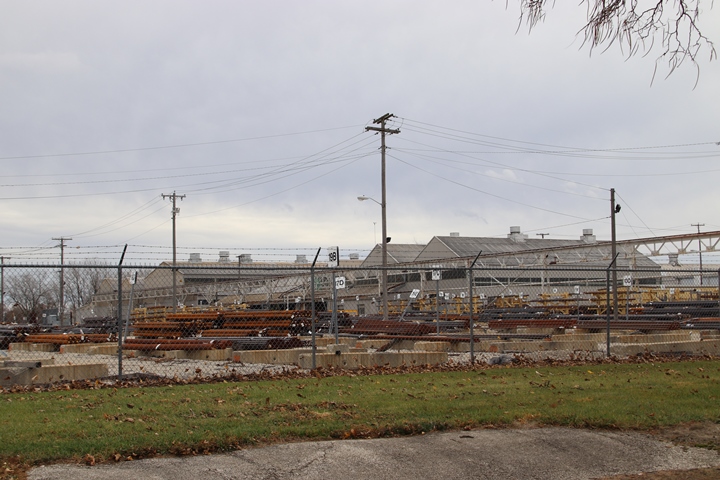
This image is looking southeast from the
northwest corner of the plant. Author's photo.
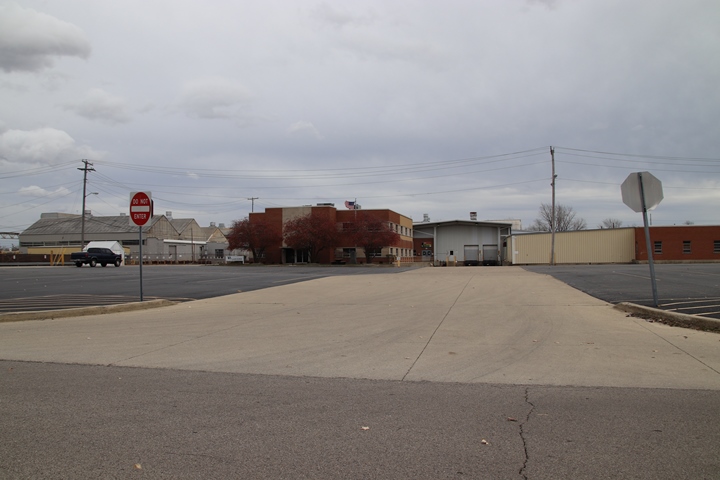
This image is looking directly east into the
parking lot with the factory's office building in the center. The
parking lot looked to have been recently repaved. I was impressed
that the area was free of litter. The employees have done an
excellent job of taking care of the parking lot. Author's photo.
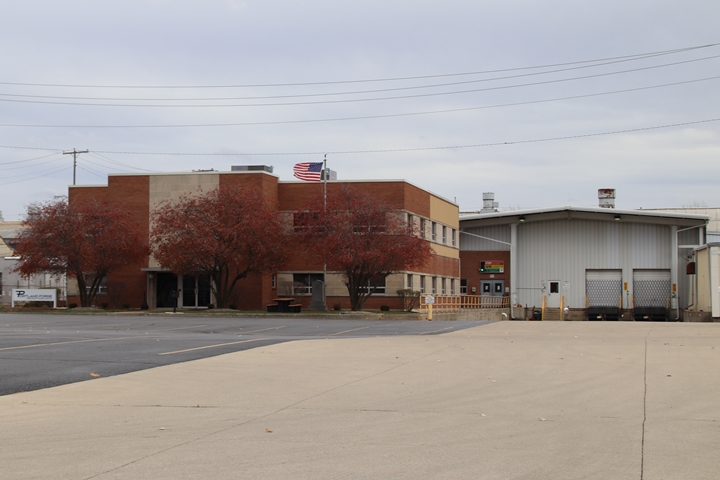
Author's photo.
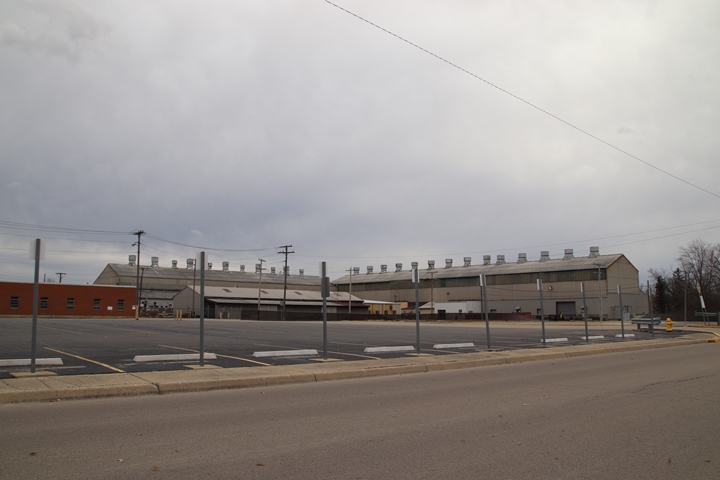
This image is looking at the last building
on the south end of the factory. This photo again shows the
cleanliness of the parking lot and the area around the forges.
Author's photo.
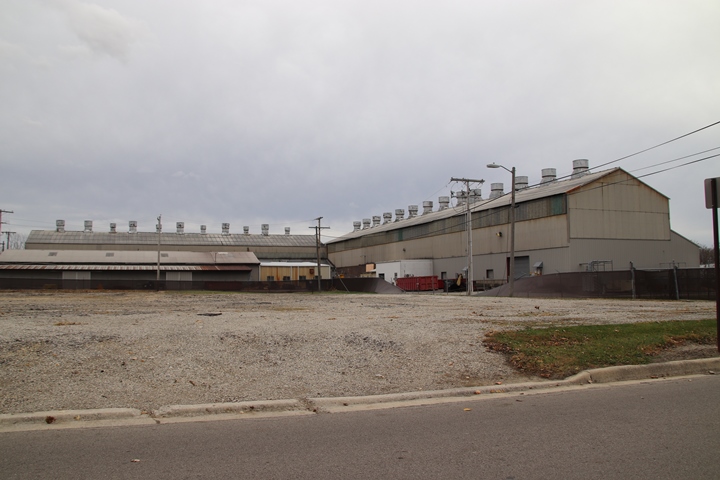
These two forges appeared to be the oldest
buildings of the complex. However, if so, they have been well
maintained during their lifetime. Author's photo.
During World War Two, this forge and foundry
complex employed approximately 350 employees.
History: The history of the
company goes back 120 years to the 1880's when Patrick Moffitt and Henry
Sees started the Moffitt and Sees
Company, Founders and Machinists Company on East North Street in
Portland, IN. The two men operated the company at this location
producing equipment for the gas and oil companies in the area at the
time. In 1909, the two of them sold their business to a
corporation which renamed the business as the Portland Foundry and
Machine Company. It also moved the operation to its current
location on North Wayne Street in Portland. The new owners changed
the direction of the company's future by installing four drop hammers in
the plant. In 1915, this change was reflected in the company's new
name of the Portland Forge & Foundry Company.
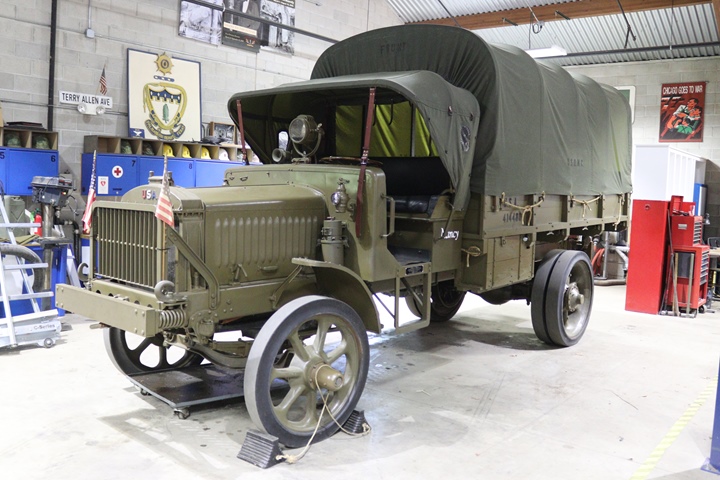
During World War One, the company forged
gears for the Class B Liberty truck. Both Durham Gear and Warner
Gear in nearby Muncie, IN made transmissions for the vehicles.
Most likely the Portland Forge was providing gears for one or both of
the companies. Author's photo.
The Army-Navy "E" Award:
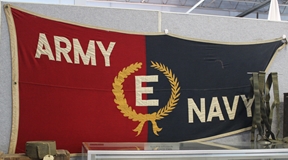
The Portland Forge and Foundry won the
Army-Navy "E" flag four times during World War Two.
The first award was made on February 13, 1943. The second award
was announced on April 6, 1944.
Portland, IN is a small town in east-central
Indiana and is the county seat of Jay County. The current
population of Portland is just over 6,000 persons, with agriculture
being the primary means of earning a living in the area. During
World War Two, the Portland Forge was one of several companies in
Portland. When the Portland Forge won the "E" award, it was a big
deal in town.
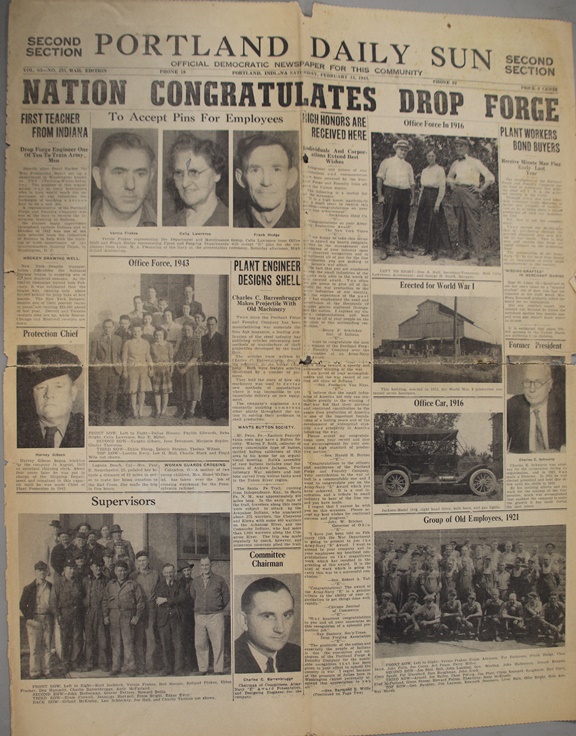
The February 13, 1943, edition of the
Portland Daily Sun featured the Portland Forge on the first page of the
newspaper.
Currently, the town of Portland, IN has a fine
military museum. Named the Museum of the Soldier, the museum not
only has military artifacts, but also information on the local
industries during World War Two. Without the Museum collecting and
saving this valuable information, I would not be able to write this
webpage. The newspaper pages, "E" Award information, and the
Portland Forge and Foundry's "Forgings for War" are all from the
Museum's collection.
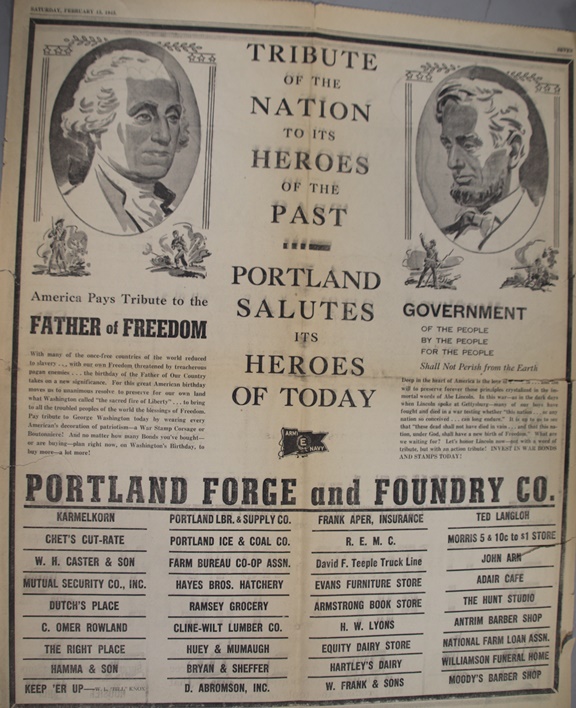
This is one of many pages in the newspaper
with other businesses in Portland congratulating the Portland Forge for
winning the "E" Award.
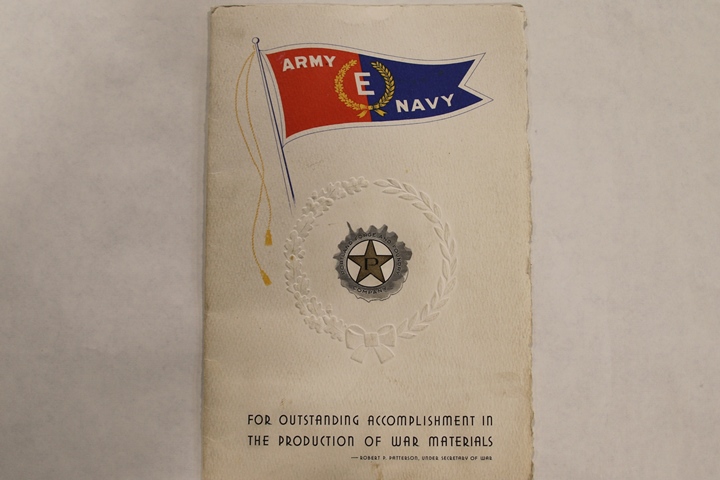
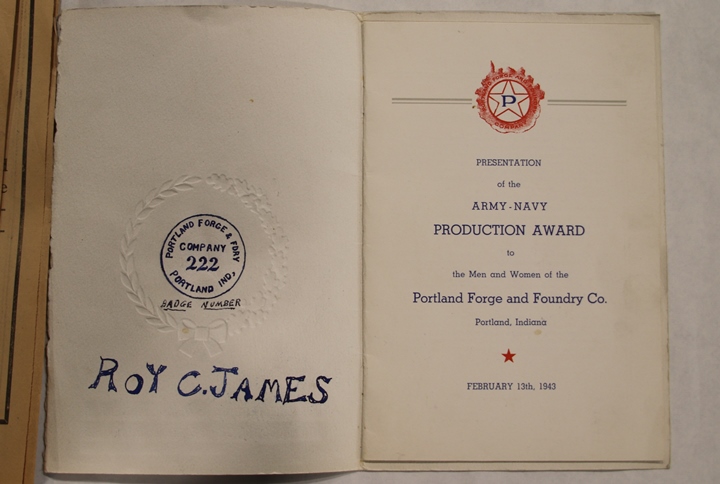
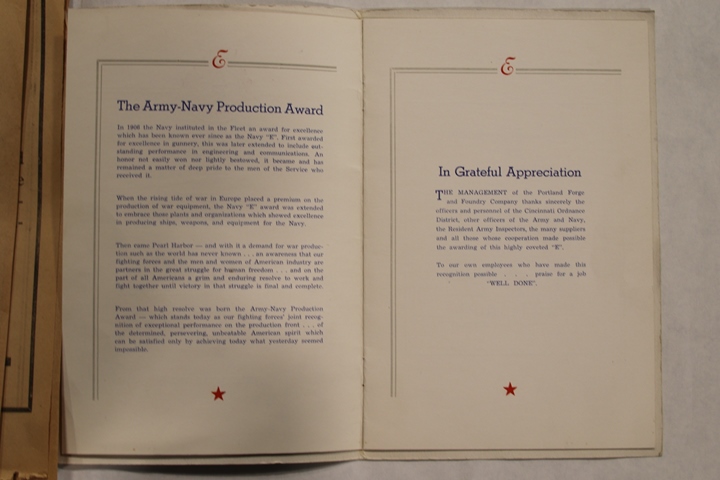
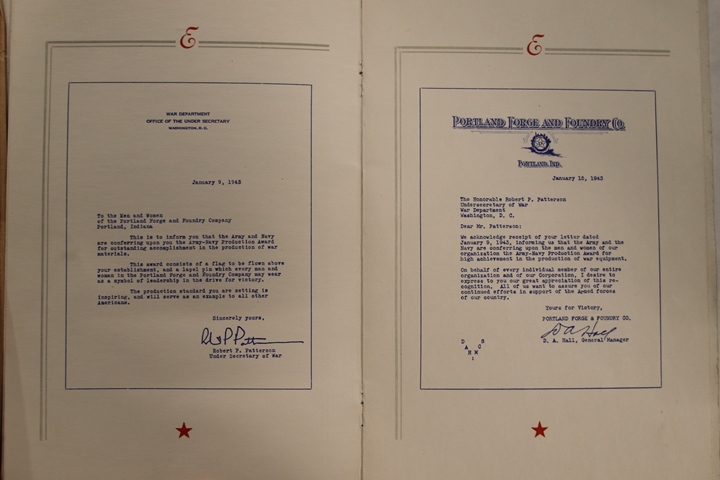

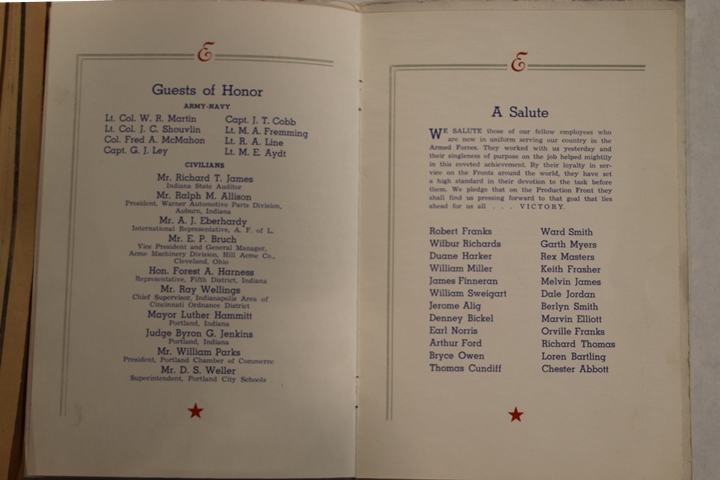
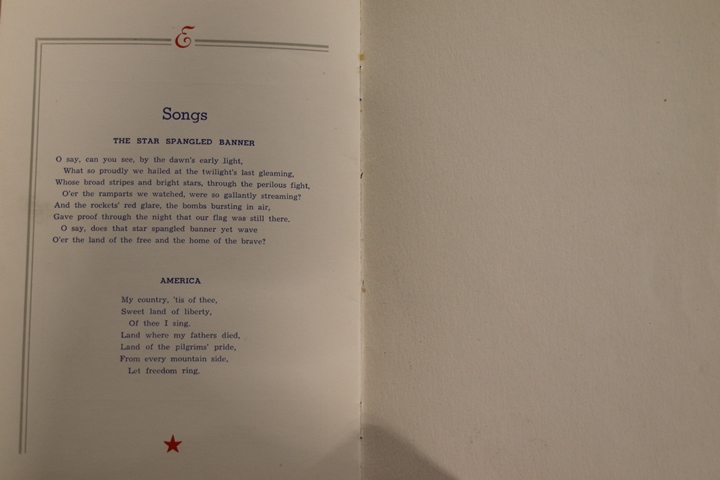
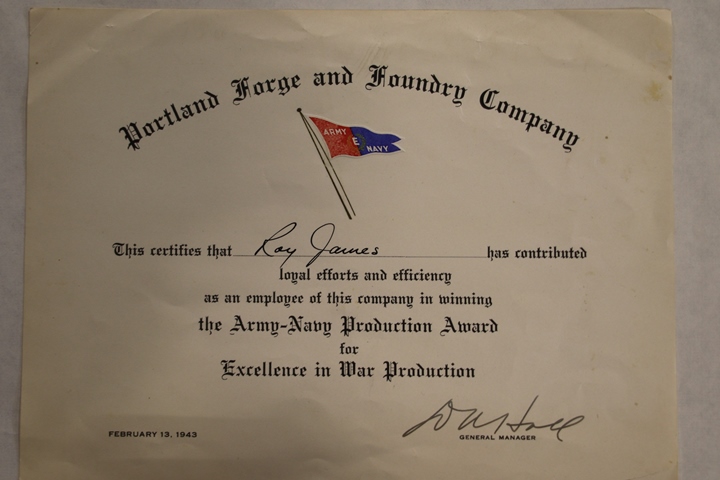
Portland Forge and Foundry World War Two
Products: The two products
most associated with the company during World War Two were 37mm high
explosive shells, 75mm shot and high explosive shells, and 81 mm mortar
high explosive shells. Table 1 shows that the Portland Forge had
$609,000 in contracts from Army Ordnance totaling $609,000 between
October 1940 and November 1942. What is interesting is that there
are no major contracts over $50,000 after November 1942. However,
it is known that the company was producing something for military use after
this date, as the Portland Forge received its first "E" Award in February
1943. It then went on to receive three more renewal awards.
It could be the contracts from Army Ordnance
in 1943, 1944, and 1945 were less than $50,000 per contract. The
company was also making forgings and castings to several companies under
sub-contracts.
Table 1 -
Portland Forge and
Foundry Company's
Major World War Two Contracts
The information below
comes from the "Alphabetical Listing of Major War Supply
Contracts, June 1940 through September 1945." This was
published by the Civilian Production Administration, Industrial
Statistics Division. |
Product - Customer |
Contract Number |
Contract Amount |
Contract Awarded
Date |
Completion
Date |
Shell
Forgings - Army Ordnance |
2940-ORD-706 |
$95,000 |
10-40 |
1-1942 |
Shells - Army
Ordnance |
2940-ORD-00790 |
$127,000 |
8-1941 |
6-1942 |
Shells - Army
Ordnance |
2940-ORD-00035L |
$127,000 |
8-1941 |
3-1942 |
Shells - Army
Ordnance |
2940-ORD-895 |
$88,000 |
1-1942 |
9-1942 |
Shells - Army
Ordnance |
2940-ORD-958 |
$192,000 |
2-1942 |
11-1942 |
Total |
|
$609,000 |
|
|
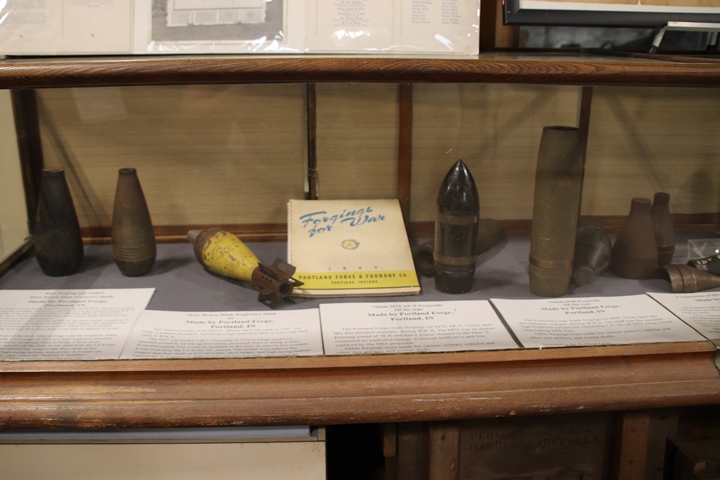
This is part of the Portland Forge & Foundry
display at the Museum of the Soldier in Portland, IN.
Author's photo.
81mm Mortar Shell Forgings: The
Portland Forge produced the rough forgings that were made into the 81mm
M42A1 high explosive mortar shell. It was one of several forges in
the United States that produced this forging.
Table 2 - Total American Industry 81mm M43A1 Mortar Shells
From "Official Munitions Production of the United States"
by the Civilian Production Administration, May 1, 1947 |
Year |
Quantity |
1940 - six months |
12,000 |
1941 |
267,000 |
1942 |
3,147,000 |
1943 |
4,893,000 |
1944 |
6,410,000 |
1945 - eight months |
8,491,000 |
Total |
23,220,000 |
The 23,220,000 high explosive shellswas the most produced of the
four different types of 81mm mortar shells manufactured during World War
Two. It was 63% of the total 37,043,000 mortar shells produced.
It is unknown how many of the 23,220,000 rough forgings the Portland
Forge made.
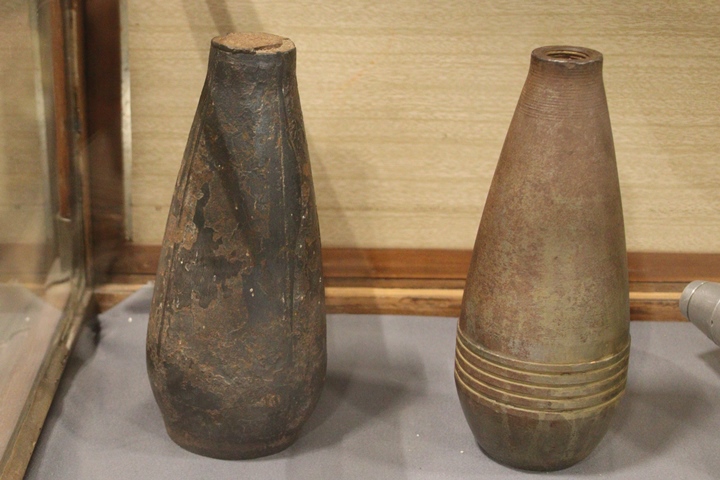
On the left is an 81mm mortar shell rough
forging produced by the Portland Forge and Foundry Company. On the
right is a machined 81mm mortar shell. The Portland Forge only
made the rough forgings, which were then sent to another company for the
machining. In the background is a completed mortar shell.
Author's photo from the Museum of the Soldier.

This is an M43A1 finished 81mm high explosive shell. To make a
complete mortar shell, several different companies furnished different
parts to the final product. The fuse and tail fins also needed to
be built. All of the component parts were then sent to an Ordnance
plant that assembled all the components and then added the explosives to
the final product. The yellow paint indicates this is a high
explosive shell. Author's photo from the Museum of the Soldier.
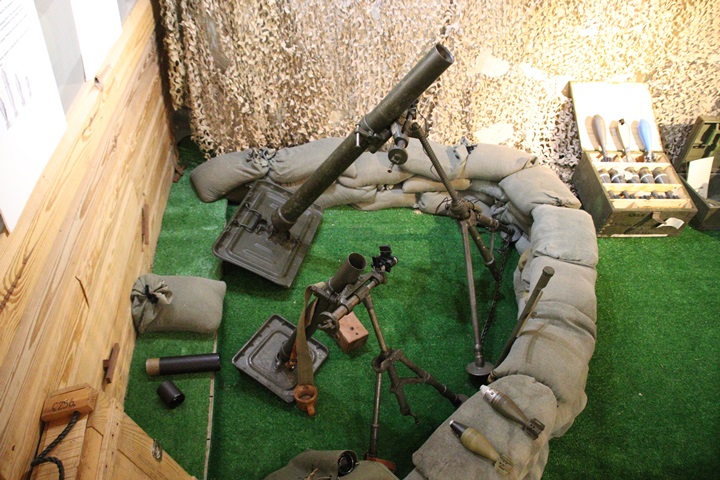
An 81mm mortar is shown at the top of the
image. Author's photo.
37mm Forgings: The Portland Forge
also made 37mm high explosive shell rough forgings for the war effort.
As Table 3 shows, the production of this shell was limited to three
years. This was due to the fact the 37 anti-tank guns were being
phased out at the end of the war.
Table 3 - Total American Industry 37mm M63 and M63, T32 High
Explosive Shells
From "Official Munitions Production of the United States"
by the Civilian Production Administration, May 1, 1947 |
Year |
M63
Quantity |
M63, T32
Quantity
|
1940 - six months |
0 |
0 |
1941 |
0 |
0 |
1942 |
10,229,000 |
,000 |
1943 |
6,336,000 |
158,000 |
1944 |
19,000 |
480,000 |
1945 - eight months |
0 |
0 |
Total |
16,584,000 |
638,000 |
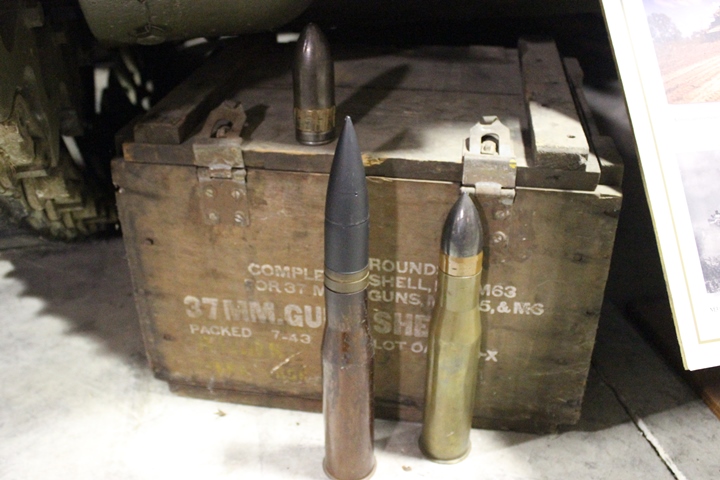
There are two examples of 37mm shells in this photo.
Author's photo.
Below is a series of photos showing the
different types of weapons that used 37mm high explosive shells produced by
the Portland Forge in World War Two.
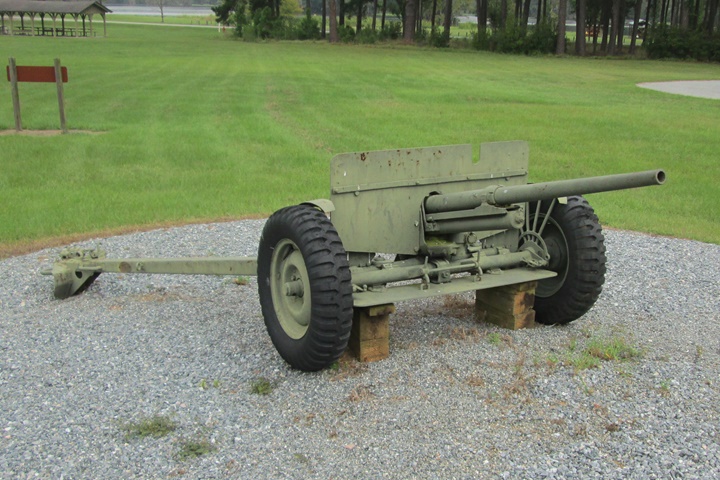
At the beginning of World War Two, the 37mm
anti-tank gun was the primary towed weapon of this type used by the U.S.
Army. It soon became obsolete as German tanks added more armor
plate. Author's photo.
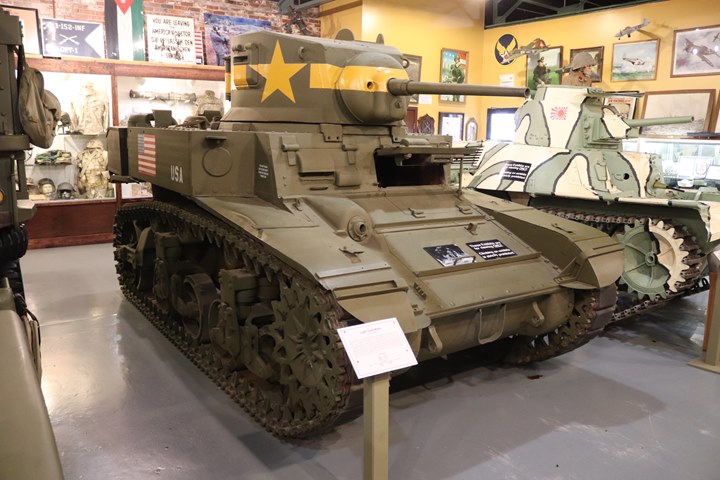
The M3 and M3A1 series light tank was the
light tank of the U.S. Army and USMC at the start of the war. It
was superseded in American service by the M5 series light tank.
However, other Allied forces continued to use the M3 and M3A1 series
light tank until the end of the war.
Author's photo.
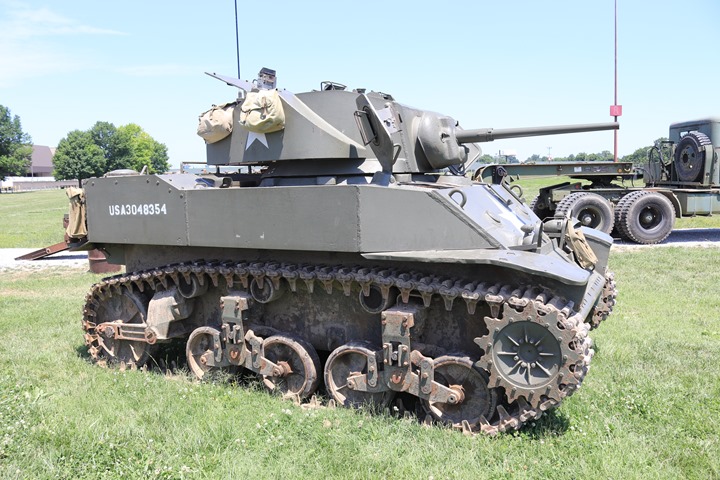
The M5A1 replaced the M3 series light tank with U.S. forces and was
still in use at the end of the war. Author's photo.
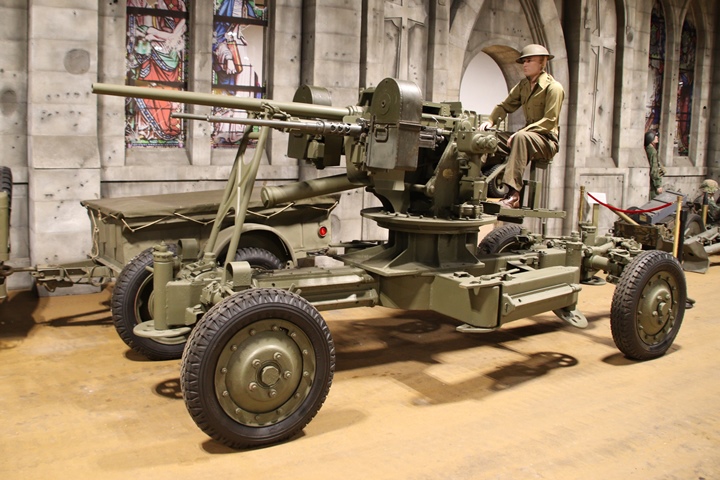
The M3 towed anti-aircraft gun also used
high explosive ammunition. Author's photo.
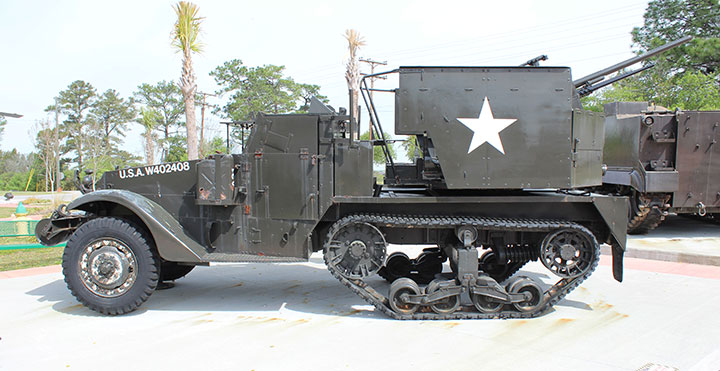
The M15A1 half-track was used to carry anti-aircraft weapons. Author's photo.
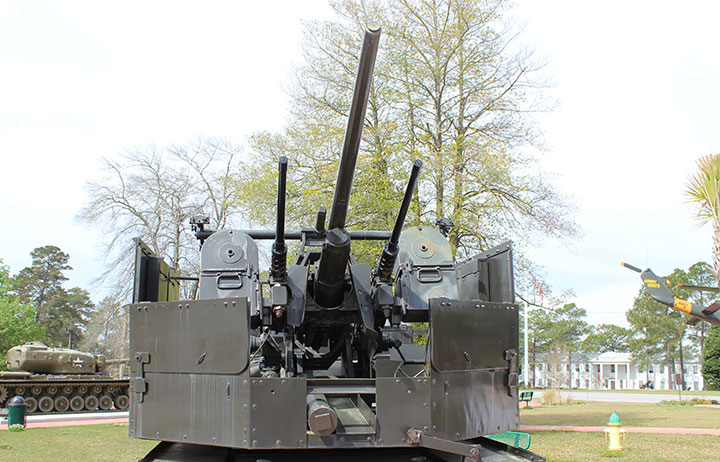
This photo shows the M1A2 37mm anti-aircraft
gun mounted above the M2 .50 Browning machine guns. Author's
photo.
75mm
Shell Forgings: The Portland Forge produced the rough forgings
that were made into the 75mm M72 APC
anti-tank and 75 mm M48 High Explosive Shell. It is unknown how
many forgings for each type of shell the company made. Table 4
shows the total shells for each type made by all manufacturers during
World War Two.
Table 4 - Total American
Industry 75mm M72
APC anti-tank and 75 mm M48 High Explosive Shell
From "Official Munitions Production of the United States"
by the Civilian Production Administration, May 1, 1947 |
Year |
M72 AP-T
Quantity* |
M48 Quantity |
1940 - six months |
0 |
77,000 |
1941 |
0 |
683,000 |
1942 |
4,926,000 |
12,810,000 |
1943 |
7,473,000 |
16,947,000 |
1944 |
4,433,000 |
11,399,000 |
1945 - eight months |
1,304,000 |
4,732,000 |
Total |
18,907,000 |
46,648,000 |
* Includes M61 APC.
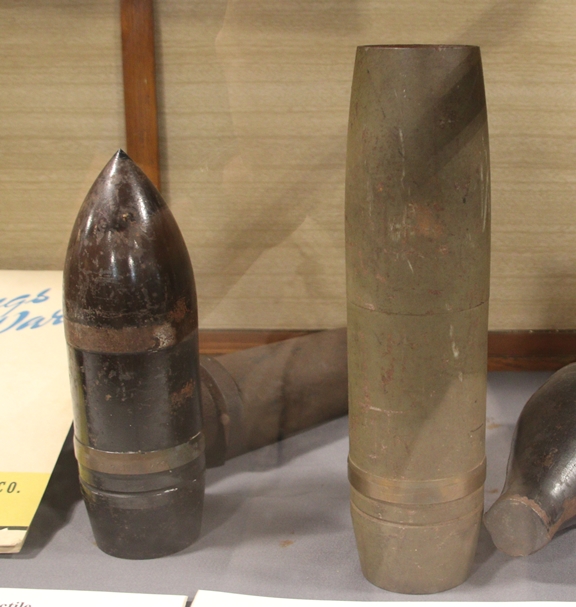
The shell on the left is a completed 75mm
M72 AP-T anti-tank projectile weighing 18 lbs. On the right is a
completed M48 high explosive shell. To be completed, it would have
needed to have been sent to an Ordnance plant to have 1.47 lbs. of TNT
added along with an M48 fuse. Author's photo from the Museum
of the Soldier.
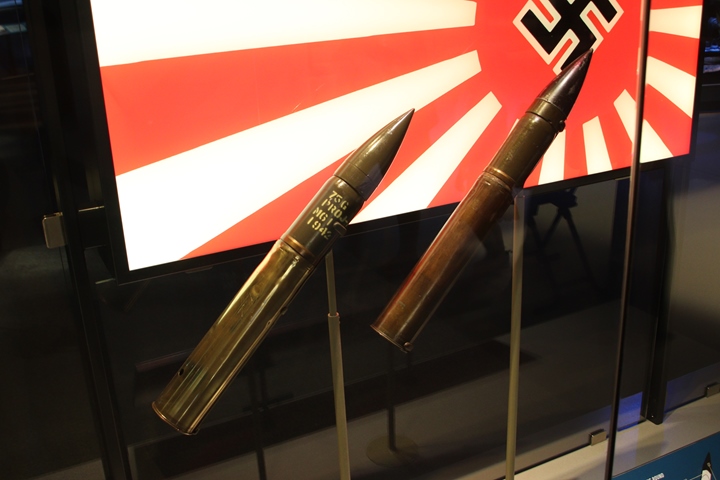
When completed with the shell casing and
fuse, the finished shell forging looks similar to these two 75mm
examples.
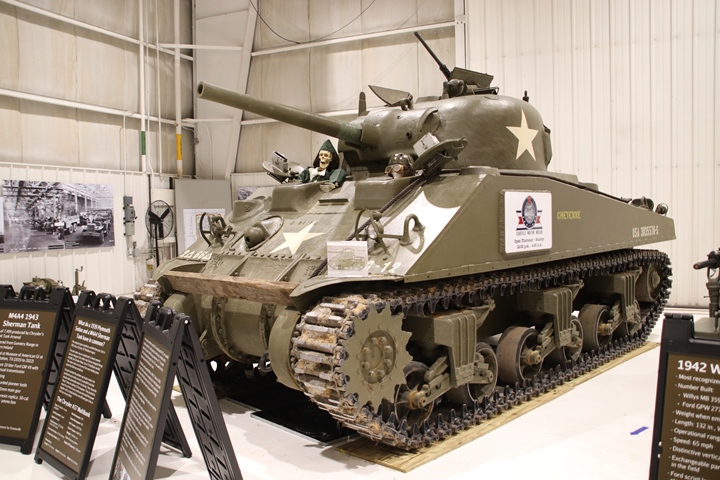
The most common use for the 75MM M48high
explosive shell was in Sherman tanks when they were used in the
infantry support role. High explosive shells were used to destroy
enemy bunkers and fortifications so that the infantry could advance
beyond them. About 75% of the 75mm shells carried in Sherman tanks
were high explosive types. The Sherman tank was also the prime
user of the M72 APC round. This Chrysler-built M4A4(75)VVSS is on
display at the Evansville Wartime Museum in Evansville, IN.
Author's photo.
Other World War Two Products:
Forgings for shells, bomb
bases, bomb noses, Hip flanges, and pipe time flanges. Other
forgings and castings were used in various other types of equipment
such as submarines, landing craft, gun carriages, armored cars, jeeps,
trucks, tanks, airplane tractors, bulldozers, and aircraft.
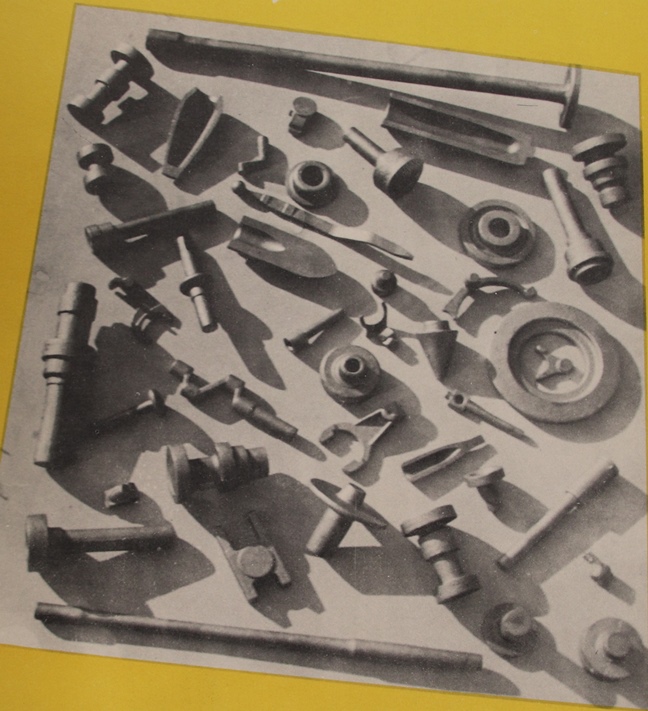
This photo is from the "Forgings for War"
shown below and shows some of the many other components the Portland
Forge made to help win World War Two. This parts appear be
castings.
"Forgings for War:" This is a
1943 publication by the company on its efforts to provide forgings and
castings for the war effort. This is part of the collection at the
Museum of the Soldier in Portland, IN. It is always most helpful
to find a primary source document written by a company during World War
Two to obtain an inside look from the company.
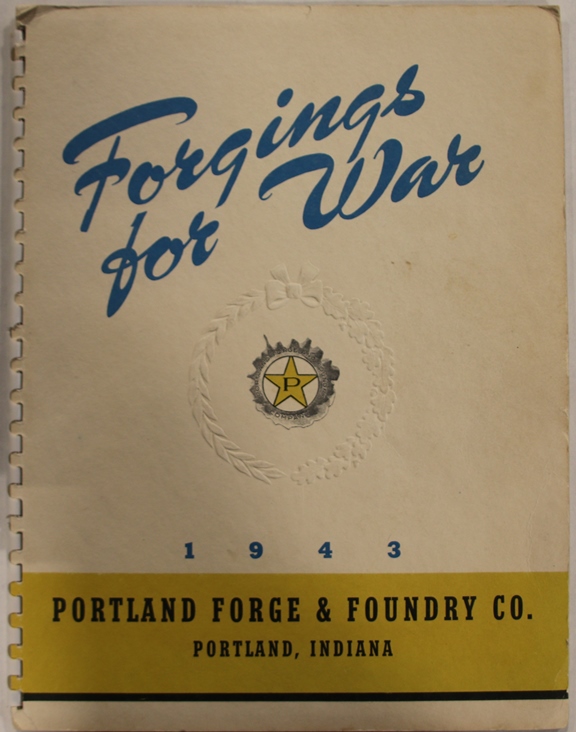
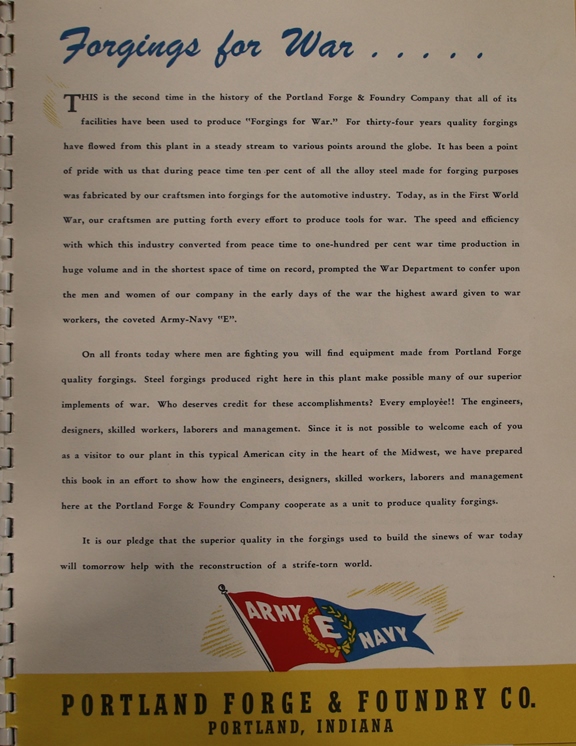
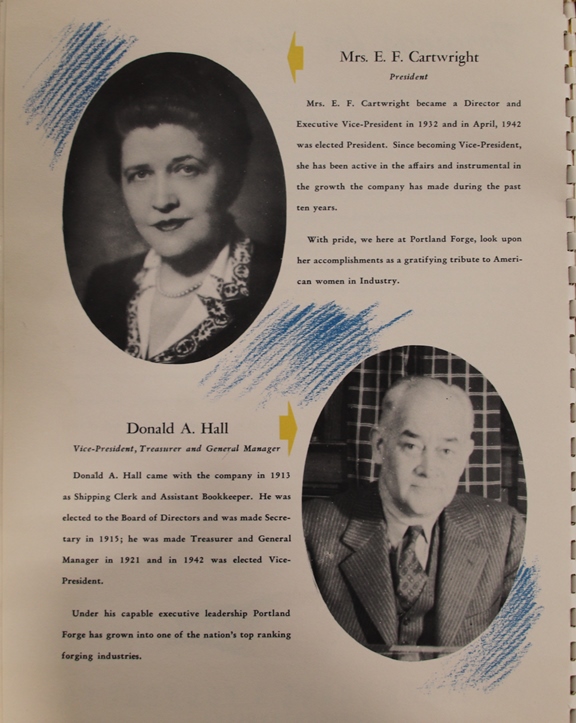
Mrs. E.F Cartwright was elected president of
the company in April 1942. This woman was way ahead of her time. For
a woman to be elected president of any company in the 1940s was unheard
of. To be elected to that position in a male dominated forge plant
in a small conservative farming community in rural Indiana is even more
amazing. She must have really been an outstanding leader and
business person!
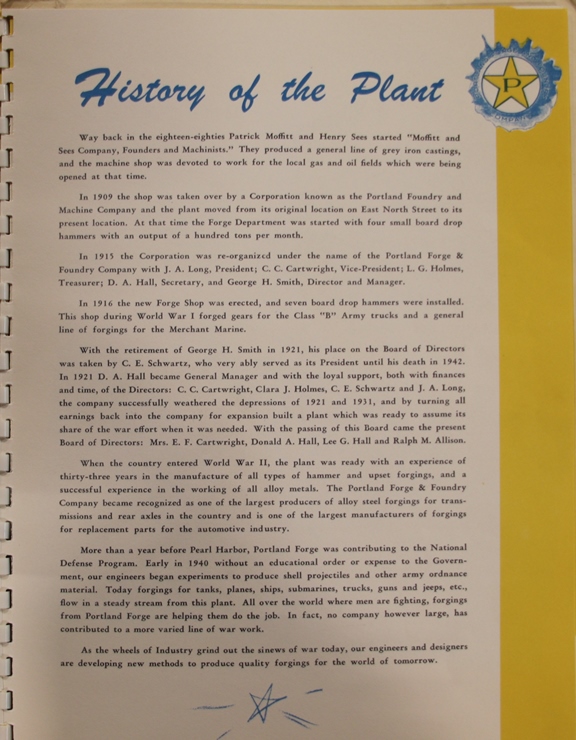
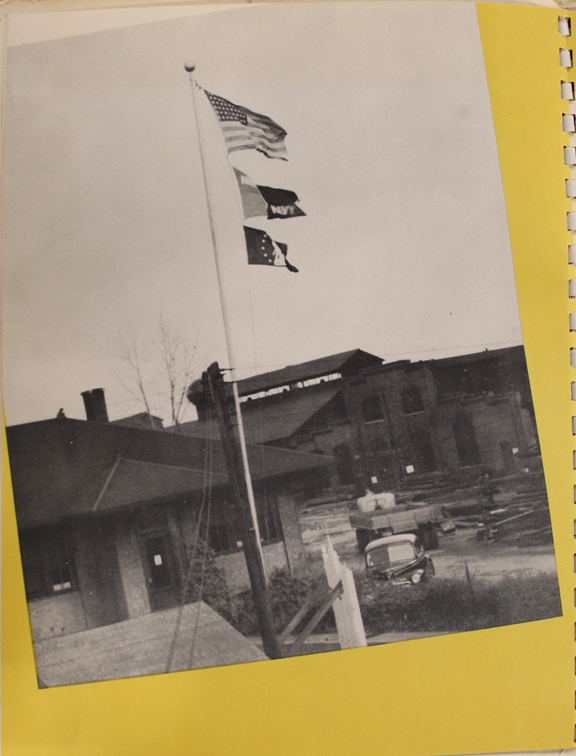
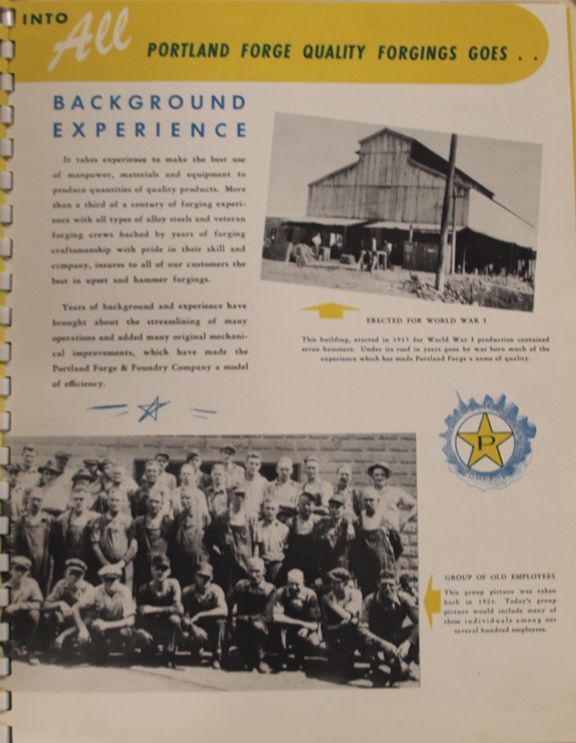
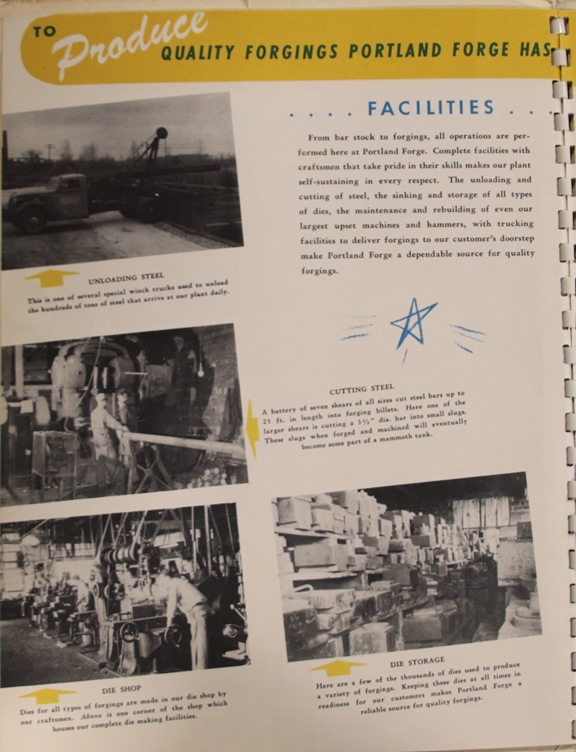
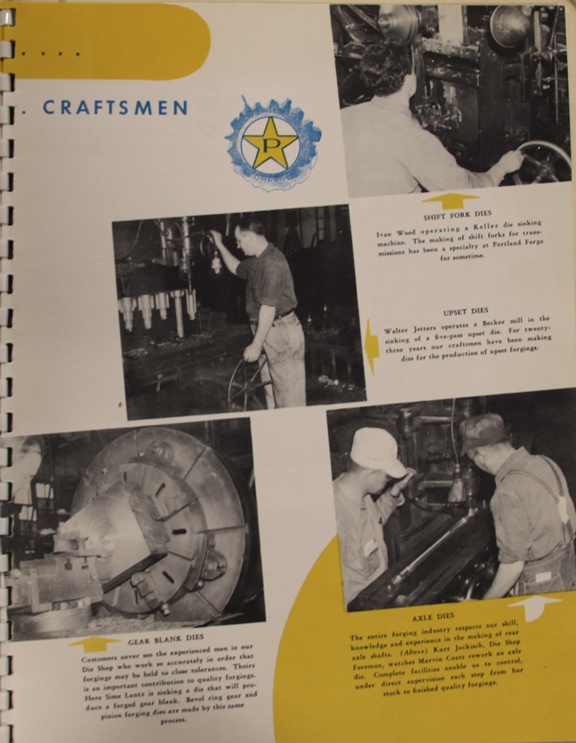
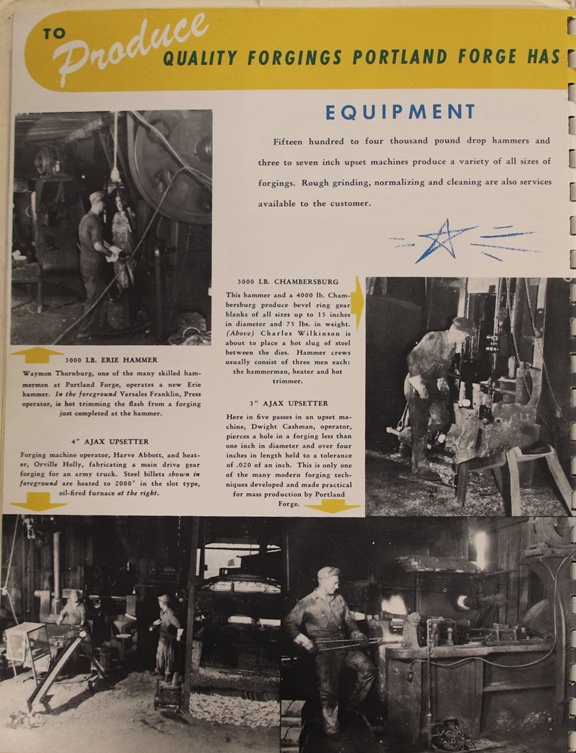
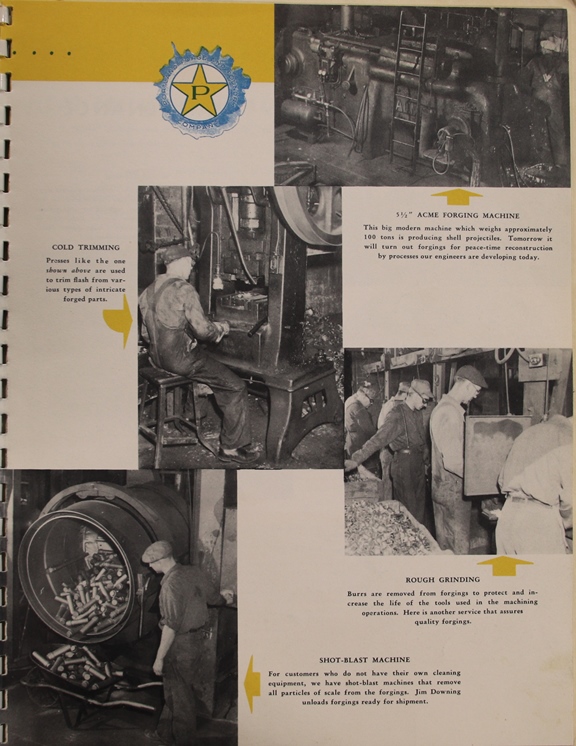
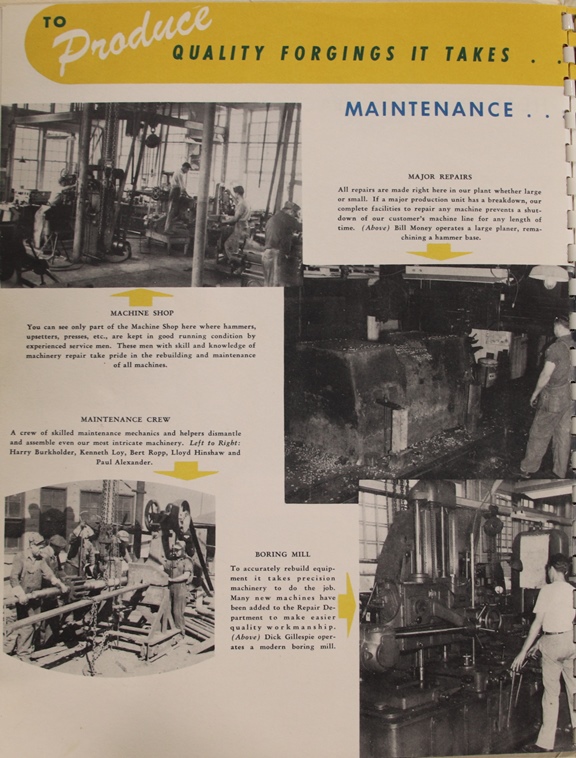
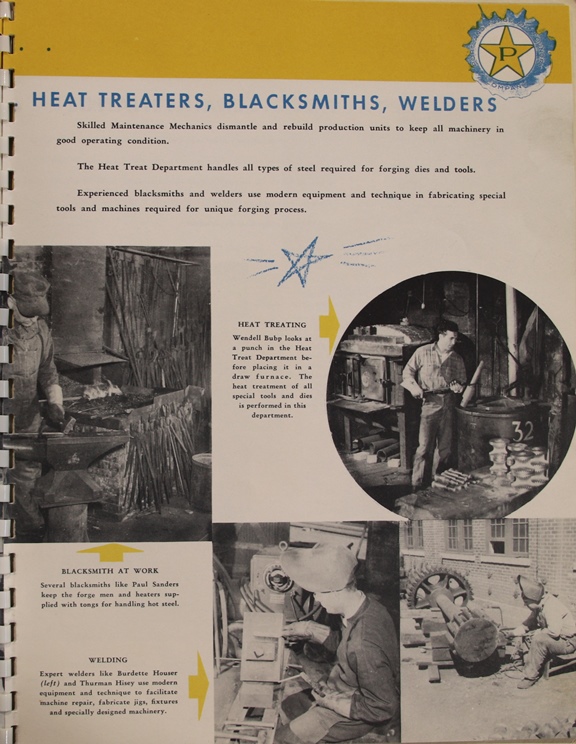
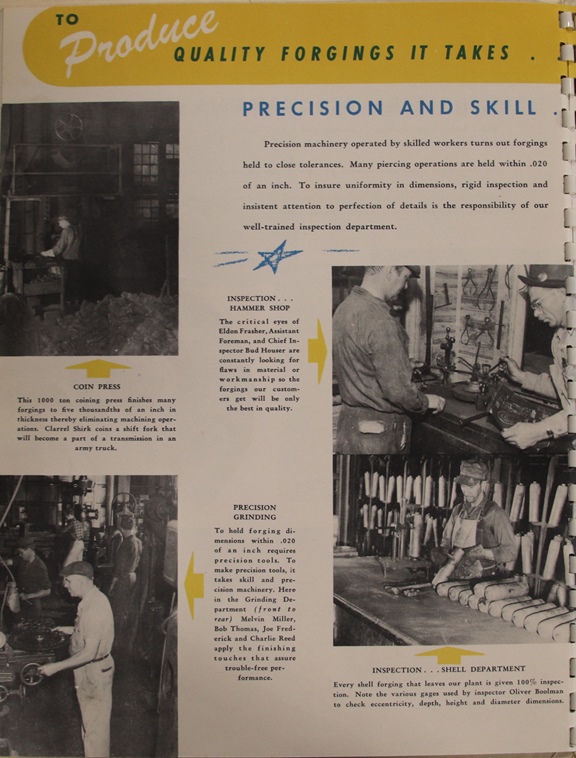
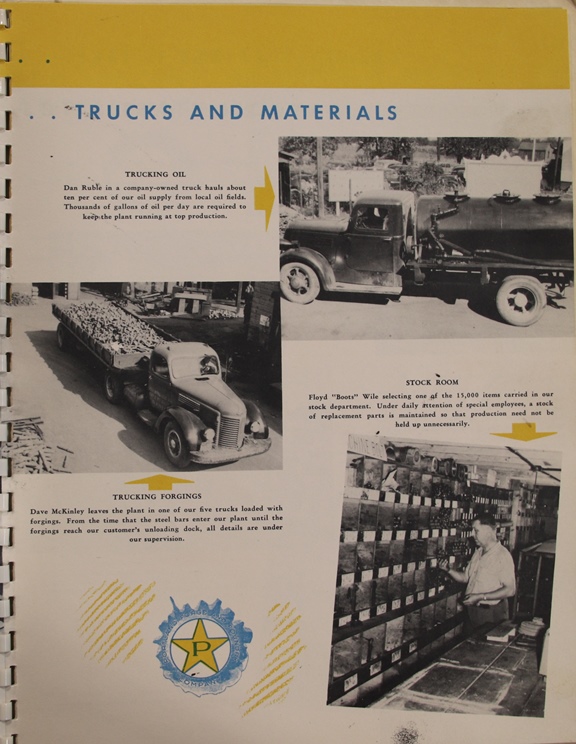
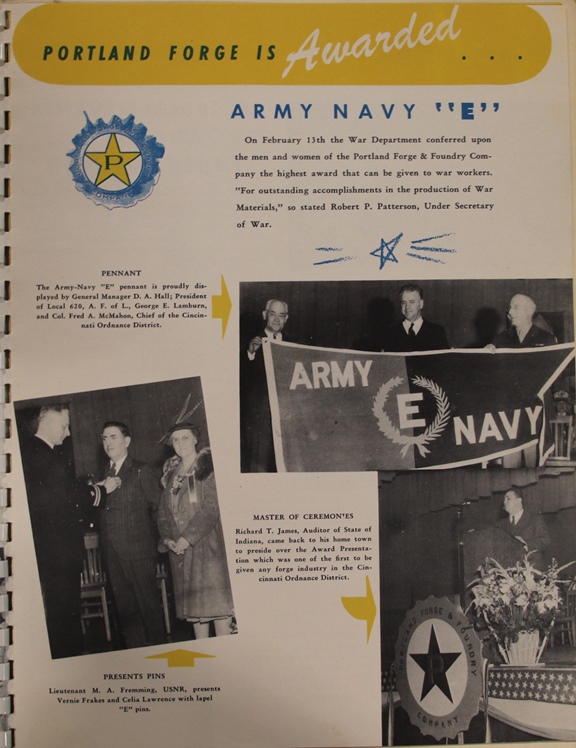
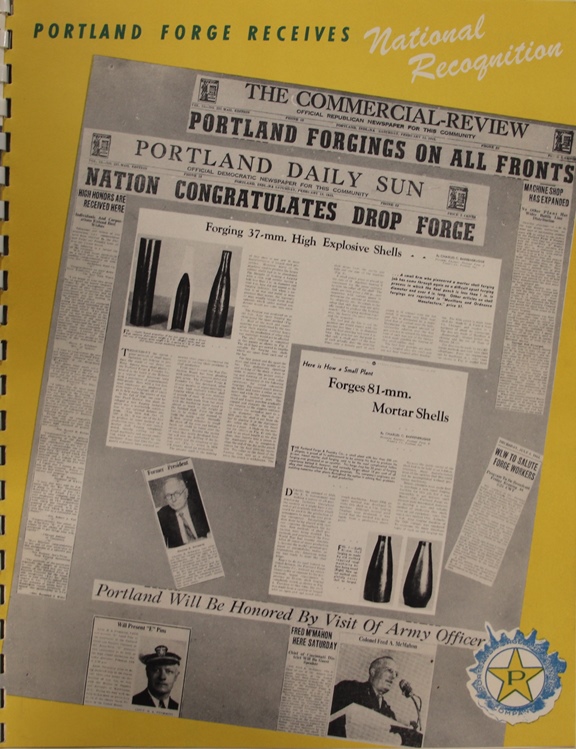
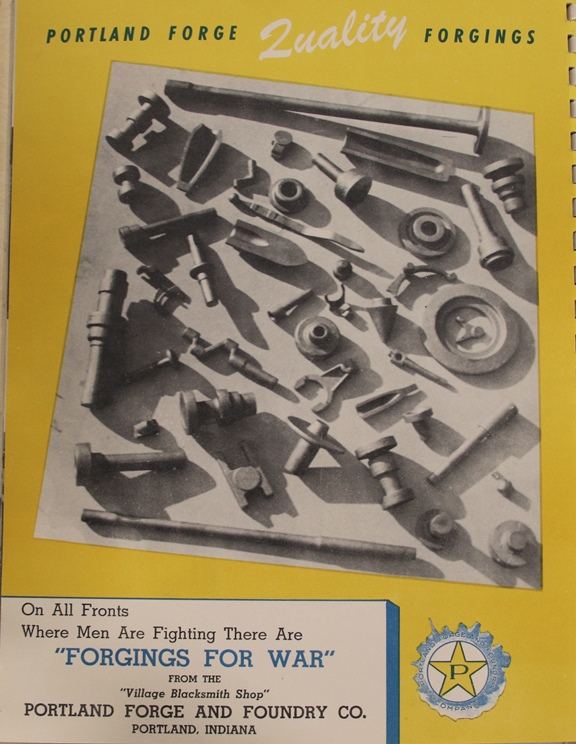
|