War
Production by Otis Elevator
Otis
Elevator in World War Two
Yonkers, NY
1852-1976
1976-Present as a subsidiary of United Technologies
This page added 6-18-2021.
I never had any intention of publishing a page
on the Otis Elevator Company of Yonkers, NY. It had not even
crossed my mind, as the company is not at all related to the American
Automobile Industry. However, as is the case with many of my pages,
fate would intervene, and I would learn how many different products Otis
Elevator made to help win World War Two.
On a return trip from Florida, I stopped in
Calhoun, GA to take several photos of a Pressed Steel M4A1 Sherman tank
at the National Guard Armory. I was aware that next door at the
American Legion there was also a 90mm anti-aircraft gun on display.
However, I was focused on the Sherman tank, not thinking the
anti-aircraft gun would produce anything new for me. How wrong
I was! On the gun was a data plate indicating that the recoil
mechanism was built by the Otis Elevator Company. It turns out
that Otis produced 3,961 or 50% of the recoil mechanisms for the 90mm anti-aircraft gun
during World War Two.
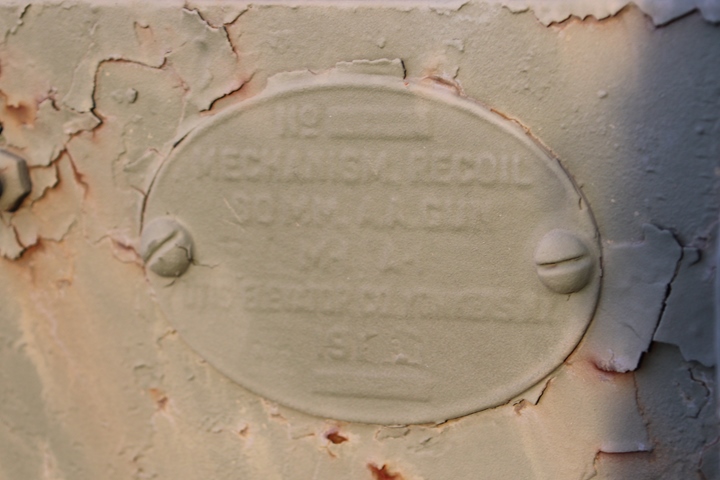
The data plate is difficult to read with
several coats of paint on it, but Otis Elevator built this recoil
mechanism for this M1A1 90mm anti-aircraft gun in 1943. Author's
photo.
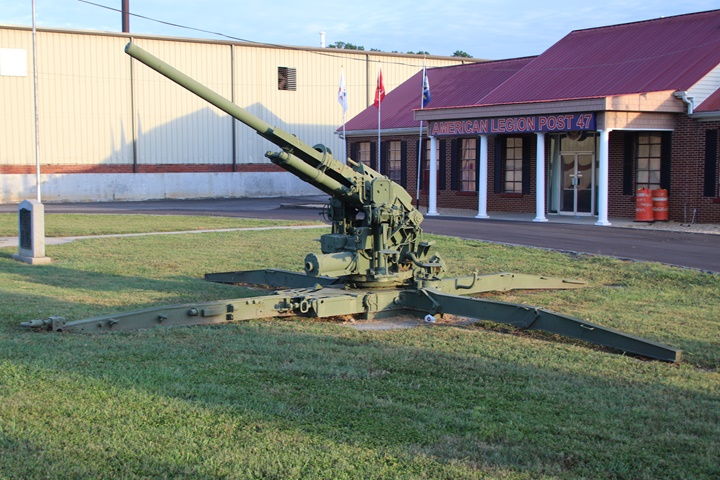
It was early in the morning and the sun was just rising in Calhoun, GA.
Author's photo.
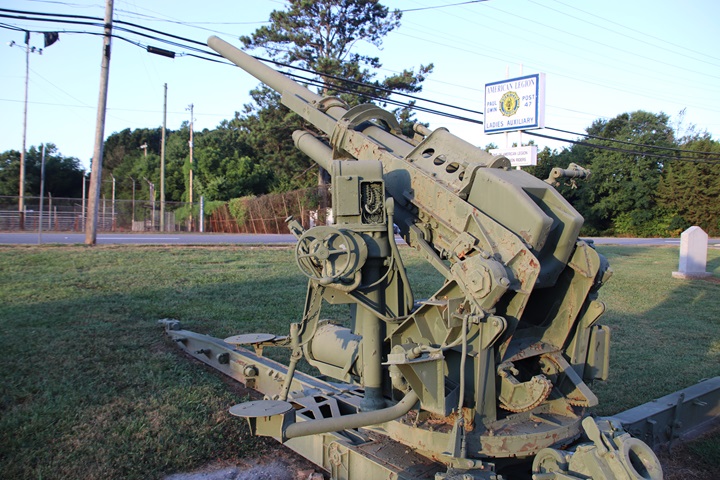
Author's photo.
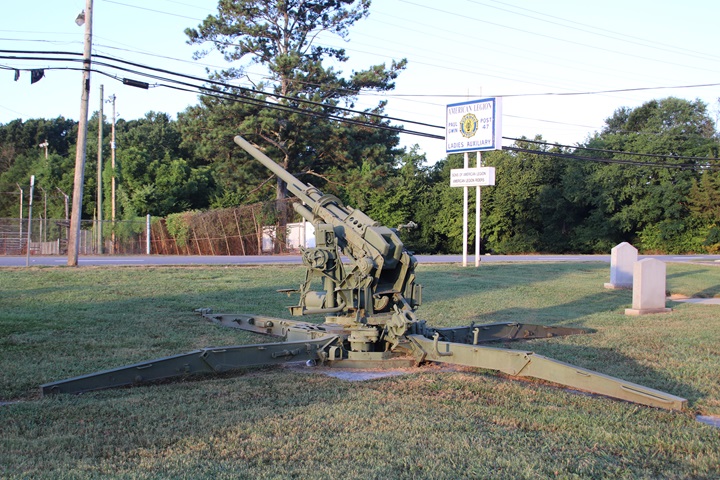
Author's photo.
Upon my arrival home and things were
unpacked, I did an internet search on Otis Elevator in World War Two and
found the 107 page book "War Production by Otis." Upon its arrival
a week later, I was amazed by the amount of information contained in
this 1947 publication. It is one of the most comprehensive
publications I have found that details a company's contribution in
helping to win World War Two. This excellent account of how Otis
Elevator helped win World War Two is in the link at the top of the page.
Otis Elevator is known for its elevators and
escalators, found in many buildings in the United States. Like many
companies during World War Two, Otis produced large quantities of
military equipment totally unrelated to its normal peace-time product
line. Otis Elevator was prolific in both the variety and volume of products
it manufactured to help win World War Two. It stands
as an excellent example of how American industry rose to the occasion,
re-tooled its plants, and turned out the needed equipment to win World
War Two.
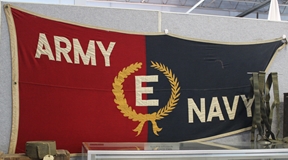
The
Aeronautical Division, Harrison, NJ won the Army-Navy "E" Award four times
during World War Two. The first award given on October 24, 1942.
The
Yonkers Works, Yonkers, NY won the Army-Navy "E" Award five times during
World War Two. The first was giving on August 15, 1942, and last on January 6, 1945.
The Otis Buffalo Works won the Army-Navy "E" Award four times during
World War Two.
Harrison Works Elevator Division, NJ won the Army-Navy "E" Award one time on July 10,1945.
Otis World War Two Products:
Aeronautical Division,
Harrison, NJ: This brand new
building was built for the manufacture of crankcases for the
Wright R-2600 radial engine. Construction began in February 1941 with
the first crankcases
shipped on October 11, 1941. Production demand for 2,500 crankcases
per month
required a second building erected at this location for machine tool
operations. This plant began producing parts on November 16, 1942.
The Otis Aeronautical Division began producing Wright R-3350 crankcases
for the B-29 in February 1945.
Yonkers Works,
Yonkers, NY: This plant
produced a variety of products for the war effort. This included: 3,961 90mm anti-aircraft gun recoil mechanisms, 78,710 navy electrical
bomb shackle release mechanisms, recoil mechanisms for 155mm cannons,
recoil mechanisms for 120mm anti-aircraft guns, Navy five-inch gun ammunition racks and
servers, C-46 tail landing gears, P-40 wing flap cylinder assemblies,
B-26 bomb hoists, B-26 engine hoists, and P-47 down lock cylinders.
Yonkers,
NY Aluminum Foundry:
The foundry produced castings for Otis-built products plus castings
other companies for B-17, F6F, PBM-5, C-46,
P-47, 1,486 machine tools, motors and generators, many for GE amplidynes , Sperry
searchlight trunnions,
Lawrance crankcases for US Navy, recoil mechanisms for 90mm
anti-aircraft guns, 155 long toms and 120mm anti aircraft guns, navy
five inch ammunition racks and servers, C-46 tail landing gear,
P-40 wing flap cylinder assembly, B-26 bomb hoists, B-26 engine
hoists, P-47 down lock cylinders, and 8,710 navy electrical bomb shackle release
mechanisms.
Harrison Works, Harrison, NJ: Elevator platforms and
ammunition hoists for navy cruisers, parts for 27,000 welding
generators, cradles for 4,000 for recoil mechanisms, assemblies for
torpedo hoisting equipment, parts of mine handling elevators and
mine layers, C-46 landing strut, PBM-3 and PBM-5 tail and top turrets,
87,000 shock mounts for aviation cameras and radios, 750 Morey 2-spindle
No.12 vertical profilers, large number of Morey turret lathes, Lawrance
Avilectric power plants for the B-17 and B-24 auxiliary generators, steam driven
pumps for Liberty ships, and P-47 cowl rings.
Buffalo Works, Buffalo, NY: Aircraft carrier aircraft
elevators, turret rings for Martin aircraft, PBM beaching gear, various
steel castings including 120mm anti-aircraft gun, various drop-forged
parts, and 37mm gun mounts for the Dutch Royal Navy.
Otis-Fensom Elevator Company, Hamilton, ONT:
5,000 40mm Bofors anti-aircraft guns, twin 40mm Bofors mounts for
Royal Canadian Navy and Royal Navy ships, truck-mounted 40mm Bofors
single mounts, 200 40mm Bofors mobile mounts, 30,000 40mm gun barrels,
8,000 40mm Bofors electrical-hydraulic fire control mechanisms, 76mm
muzzle brake for U.S. Army, 6-pounder gun mounts for the Ram tank, 40mm
Bofors elevating training mounts for U.S. Navy, light-weight ammunition
trailers, engine lathes, bombing teaching assemblies, 20mm mobile quad
mount sub-assemblies, Lancaster and Lincoln tail wheel assemblies,
Mosquito 20mm gun mounts, radar rotator assemblies, various castings
Aeronautical Division,
Harrison, NJ Product Photos:
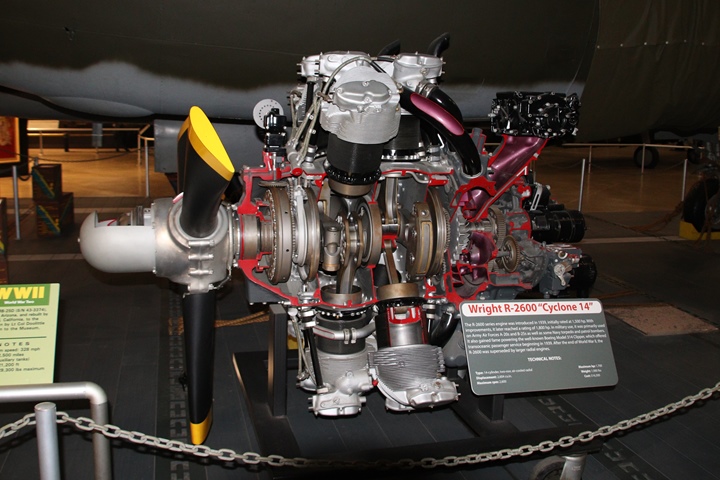
This cut-away of an R-2600 is on display at
the National Museum of the United States Air Force. The outline of
the crankcase is painted in red on this example. Assuming Otis
Harrison, NJ plant came to full production of 2,500 crankcases per month
in October 1942, the company built at least 90,000 R-2600 crankcase
during the war. Author's photo.
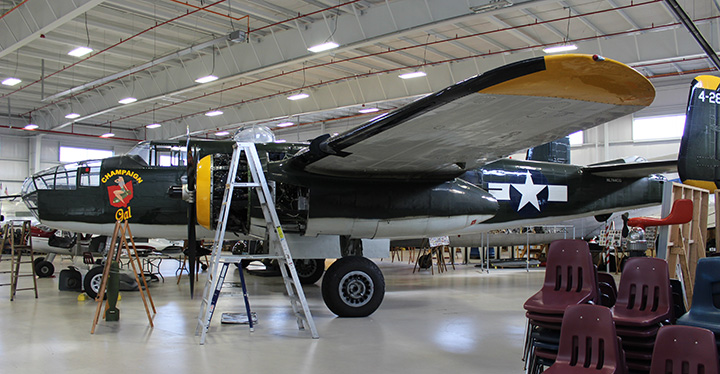
The North American B-25 had R-2600 engines.
Author's photo.
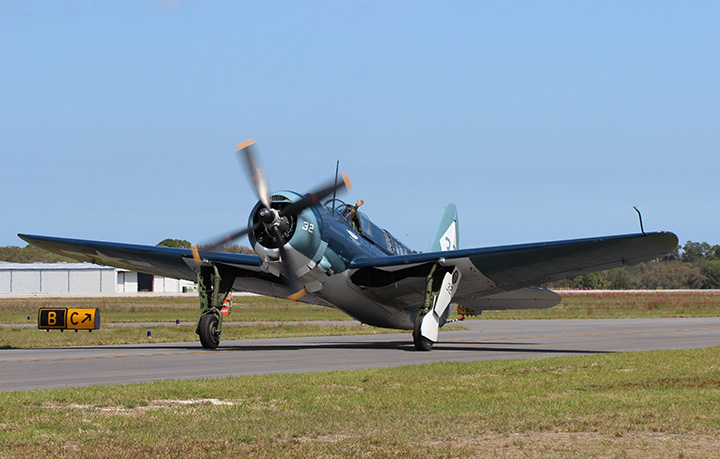
The U.S. Navy's Curtiss SB2C was powered by
the Wright R-2800 with Otis-manufactured crankcases. Author's
photo.
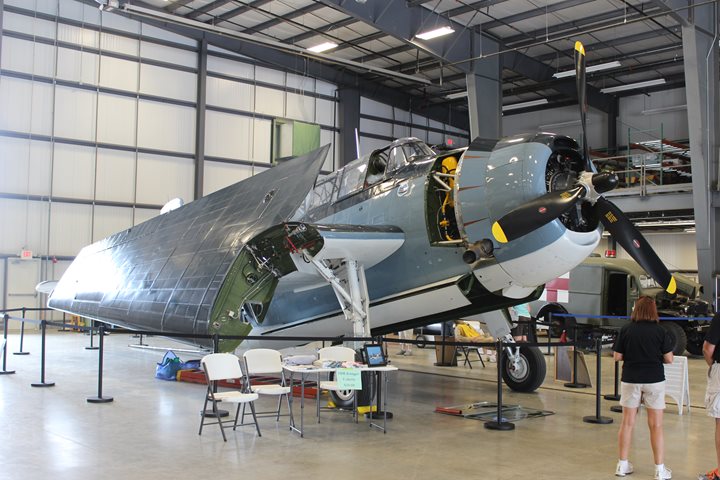
The R-2600 was the power plant for the
General Motors Eastern Aircraft Division's TBM Avenger torpedo aircraft.
Author's photo.
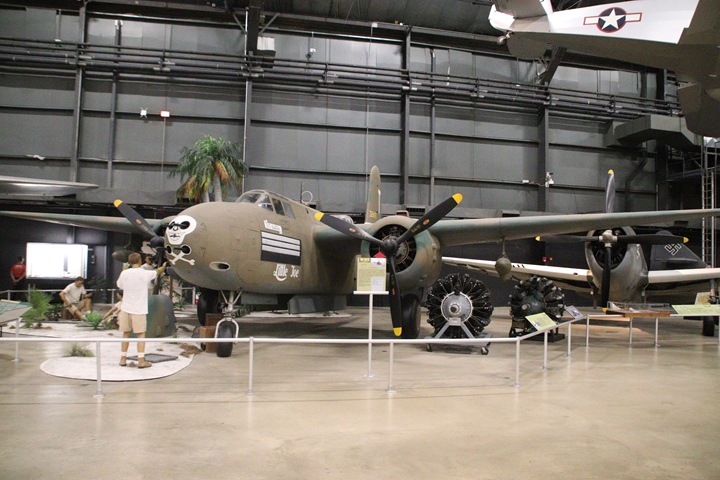
The Douglas A-20 attack aircraft used two
R-2600 engines with Otis crankcases. This A-20 is on display at
the National Museum of the United States Air Force. Author's
photo.
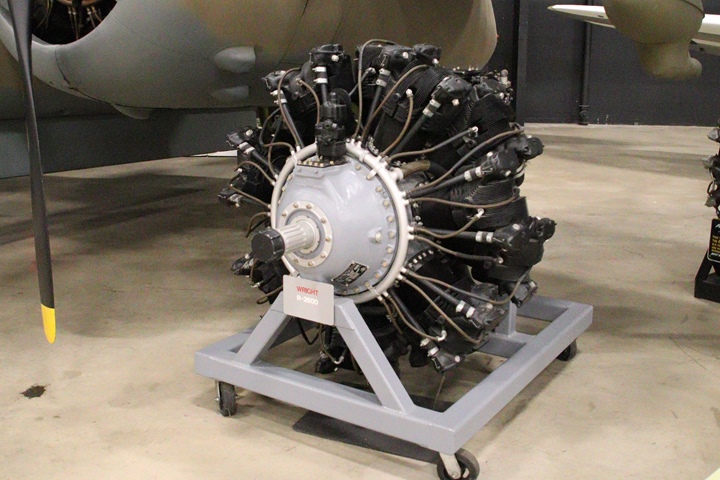
This R-2600 engine is on display next to the
A-20. Author's photo.
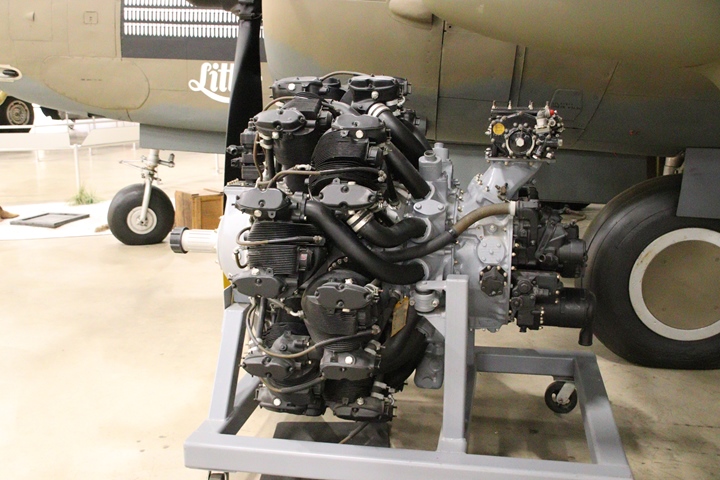
Author's photo.
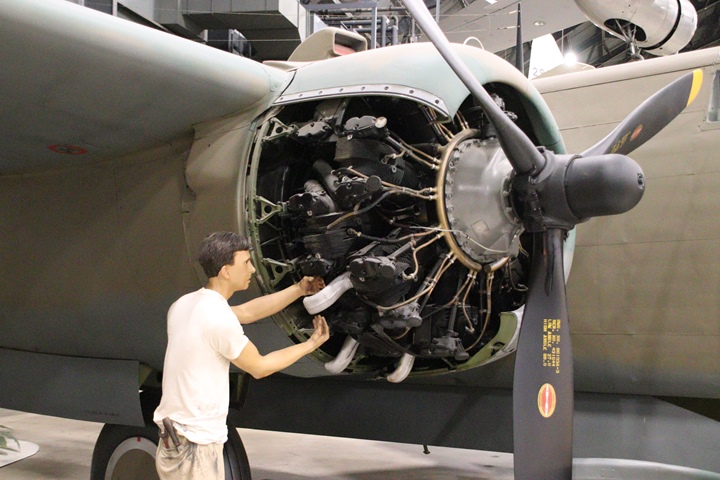
This diorama shows the R-2600 installed on
the A-20 with part of the engine cowling removed. Author's photo.
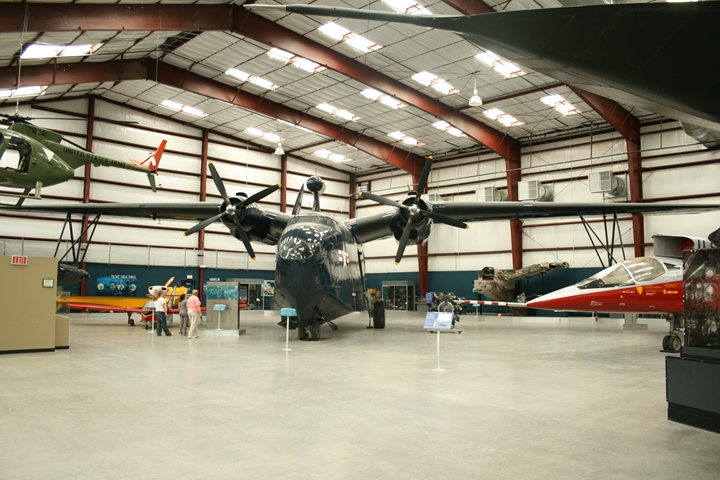
The early versions of the Martin PBM were
powered by R-2600 engines. The Otis Harrison Works produced top
and rear gun turrets for the PBM-3 and PBM-5 aircraft. Author's
photo.
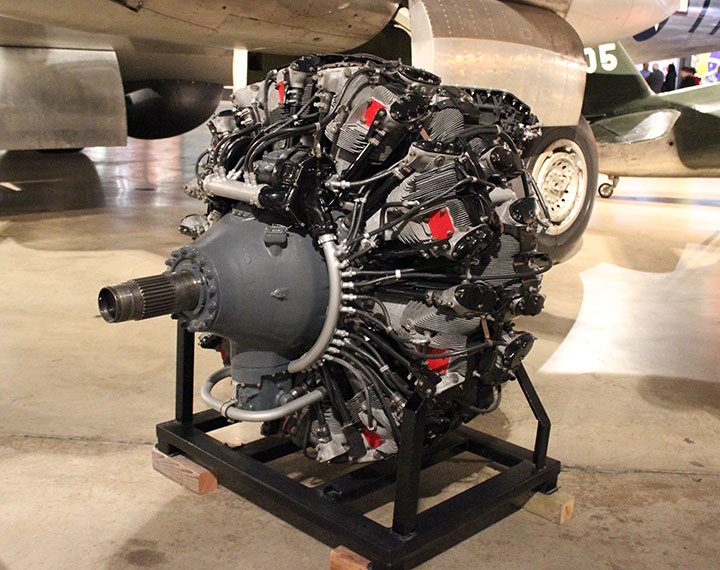
In early 1944 Otis began tooling up to
manufacture the Wright R-3300 crankcase which powered the B-29.
First delivery of the engine was in February 1945. Author's photo.
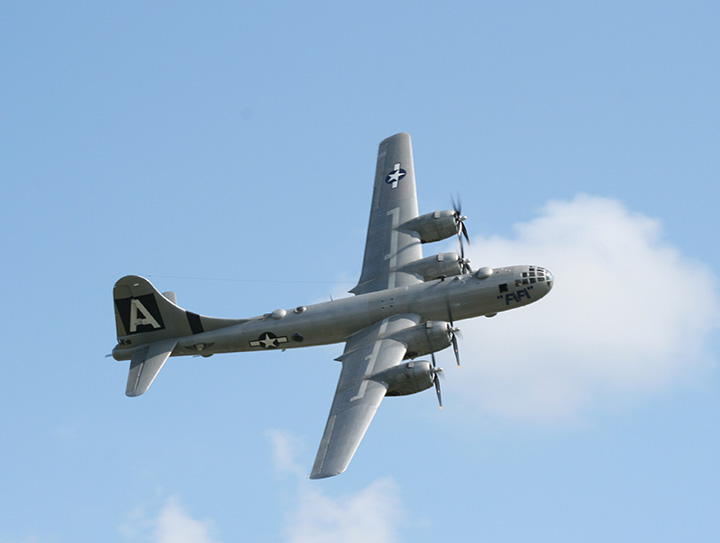
This is only one of two B-29s still flying.
It may well have Otis-built crank cases in the R-2250 engines. Author's photo.
Yonkers Works, Yonkers, NY Product Photos:
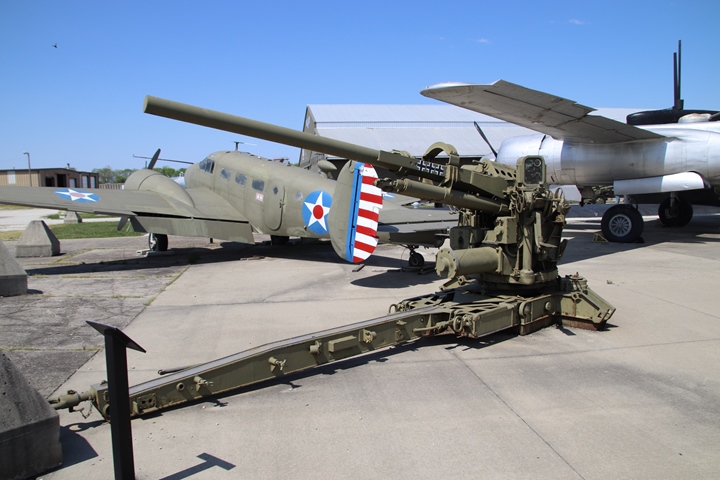
This 90mm anti-aircraft gun on display at
the Indiana Military Museum in Vincennes, IN is equipped with an Otis
recoil mechanism. Otis built 3,961 of the 7,831 recoil mechanisms
required during World War Two. This was 50% of the total.
Author's photo.
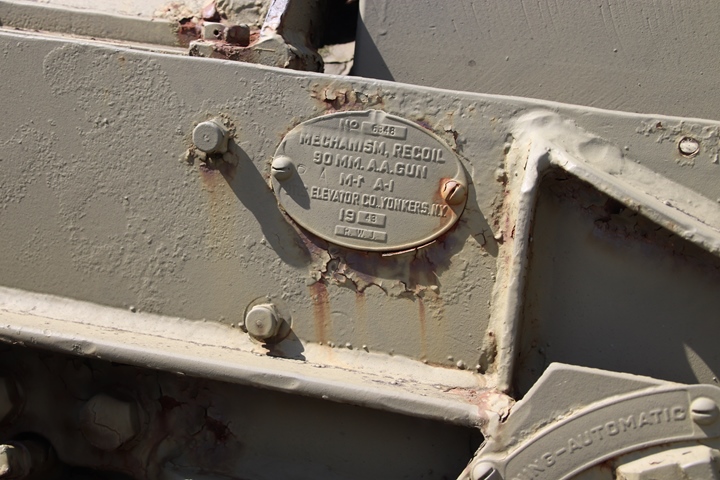
The Otis Elevator recoil mechanism is serial
number 6848 and was built in 1943. Author's photo.
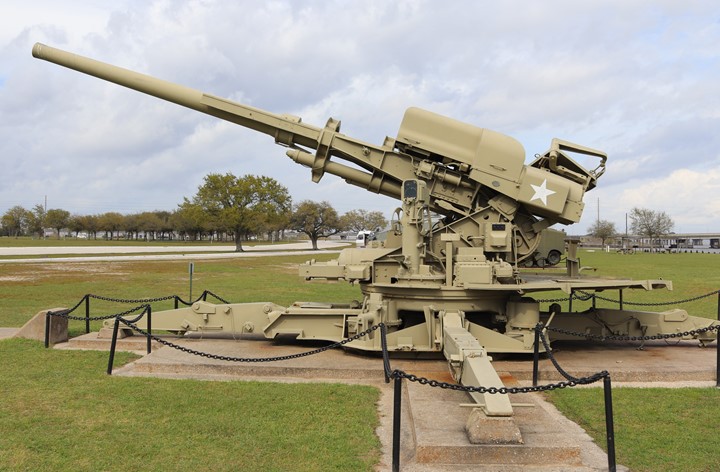
Otis produced recoil mechanisms for the 550 120mm M-1 anti-aircraft guns
produced at the Fisher Body Division of General Motors Grand Rapids, MI
plant. Author's photo.

The Otis Elevator Company in Yonkers, NY also built recoil mechanisms
for the 155mm "Long Tom" cannon. Author's photo.
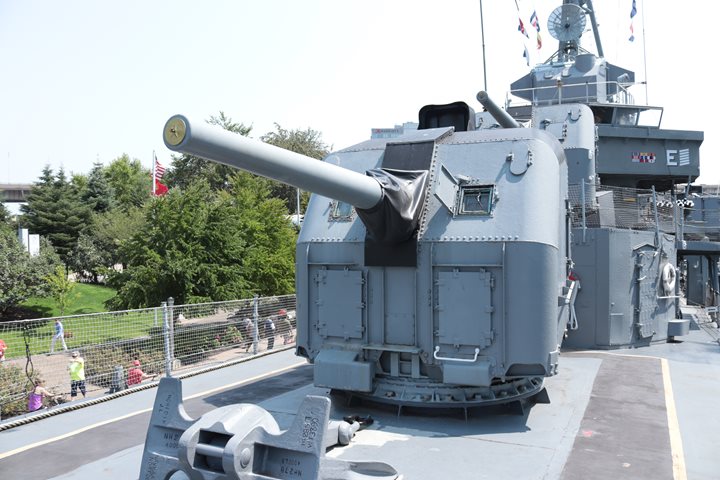
This five-inch, 38 caliber gun can be
seen at the USS Sullivans at the Buffalo and Erie County Naval and
Military Park in Buffalo, NY. The ammunition for the five inch
guns was fed into the gun turret from below deck. Otis Elevator's
Yonkers' plant provided the ammunition racks and servers to keep these
rapid firing weapons provided with ammunition. Author's photo.
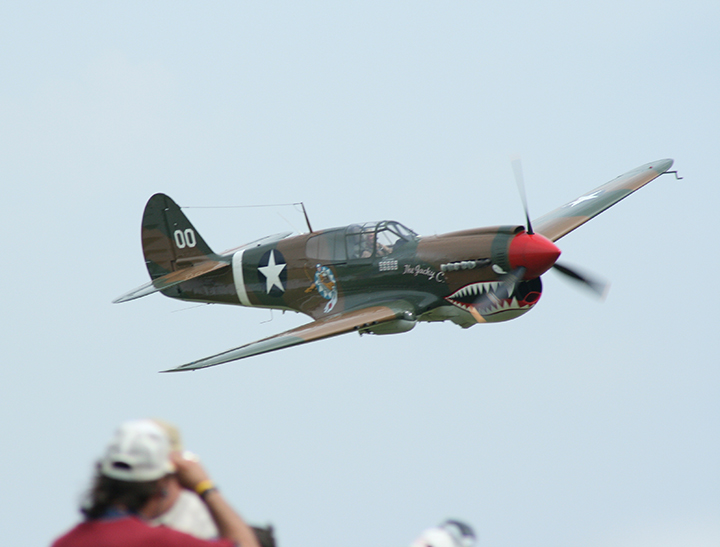
The Yonkers Works produced Curtiss P-40 wing flap cylinder assemblies.
Author's photo.
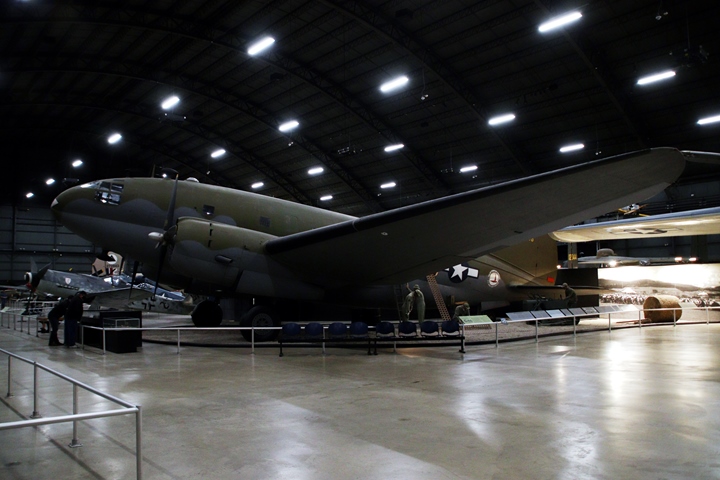
Both the Otis Yonkers and Harrison Works
produced landing gear components for the Curtiss C-46. This C-46
is on display at the National Museum of the United States Air Force.
Author's photo.
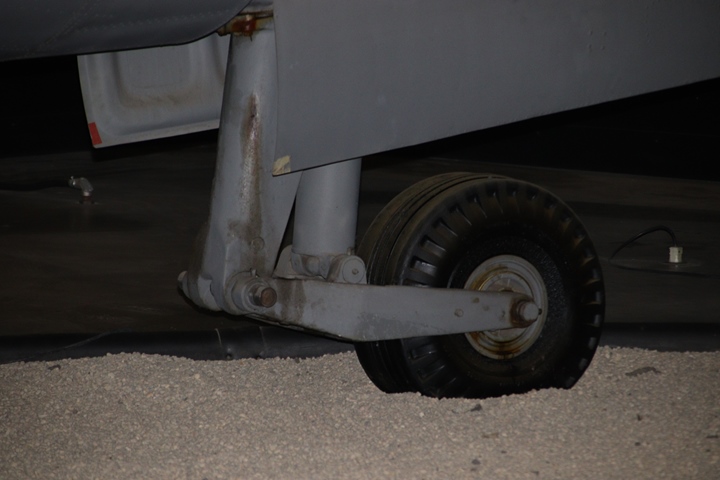
Yonkers produced the tail landing gear.
Author's photo.
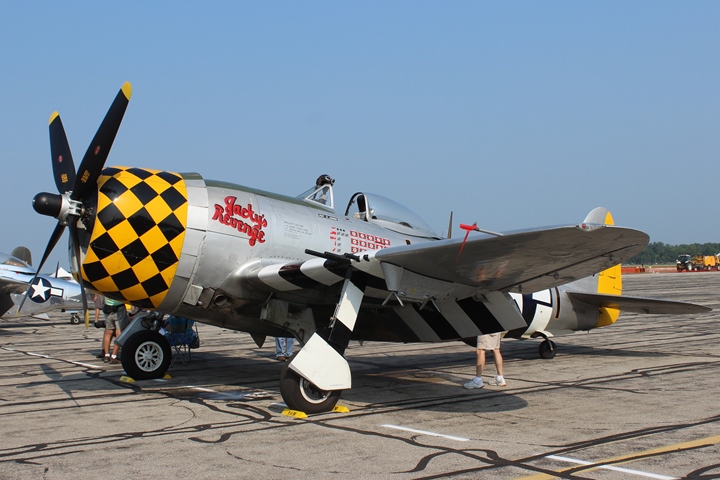
Both the
Otis Yonkers and Harrison Works produced components for the Republic
P-47. Yonkers manufactured the down lock cylinders for the landing
gear. Author's photo.
Curtiss, Eastern Aircraft, Martin, Republic,
and Wright were all located on the east coast. This made
Otis Elevator Company an excellent choice for supplying components for
these aeronautical companies.
Yonkers,
NY Aluminum Foundry Product Photos:
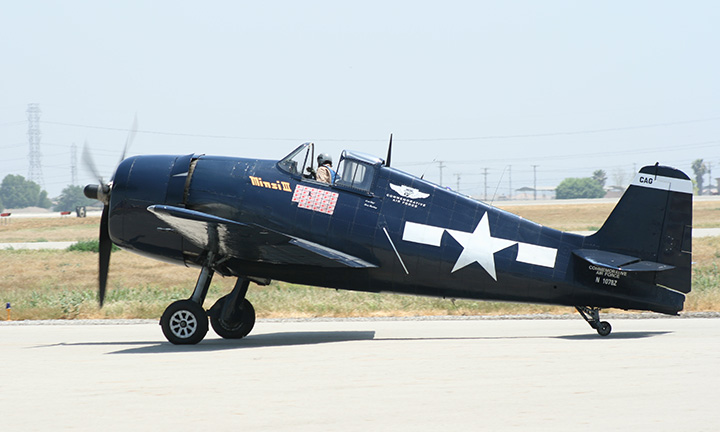
Grumman Aircraft on Long Island, NY was
another east coast aircraft company for which Otis supplied parts. The
Yonkers Foundry cast parts for the Grumman F6F fighter. Author's
photo.
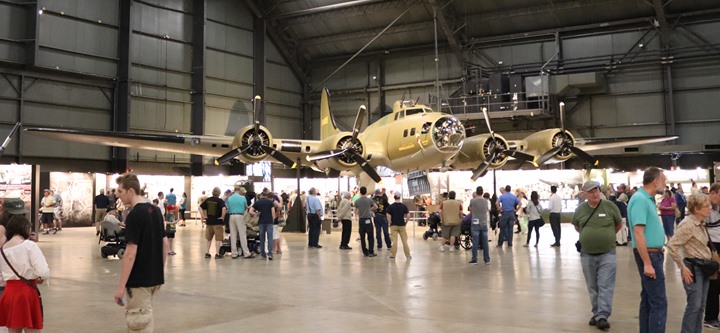
The Yonkers foundry cast components for the
B-17 bomber. Unlike the other parts Otis built for different
aircraft, the B-17 was not built on the east coast of the United States.
It was built in Washington and California. Author's photo.
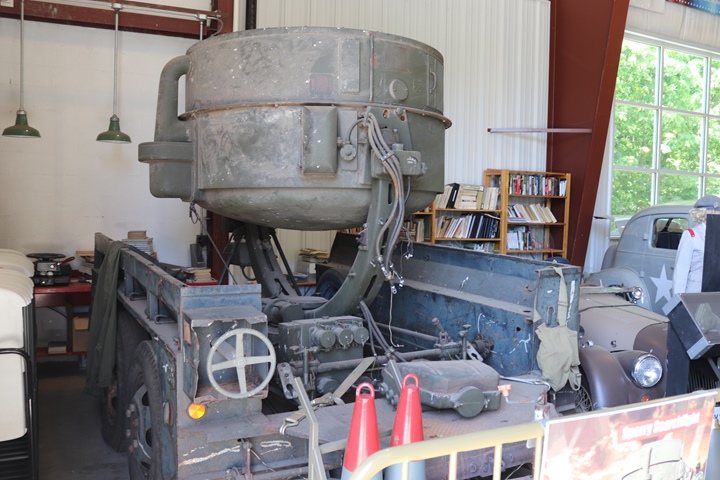
The Yonkers foundry cast the trunnions for
the Sperry searchlight. The trunnion is the U-shaped device.
Author's photo.
Harrison Works, NJ Product Photos:
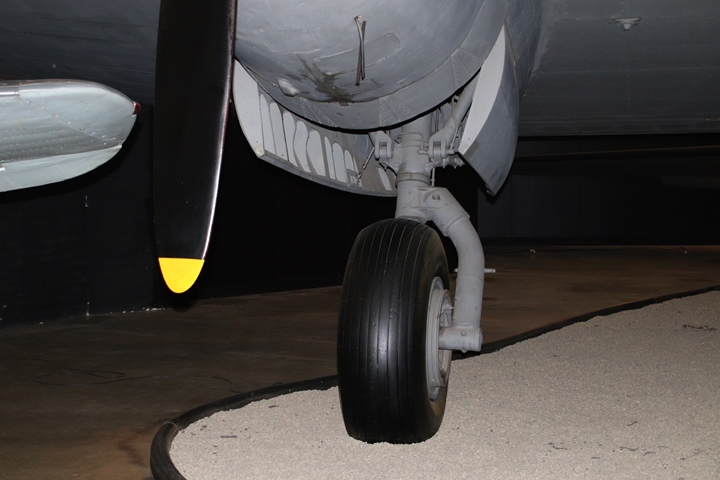
Harrison Works produced the landing gear
strut for the Curtiss C-46. This is the strut for the starboard
landing gear on the C-46 shown above. Author's photo.
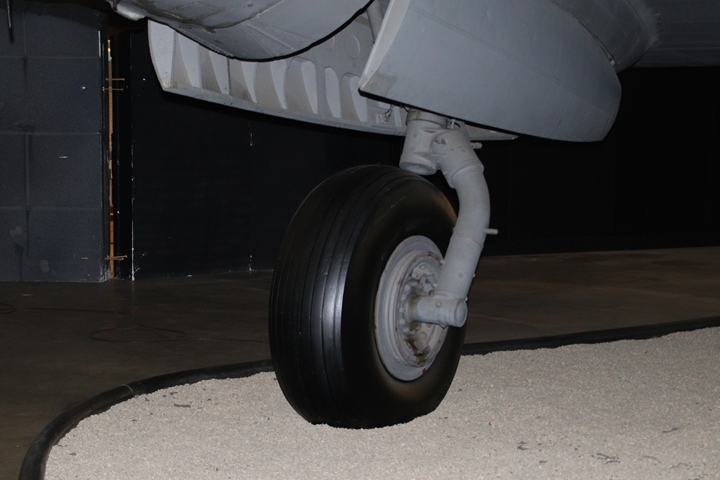
Author's photo.
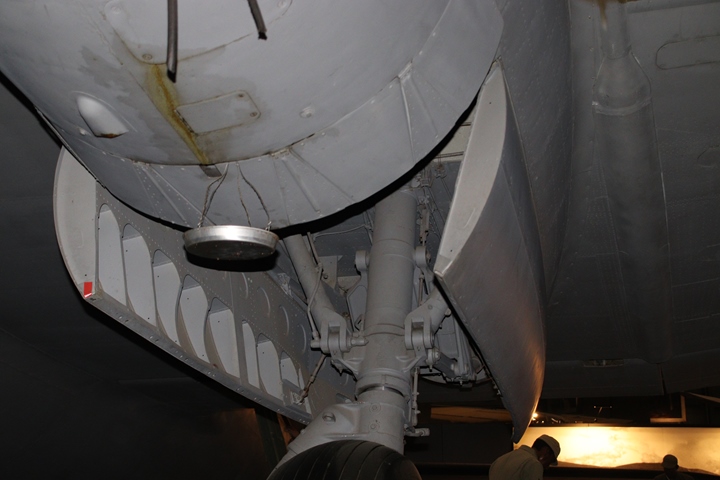
This photo of the port C-46 landing gear
shows the strut up inside of the landing gear doors. Author's
photo.
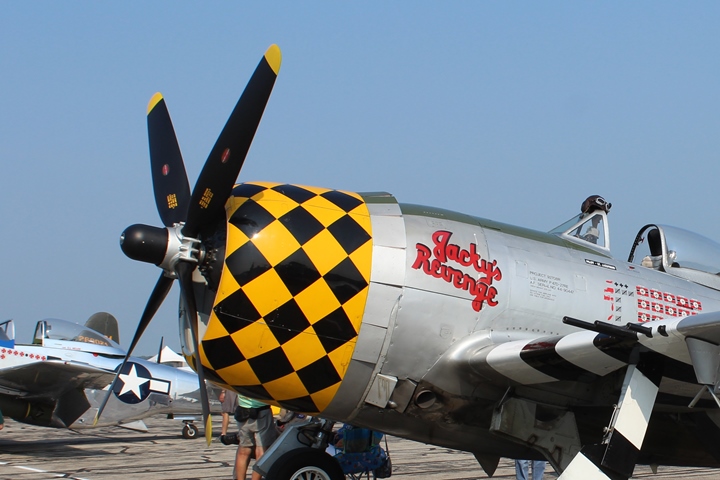
The Harrison Works produced
cowl rings for the P-47. These opened and closed to keep the
engine at the proper operating temperature. Author's photo.
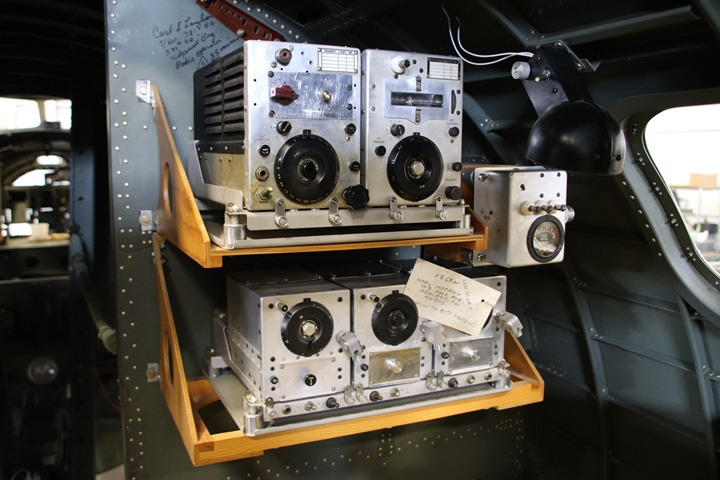
The Harrison Works manufactured 87,000 radio
shock mounts for the Army Air Force like these in the radio room of a
B-17. Author's photo.
Otis-Fensom Elevator Company, Hamilton, ONT
Product Photos:
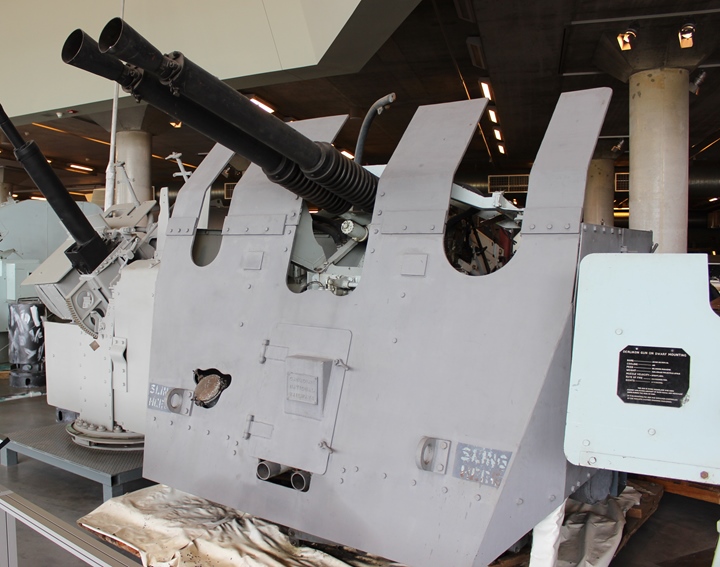
Otis-Fensom built 40mm Bofors twin-mounts
like this one for the Royal and Royal Canadian Navies. Author's
photo.
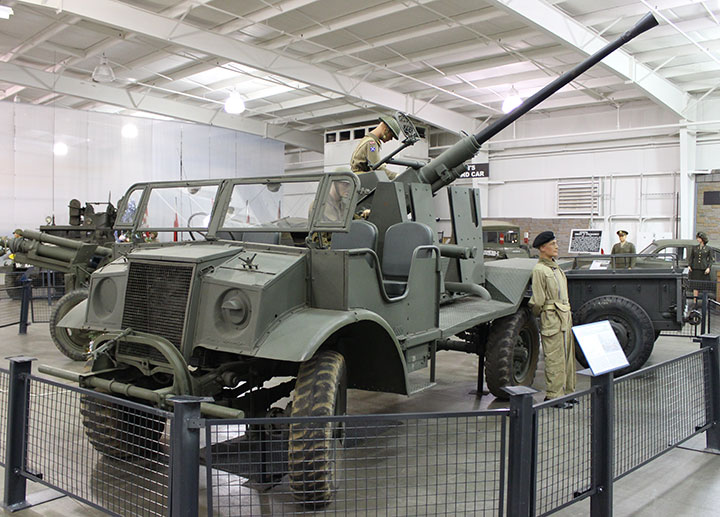
Otis-Fensom also mounted 40mm Bofors on Ford
of Canada Canadian Military Pattern trucks.
Author's photo.
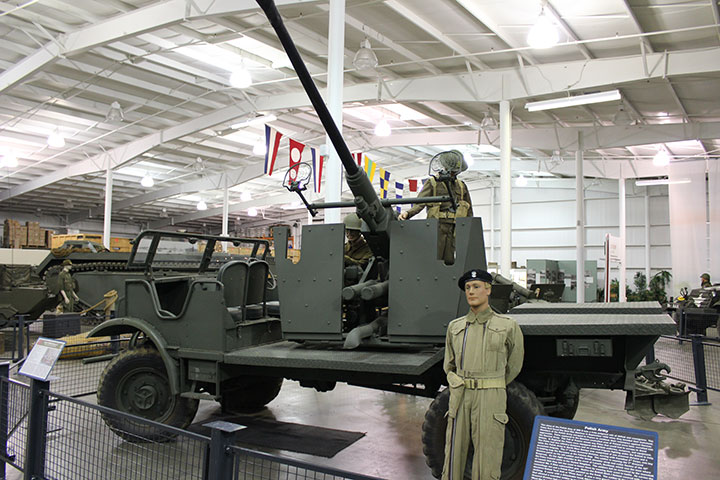
Author's photo.
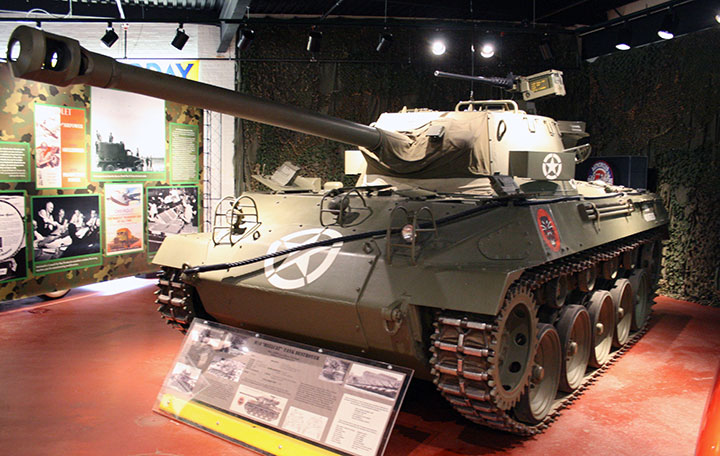
When the 76mm main gun began its use in combat after D-Day in Europe, it
was found by the armored vehicle crews that the weapon's blast created a
lot of dust that obscured the gunner's view for follow-up shots.
The original 76mm main guns did not have muzzle brakes that would help
alleviate this problem. The U.S. Army contracted with Otis-Fensom
in Canada to manufacture muzzle brakes on an expedited basis for
shipment to the battle zone. The Buick-built M18 Hellcat tank
destroyer was one of the weapons with the new 76mm main gun.
Author's photo.
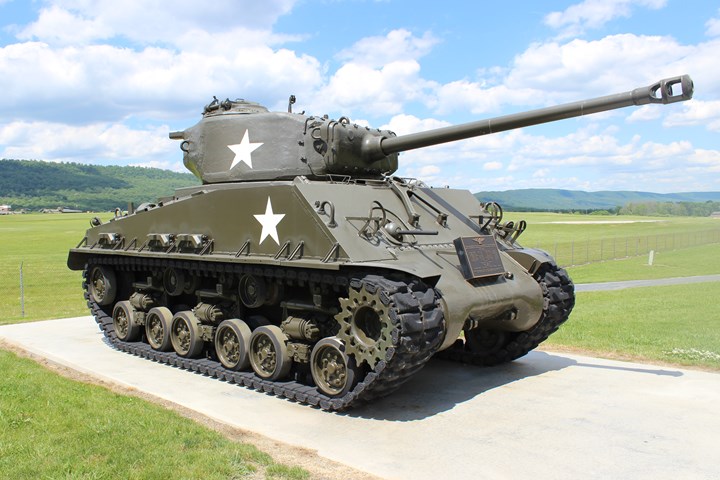
The M4A3 Sherman tanks equipped with the
76mm main gun also required muzzle brakes.
Author's photo.
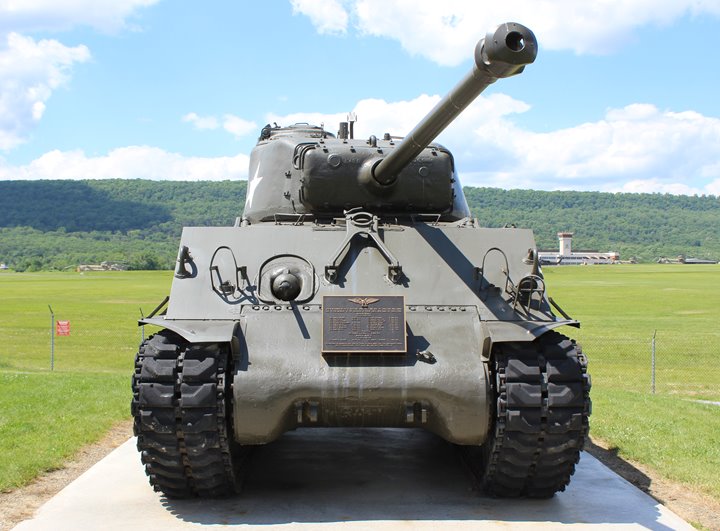
Author's photo.
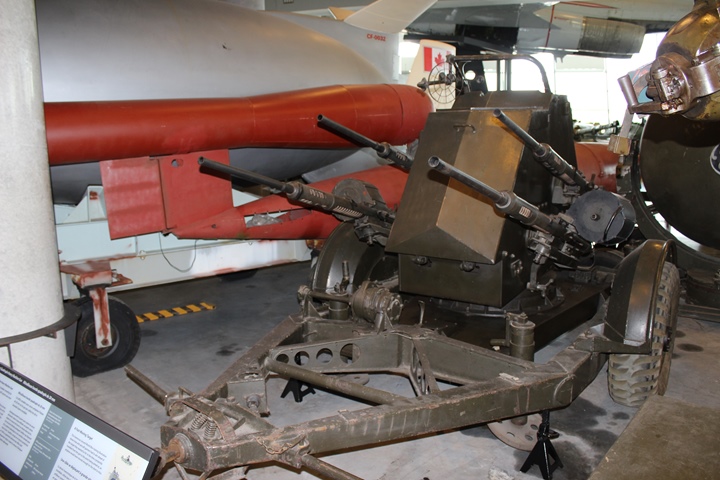
Otis-Fensom also built for the Canadian army
mobile quad 20mm gun mounts on two wheel trailers.
Author's photo.
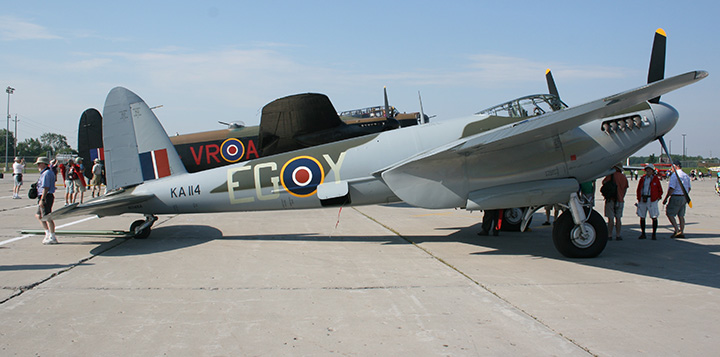
De Havilland Mosquito KA 114 is one of 1,032
of this type built by De Havilland during the Second World War at its Downsview
plant in Toronto, Ontario not far from the Otis-Fensom plant in
Hamilton, ONT. Otis-Fensom built 30mm gun mounts for the aircraft
Author's photo.

Otis-Fensom built tail wheel struts for the
Lancaster bomber.
Author's photo.
|