General Railway Signal Company (GRS) in World War Two
Rochester, NY
1904-1998
This page added 11-9-2022.
In 1904, the General Railway Signal Company (GRS)
was formed by the merger of the Pneumatic Signal Company of Rochester,
NY; Taylor Signal Company of Buffalo, NY; and the Standard Railroad
Signal Company of Arlington, NJ. The company's headquarters and
main production facility was located at 801 West Avenue in Rochester,
NY. At the turn of the 20th Century, railroads were the primary
means of travel within the United States. The Interstate System
and commercial air travel would not replace the railways for travel
within the country until after World War Two. The General Railway
Signal Company was an important contributor to travel safety of the
trains. The company supplied the signal equipment along the tracks
that notified the train engineers that the tracks were safe to use.
For this era, General Railway Signal company was "high tech." Its
signal equipment used the latest electrical technology of lighting,
relays, and batteries to keep the trains running on time and in a safe
manner. This "high tech" image of the company would allow it 38
years later during
World War Two to manufacture some of the most sophisticated equipment to
help win World War Two.
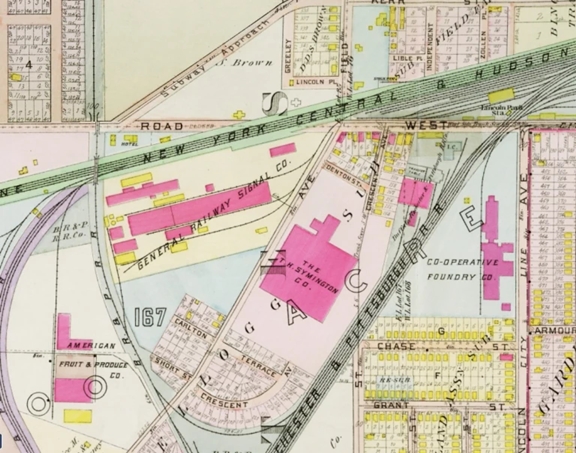
This image from the 1910 City of Rochester
plat map shows the location of the General Railway Signal Company's
factory at 810 West Avenue. The company was at this location until
1993 when operations moved to Brighton, NY, and West Henrietta, NY.
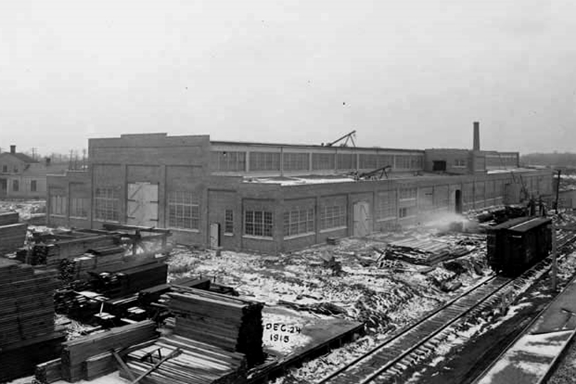
This image shows the plant on a blustery
Christmas Eve Day in 1915. During World War One this plant turned
out artillery shells for the Allied effort. The company would
again make artillery shells when World War Two began.
In 1998, GRS was purchased by Alstom SA, which
discontinued the General Railway Signal Company name on its products.
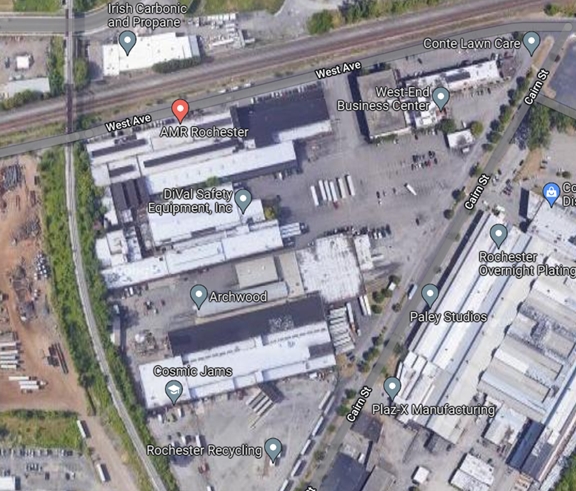
The original plant and additions are still
in current use by other companies.
General Railway Signal Company World War
Two Products:
Table 1 - General Railway Signal
Company's Major World War Two Contracts
The information below
comes from the "Alphabetical Listing of Major War Supply
Contracts, June 1940 through September 1945." This was
published by the Civilian Production Administration,
Industrial Statistics Division. |
Product - Customer |
Contract Amount |
Contract Awarded
|
Completion
Date |
Ammunition
Components - Army Ordnance |
$4,375,000 |
11-1940 |
2-1942 |
Shells - Army
Ordnance |
$4,738,000 |
8-1941 |
6-1942 |
Shells - Army
Ordnance |
$4,335,000 |
12-1941 |
2-1942 |
Shells - Army
Ordnance |
$536,000 |
1-1942 |
11-1942 |
Shells - Army
Ordnance |
$7,232,000 |
2-1942 |
5-1943 |
Shells - Army
Ordnance |
$442,000 |
2-1942 |
11-1942 |
Shells - Army
Ordnance |
$2,365,000 |
3-1942 |
2-1943 |
Shells - Army
Ordnance |
$867,000 |
4-1942 |
12-1942 |
Fire Control
Equipment - USAAF |
$83,193,000 |
8-1942 |
4-1944 |
Shell Assemblies HE M8 - Army Ordnance |
$4,552,000 |
7-1943 |
12-1943 |
Shells 75mm
HE - Army Ordnance |
$368,000 |
8-1943 |
10-1943 |
Signal
Equipment - Treasury |
$4,089,000 |
8-1943 |
2-1944 |
Shells 105mm
HE - Army Ordnance |
$9,049,000 |
9-1943 |
12-1944 |
Fire Control
Equipment - USAAF |
$48,688,000 |
1-1944 |
6-1945 |
Rocket Shells
HE M8A1 - Army Ordnance |
$3,430,000 |
1-1944 |
1-1945 |
Railroad
Signal Equipment - Treasury |
$96,000 |
6-1944 |
8-1944 |
Shells 105mm
HE M1- Army Ordnance |
$8,399,000 |
8-1944 |
5-1945 |
Airplane
Controls - USAAF |
$294,000 |
12-1944 |
4-1945 |
Shells 105mm
HE M1- Army Ordnance |
$5,192,000 |
12-1944 |
4-1946 |
Fire Control
Equipment - USAAF |
$35,926,000 |
2-1945 |
2-1946 |
Total |
$228,166,000 |
|
|
Table 1 shows that the
company's first eight contracts starting in November 1940 through
April 1942 totaled $24,890,000 shells for the U.S. Army. Its
next contract was for a whopping $83,193,000 for fire control
equipment for the United States Army Air Forces. In my
research, I have never seen a company awarded such a large first-time contract for a
new product. Normally, the company gets
a series of smaller contracts as it ramps up production. What
was so important to the winning of World War Two for the United
States Army Air Forces that they would award an $83,193,000 contract
to a company that had only
previously made artillery shells?
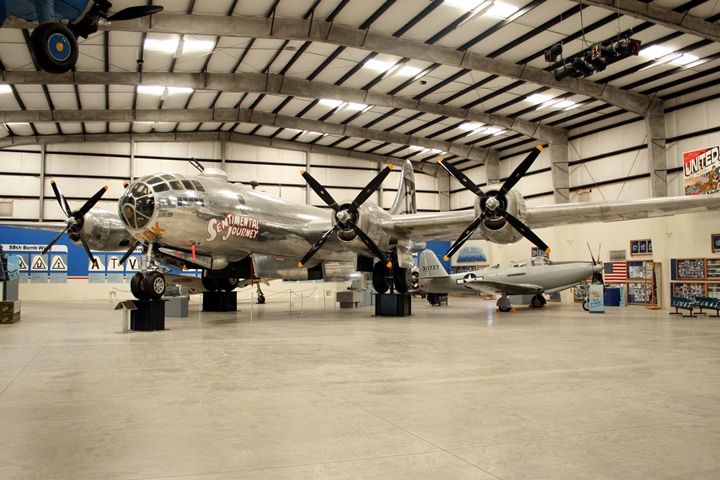
The answer is
the B-29 Superfortress four-engine long
range bomber was the most advanced aircraft of World War Two.
One of the main features of the B-29 was that the crew areas were
pressurized. The big advantage to the crew was that the
interior could be climate controlled, and the air crew was not
subject to having to wear heavy clothing and oxygen masks while
being subject to -40 degree Fahrenheit temperatures like the B-17
and B-24 crews did in Europe. In order to do this, the B-29 had
non-manned gun turrets which were operated by remote gun sights.
The General Railway Signal Company was a major, if not the largest supplier, of the B-29 gun sighting stations for all five locations on
the aircraft. Author's photo from the Pima Air & Space Museum
in Tucson, AZ.
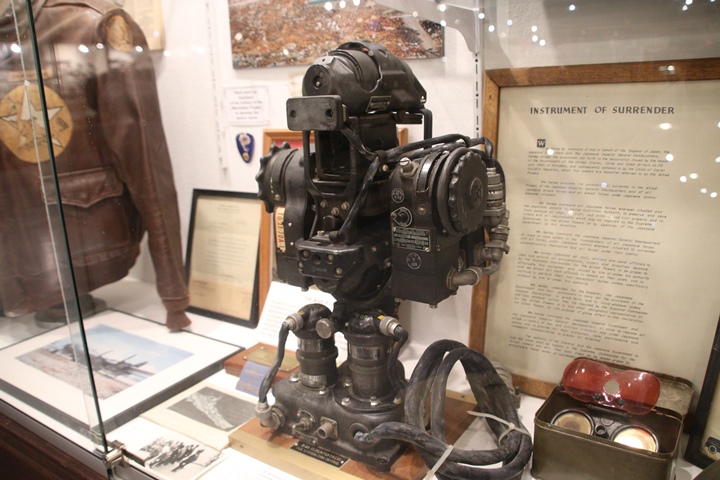
This B-29 General Railway Signal Company
B-29 tail gun sighting station is on display at the Indiana Military
Museum in Vincennes, IN. It is virtually identical to the
other four sighting stations on the B-29. Author's photo.
The B-29 project was the most
expensive American project of World War Two. It was even more
expensive than the Manhattan Project that produced the atomic bomb.
It was also a rushed project where all the new technology had to be
tested and then produced in four plants dedicated to B-29
production. Therefore, in August 1942, GRS was given an
$83,193,000 contract to produce this highly technical product.
Table 2 - General Railway Signal
Company's Major World War Two Product Categories |
Product |
Amount |
Percentage |
Fire Control Equipment
- USAAF |
$167,807,000 |
74% |
Artillery Shells and Rockets |
$55,880,000 |
24% |
Railroad Signal Equipment -
Treasury |
$4,185,000 |
1.9% |
Airplane
Controls - USAAF |
$294,000 |
.1% |
Total |
$228,166,000 |
100% |

This data plate shows this this sighting
station is serial number
312750. It should be noted that the company did not build this
number of units. As noted below, the Singer Manufacturing Company
produced 20,794 computers for the B-29s remote gun control system.
Therefore, GRS most likely produced about the same amount of sighting
stations. Author's photo.
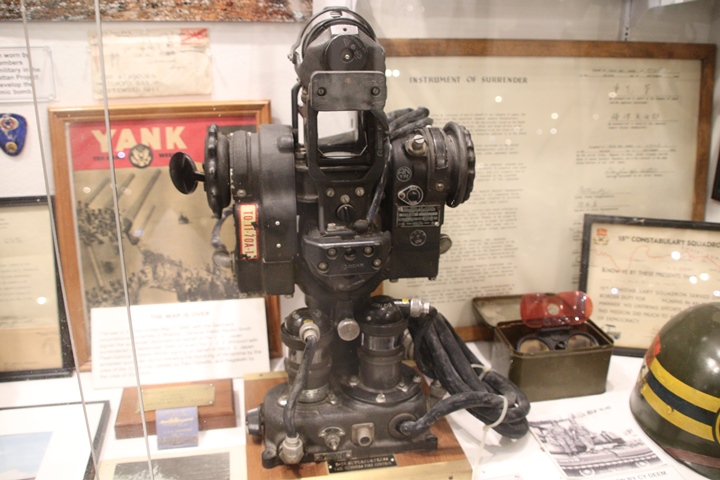
Author's photo.
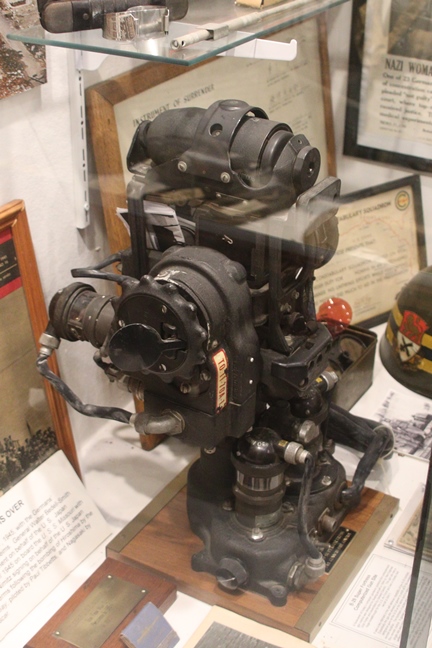
Author's photo.
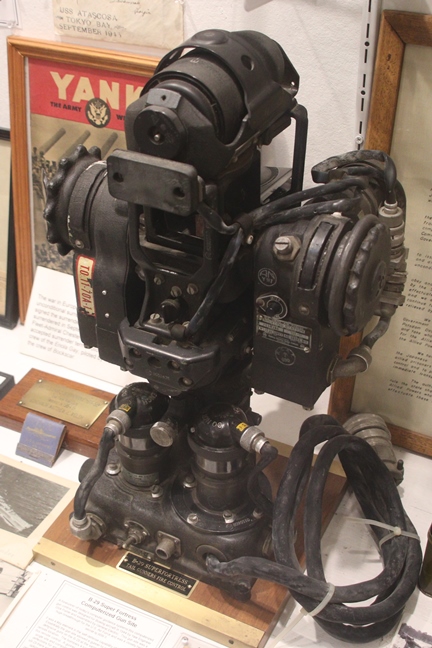
Author's photo.
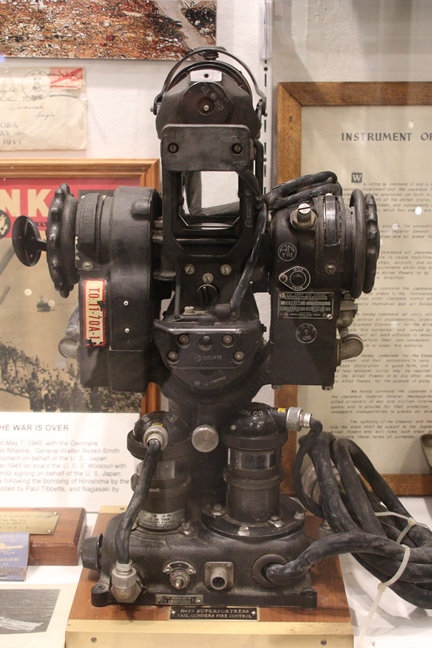
Author's photo.
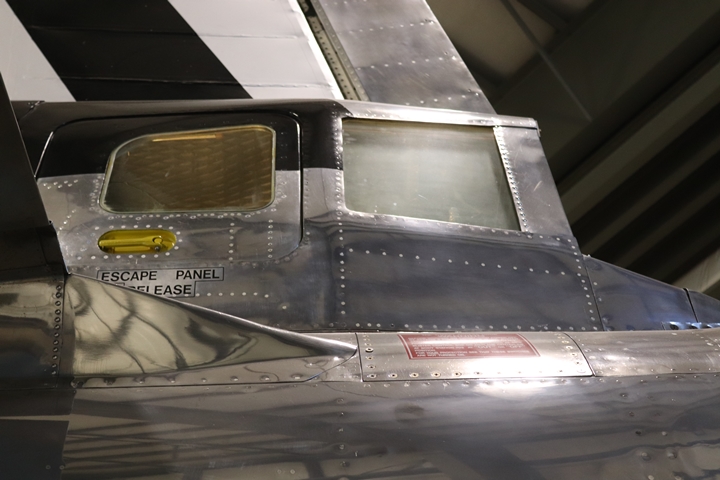
This is the tail gun position on the
B-29. Author's photo.
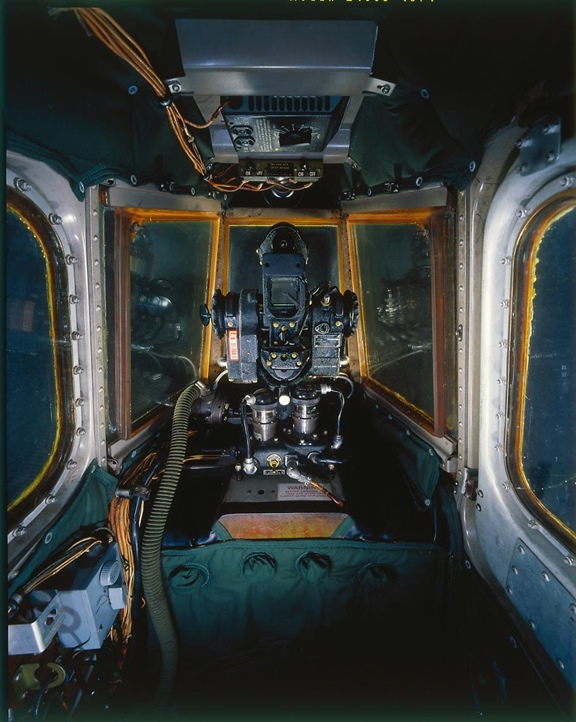
This is the interior view of the B-29's tail
gun position.
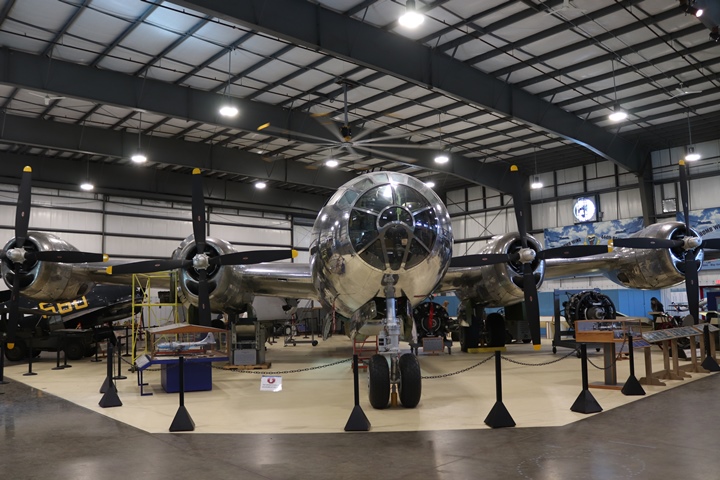
The New England Air Museum in Windsor Locks,
CT built a special display hangar to
display its B-29 named "Jack's Hack." Author's photo.
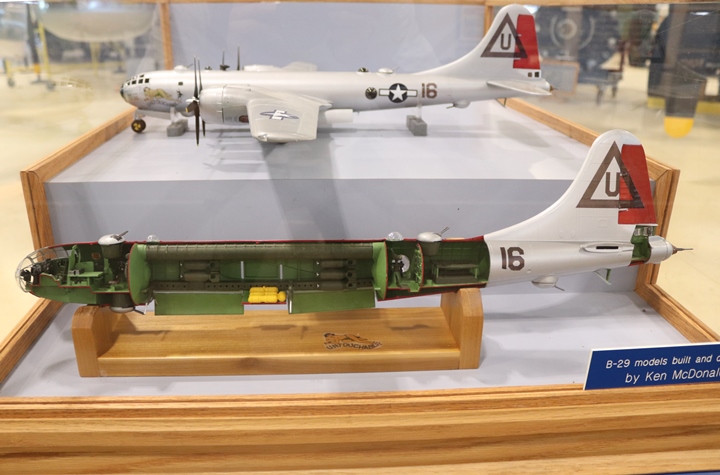
This cut-away model of a B-29 at the New
England Air Museum will be used to explain the defensive gun control
system on the aircraft. Author's photo.
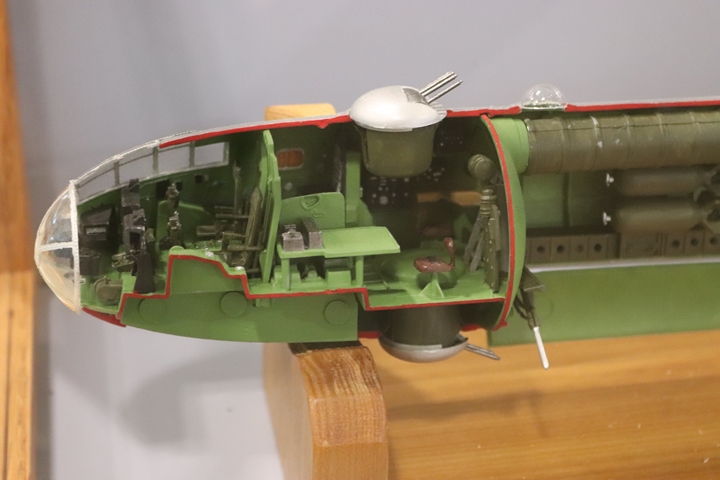
This image shows the front of the aircraft.
The forward dorsal and ventral front turrets can be seen. They are
self-enclosed units with no place for a gunner in the turret. The
bombardier that sat at the front of the aircraft had primary control of
these two turrets. This allowed him to aim both turrets in the
forward position to fire on a Japanese fighter making a head-on attack.
When the aircraft was not being attacked from the front, he could turn
over control of the dorsal turret to the gunner in the top dorsal
sighing position in the rear of the aircraft. Control of the lower
ventral turret could be turned to the port side waist sighting station
gunners. Author's photo.
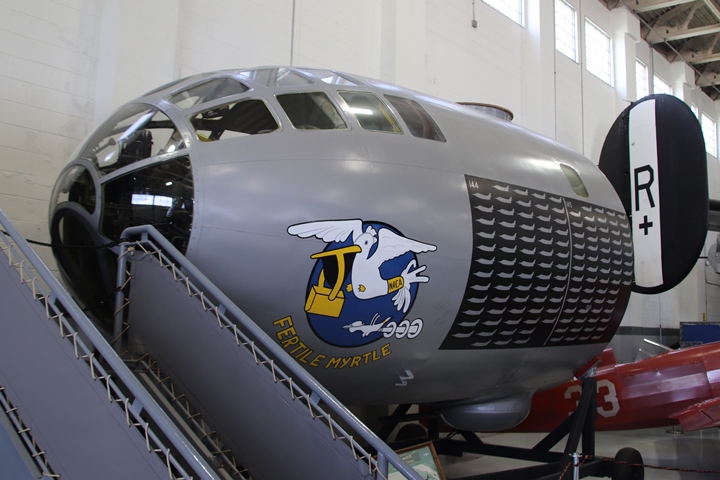
This B-29 front fuselage is on display at
Fantasy of Flight in Polk City, FL. The stairs to the nose section
allows visitors to view the inside of the cockpit area and the
bombardier's sight station. Author's photo.
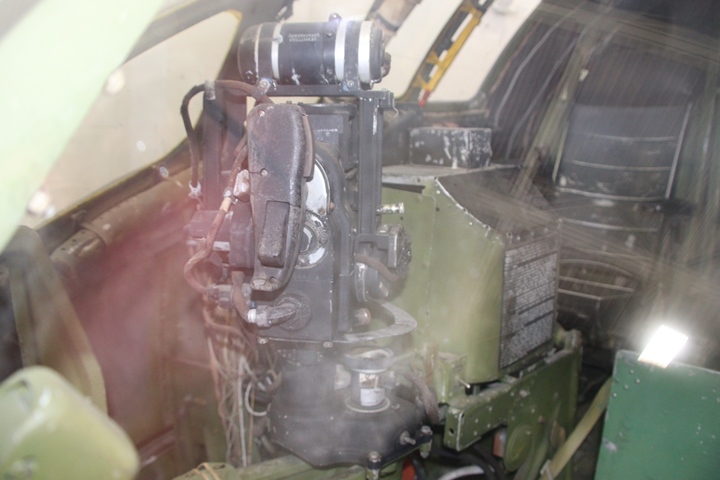
The sighting station is in the foreground.
Some of the parts are missing, such as the GE selsyn generators.
This unit could have been built by either GE or GRS. The data
plate was not visible for identification. However, GRS did build
sight stations for this location. Author's photo.
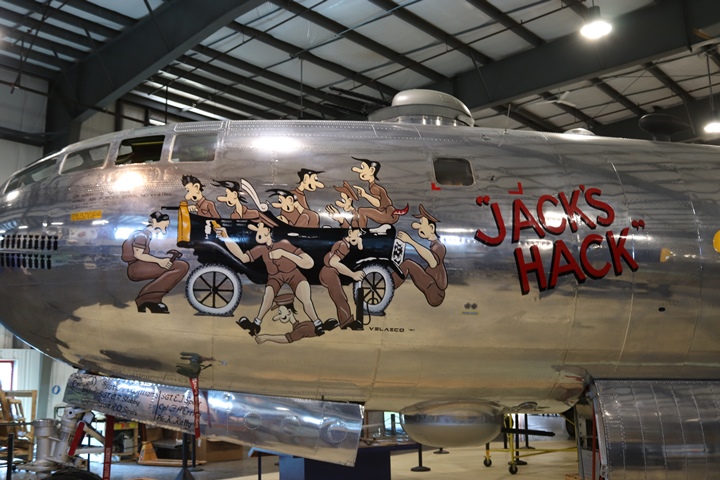
This photo of "Jack's Hack" shows the
forward dorsal and ventral remote controlled turrets. Author's
photo.
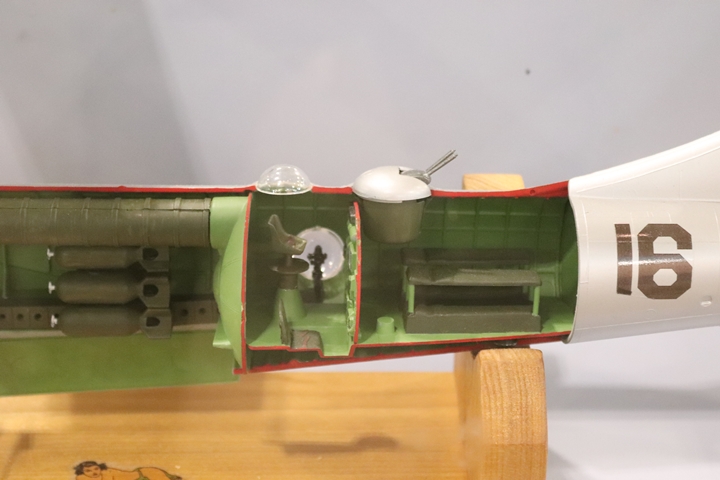
This section of the cut-away shows the rear
gunner's positions. The gunner was located at the top of the
fuselage sat in what was known as the "barber's chair." He was the
overall coordinator of the gunners and was the primary gunner for the
rear dorsal turret. If the aircraft was being attacked from above,
he could use both the dorsal turrets if the bombardier did not have
frontal attacks. The gunners in the side blisters had primary
control over the rear ventral turret which is not in this view. In
an attack from below, they could also control the front lower ventral
turret if the bombardier was not using that turret. The side
blister gunners could also take control from the tail gunner of his
turret if he was not under attack. Author's photo.
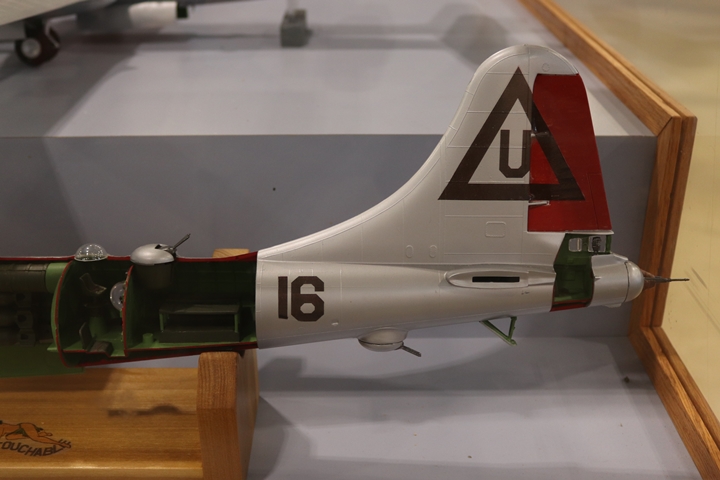
This view shows the rear ventral and tail
turrets. The tail gunner had a primary control of the tail guns,
but could turn control of the tail turret to the side blister gunners.
Author's photo.
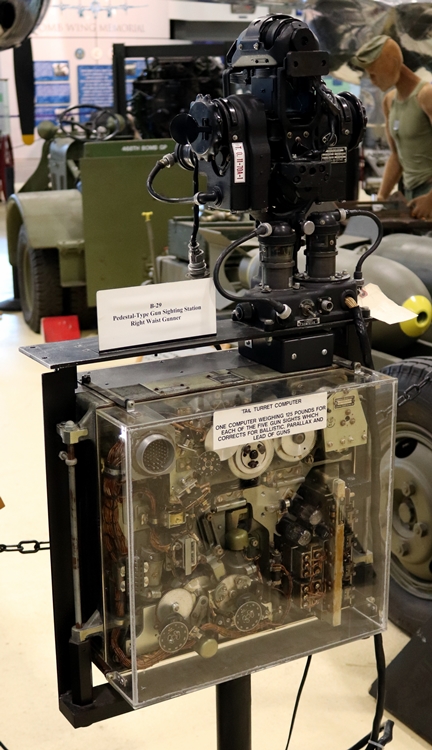
This display is also at the New England Air
Museum. The upper portion is a right waist gunner's sighting
station. This particular example was built by General Electric, but
General Railway Signal Company also built them. Author's photo.
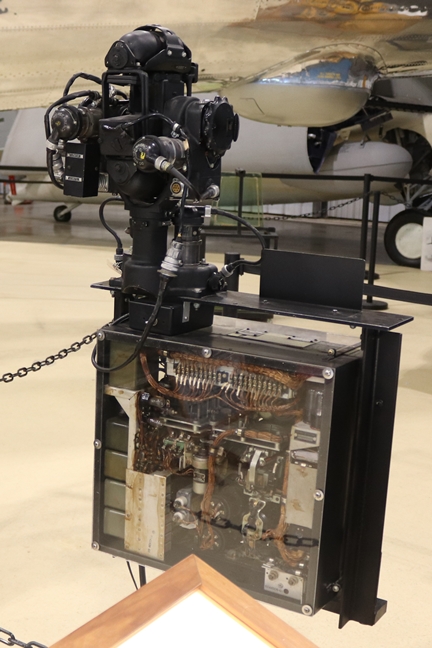
The item on the bottom is the computer for
the tail gun turret. The B-29 was the first aircraft which had a
computer controlled defensive gun system. Author's photo.
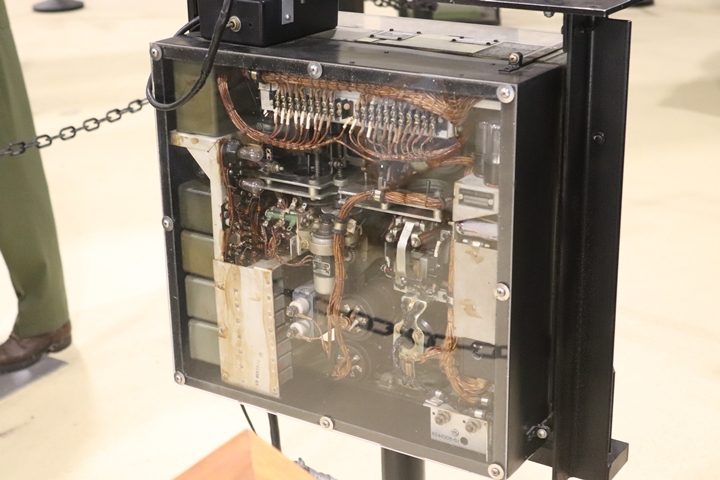
The B-29's gun turrets were all computer
controlled and there were a total of five computers on board, one for
each sighting station on the aircraft. General Electric licensed
production of the computers to the Singer Manufacturing Company which
built a total 20,794. Author's photo.
The computer was of the analog electrical
type. Each one was located under the floor near the gun station it
controlled. When in use, the gunner used his General Railway Signal
Company-built sighting station to input the wingspan of the attacking
aircraft and the motion of the enemy aircraft as the gunner tracked it
across the sky. The gunner also framed the target which gave the
computer the distance to the enemy fighter. The navigator was also
responsible for providing needed information that the computer needed to
operate properly. These inputs were indicated air speed, pressure,
outside air temperature, and altitude. The computer also knew the
ballistics of the .50 caliber ammunition that the B-29s used. The
computer took in all these inputs, calculated, a firing solution
and aimed the remote turret or turrets at the proper position to lead
the enemy aircraft.
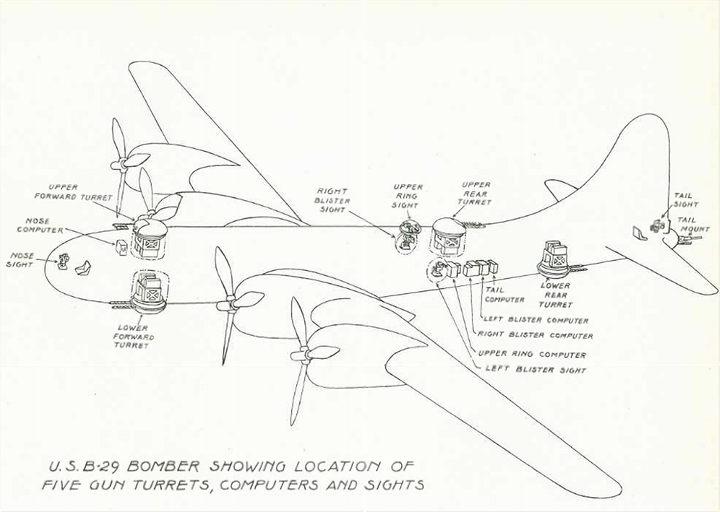
This image shows remote turrets, gun sight
stations, and the location of the computers.
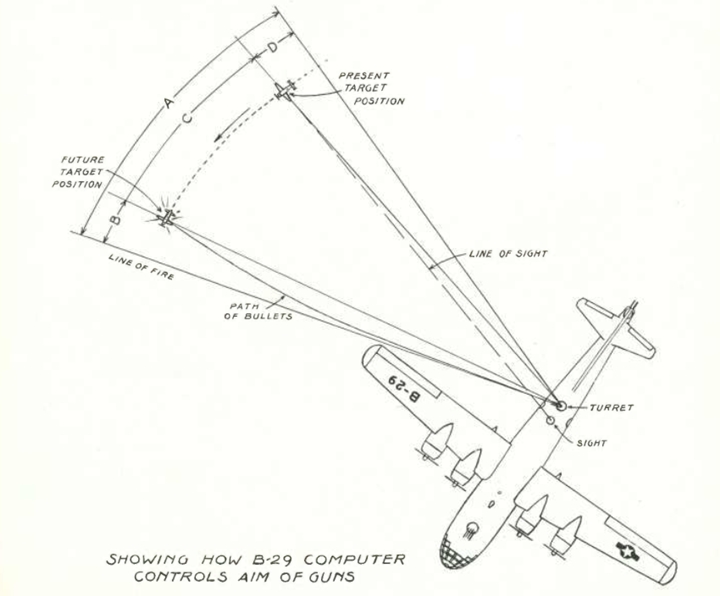
This image shows the final result of the firing
solution. The computer also needs to calculate the parallax
between the gunner's sight and the remote turret location. The
computer uses all of the inputs to determine the proper lead on the
aircraft. This was an extremely sophisticated system for the era.
The General Railway Signal Company-built sighting stations were the
gunner's tool to provide the proper information to the computer to shoot
down enemy aircraft and protect the bomber.
The effective range of the system was 900
yards, which was 50% better than on the manual systems for the B-17 and
B-24. Over the course of 31,000 sorties between August 1944 and
August 1945, B-29 gunners were credited with shooting down 914 Japanese
fighters.
Artillery Shells and Rockets:
Ordnance items were 24% of the company's business during World War Two.
The $55,880,000 worth of two sizes of shells and one type of
rocket shell that GRS built was a significant amount for any company during the war.
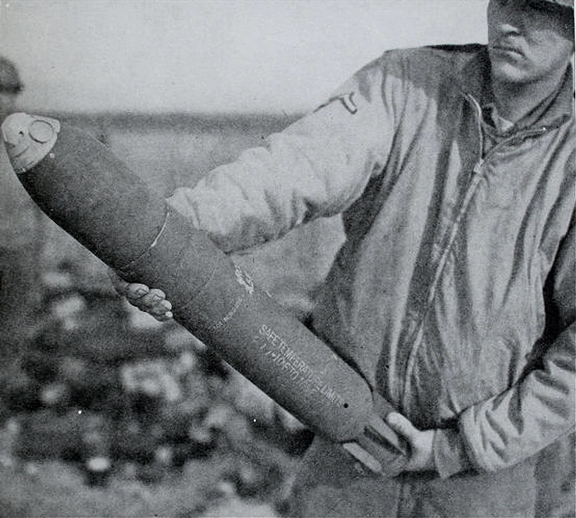
This is an M8 4.5 inch rocket that was used
by both U.S. Army air and ground forces during World War Two.
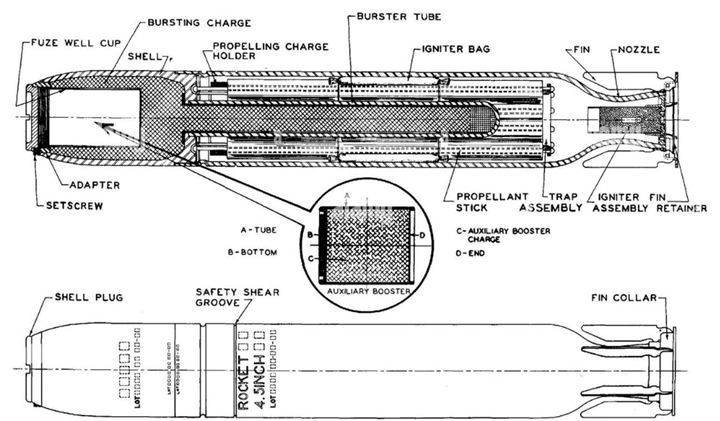
From the description of the contract stating
the company built "Rocket Shells," it may be that GRS just manufactured
the component labeled as "shell" in the diagram. This was
similar to the artillery shells the company was making. A
munitions plant would have been responsible for assembling all of the
components and hazardous explosives.
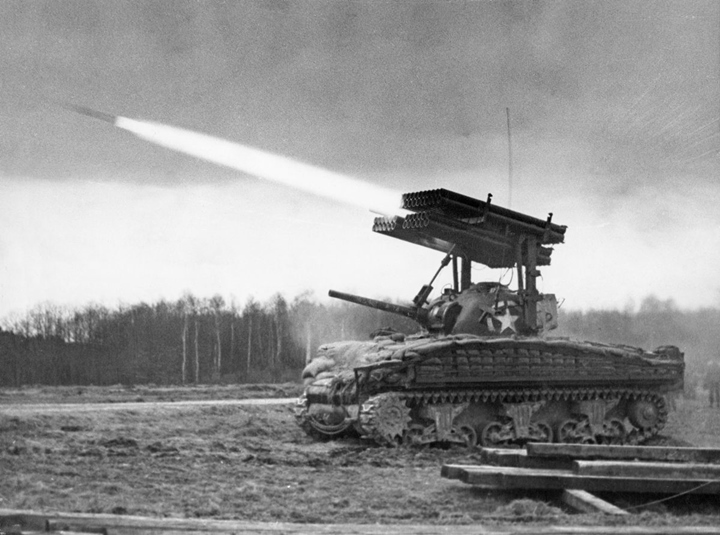
The best known use of the 4.5 inch rocket
was launching them from Sherman tanks. This is an actual
combat photo as the Sherman tank crew has added sandbags to the exterior
of the tank for added protection against German anti-tank weapons.
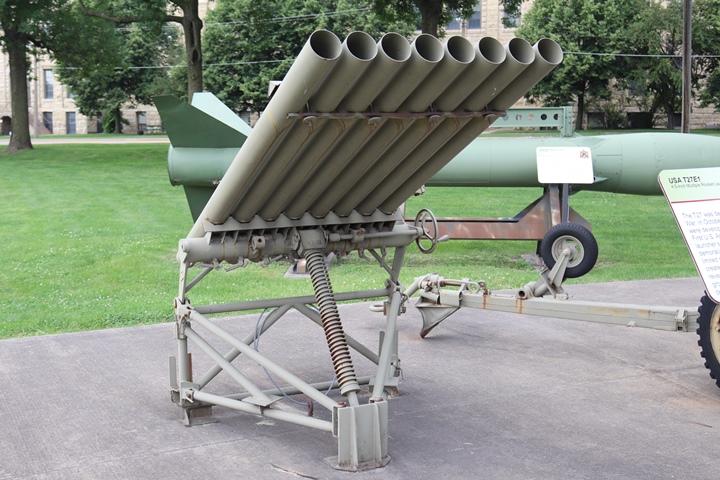
Another launcher was the
T27E1 4.5 inch rocket launcher used by ground troops. This weapon
is on display at the Rock Island Arsenal outside display area.
Author's photo.
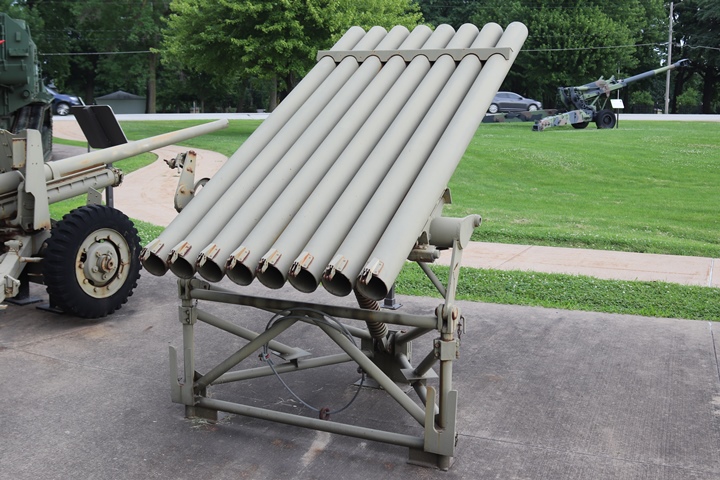
Author's photo.
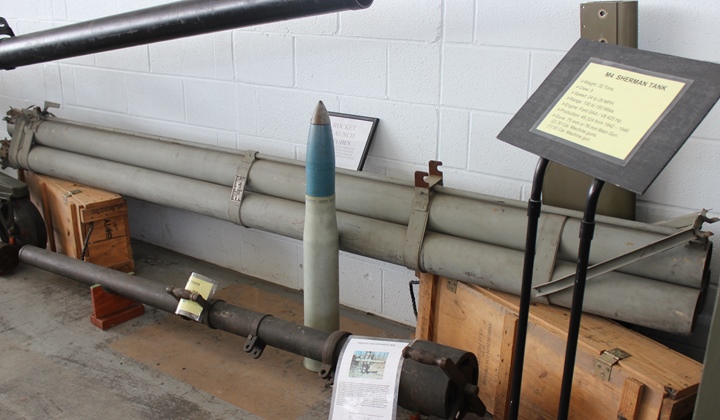
Of interest in the photo are the three
tubes. These make up a 4.5 inch rocket launcher used by the U.S. Army
Air Forces during World War Two. It is on
display at the MAPS Air Museum at the Akron-Canton Airport, OH.
Author's photo.
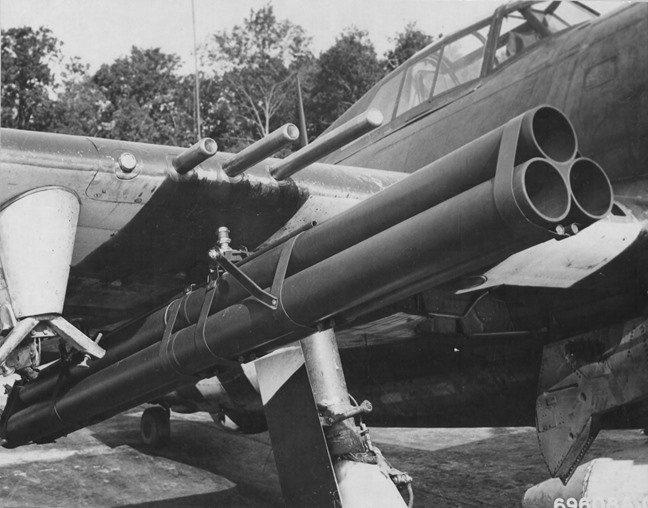
This image shows the rocket launchers
mounted to a P-47 Thunderbolt fighter.
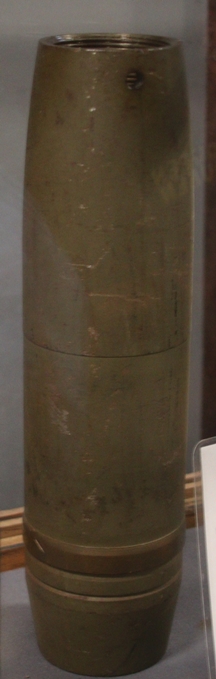
This is a 75mm high explosive shell similar
to what GRS manufactured. Author's photo from the Museum of the
Soldier in Portland, IN.
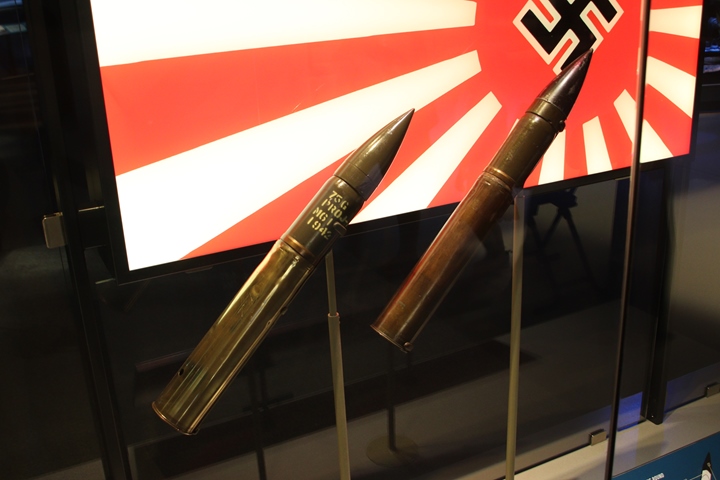
The shell would then be assembled into
complete units similar to these by a munitions plant. These are on
display at the National Museum of the United States Army at Fort
Belvoir, VA. Author's photo.
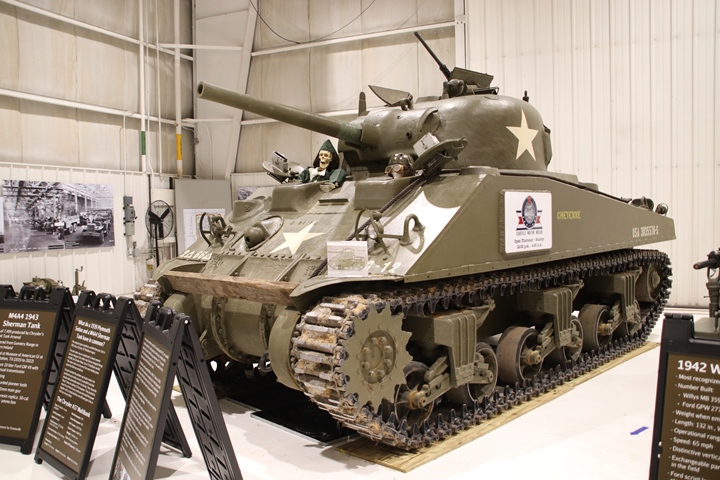
The most common use for the 75MM high
explosive shell was in Sherman tanks when they were used in the
infantry support role. High explosive shells were used to destroy
enemy bunkers and fortifications so that the infantry could advance
beyond them. About 75% of the 75mm shells carried in Sherman tanks
were high explosive types. This Chrysler-built M4A4(75)VVSS is on
display at the Evansville Wartime Museum in Evansville, IN.
Author's photo.
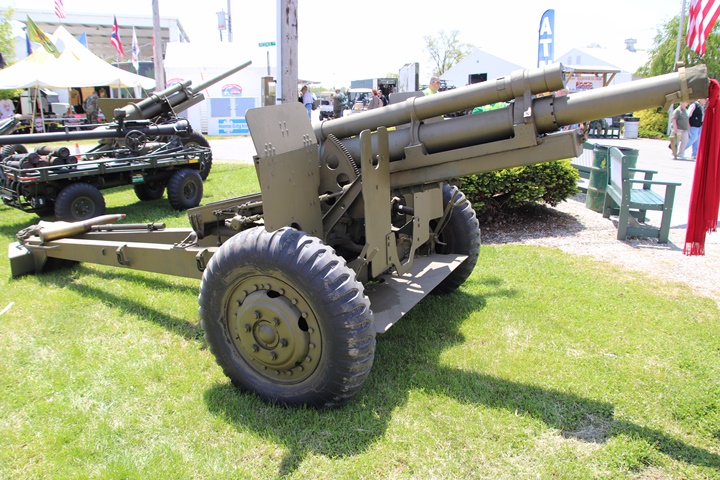
The 105mm howitzer was the most utilized
piece of artillery used by the U.S. Army and U.S. Marine Corps during
World War Two. This 105mm howitzer was on display at the 2021 MVPA
display at Findlay, OH. Author's photo.
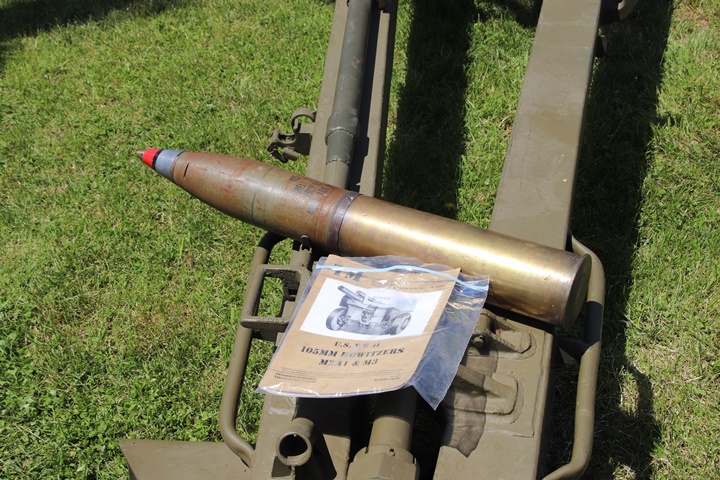
General Railway Signal Company was an
important supplier of the high explosive shell for the 105mm howitzer.
Author's photo.
|