The B-29
and the US Auto Industry in World War Two
This page added 6-15-2016.
The B-29 project was the largest and most
expensive project undertaken during World War Two. It was even
more expensive than the Manhattan Project. The American Automobile
Industry was instrumental in supplying airframe components and engines
for the B-29. Below are the automobile companies and their
suppliers known to have participated in the building of the most complex
aircraft to date.
The US Auto Industry's involvement in the B-29
was immense yet has been unheralded and forgotten. The auto
industry supplied everything from bearings for the remote control gun
systems to the major fuselage and wing components, and engines.
Boeing's initial work on the concept of a
long range bomber started with the February 5, 1940 receipt of
specification "R-40B" from the
U.S. Army Material Command at Wright Field in Dayton, OH. The specification was
written for a
long range four engine bomber with a range of 5,333 miles with the speed
and bomb load of a B-17. Boeing had been expecting the proposal,
and had been working on several conceptual bomber
models starting in 1939. The Model 341, which Boeing felt met the
requirements, was submitted in March 1940.
In late March the Army Air Corps
realized that the requirements needed to be changed. A supplementary
specification went to Boeing which included more bomb capacity, leak
proof fuel tanks, and more defensive armament. Due to these
requirements, the Model 341 evolved into the Model 345. The Model
345 added seventeen more feet of wing span than the Model 341 and was
eight feet longer. Each Wright radial engines had 200 more
horsepower at take-off than the engines designated for the Model
341. The Model 345 would have a maximum bomb load of 16,000
pounds, a crew of twelve, four remote controlled turrets, a rear
turret, and a maximum speed of 382 MPH at 25,000 feet. This was then
designated the XB-29.
As with all military designs, weight of the
B-29 went up over time with the addition of new requirements by the
military. The final B-29
design had grown to an aircraft with a design gross weight of 105,000
pounds, while the XB-29's design gross weight was 100,000 pounds, the
Model 345 was 97,700 pounds, and the Model 341 76,000 pounds. The
added requirements caused the weight to increase by 29,000 pounds over three years, while
the airframe and engines remained constant since the Model 345.
When it came time for production of the
B-29 in 1943, the US Auto Industry was deeply involved as suppliers of
airframe components, engines, and many of the internal components of the
aircraft. General Motor had seventeen of its divisions providing
parts and structural components. They were: AC Sparkplug,
Allison, Brown-Lipe-Chapin, Buick, Chevrolet, Delco Appliance, Delco
Products, Delco Radio, Delco-Remy, Fisher Body, Frigidaire, Harrison
Radiator, Hyatt Bearings, Moraine Products, New Departure, Packard
Electric, and Rochester Products. Chrysler's DeSoto, Dodge, and
Plymouth divisions contributed heavily to the B-29 project. Hudson
was the third automaker to supply B-29 components. Auto suppliers
contributing to the construction of the B-29 were Briggs Manufacturing,
Firestone, Goodyear, Goodrich, and Libby-Owens Ford.
The US Auto Industry and the B-29 "Enola
Gay": The first three Silverplate nuclear bombers were
built at the Boeing Wichita, KS plant. The "Enola Gay" and the of
remaining 43 Silverplate nuclear bombers were all built at the Martin
Omaha, NE B-29 plant. All were modified for the nuclear mission at
Martin Omaha.
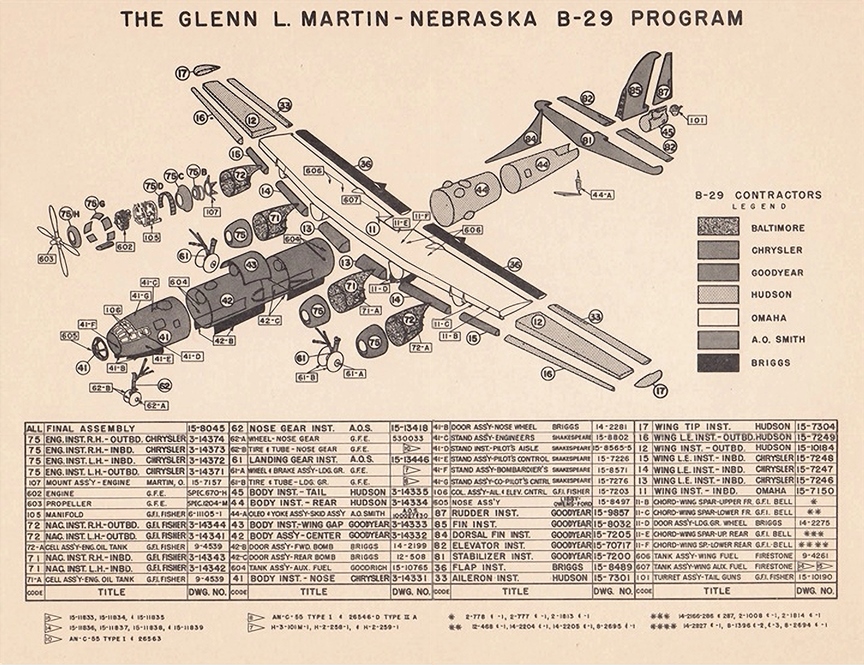
As the Martin information from World War Two shows,
the US auto industry was the major supplier of airframe and structural
components to Omaha.
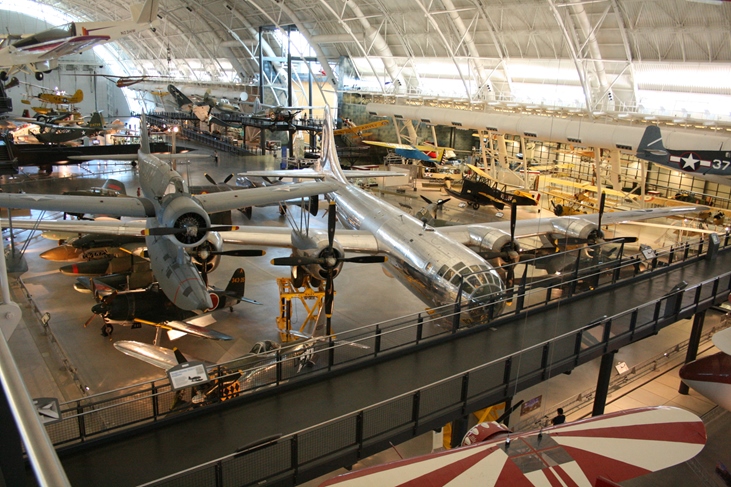
The B-29 "Enola Gay" is currently on display
at the Steven F. Udvar-Hazy Center of the National Air and Space Museum
at the Dulles International Airport in Virginia. Author's photo.
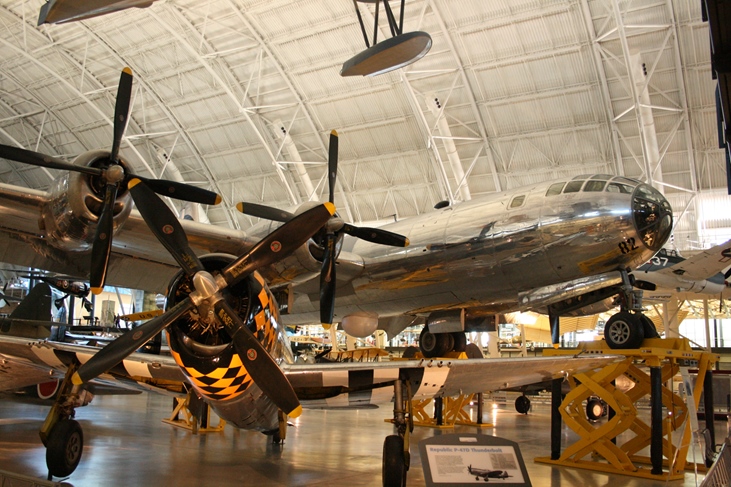
Author's photo.
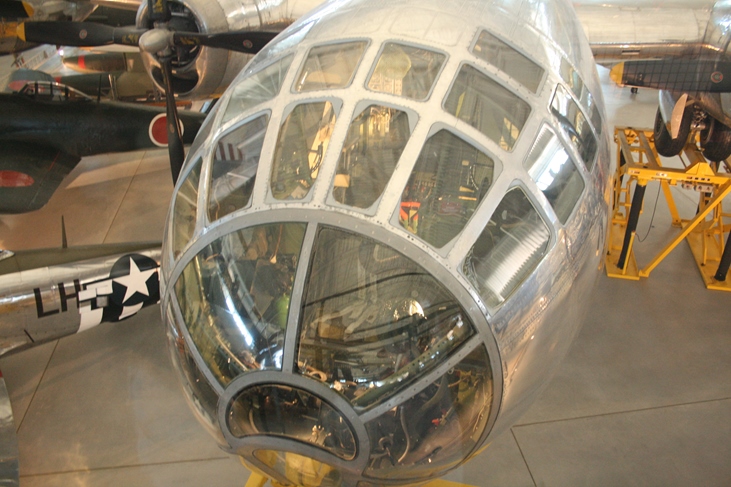
The bombardier's front Plexiglas nose
section was built by Libby-Owens-Ford, a prime supplier of glass to the
US auto industry. The front eighteen foot fuselage section was
built by Chrysler's DeSoto Division on Warren Avenue in Detroit.
Author's photo.
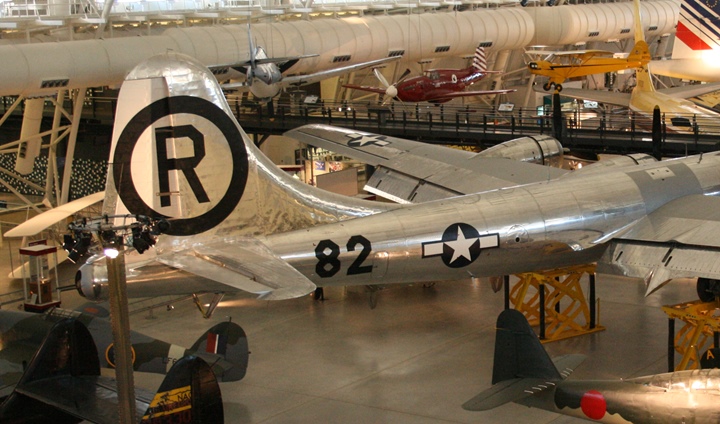
The Fisher Body Plant # 1 in Cleveland, OH
built the rear turret and gun assembly. Goodyear built the rudder,
the vertical stabilizer and the leading edge to the vertical stabilizer.
It also built the horizontal stabilizer and elevators on the "Enola
Gay". Goodyear had aviation plans in Akron, OH and
Goodyear, AZ. The three rear fuselage sections behind the
wings, to include the tail gunner's location, were built the Hudson Motor
Car Company in Detroit. Author's photo.
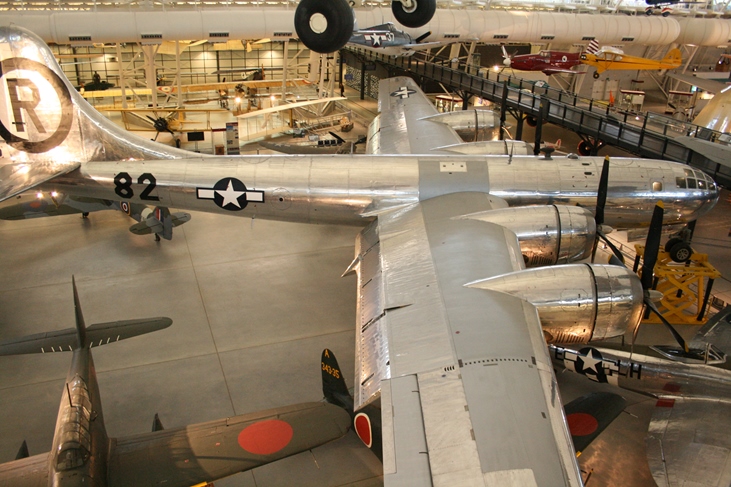
Goodyear produced the two bomb bay fuselage
sections. Chrysler furnished the engine cowlings and the leading
edge sections for the wing center section. Fisher Body Cleveland
#1 or Fisher Body Lansing built the engine nacelles and inside the
nacelles the Fisher Body furnished the engine exhaust manifolds and the
engine oil tanks. Hudson provided the ailerons, outer wing
sections, outer wing leading edges and wing tips. Briggs supplied the flaps
and bomb bay doors. Inside the wings were four Firestone
fuel tanks. The engines are shown as Government Furnished
Equipment. Dodge in Chicago produced Wright R-3350 engines.
Author's photo.
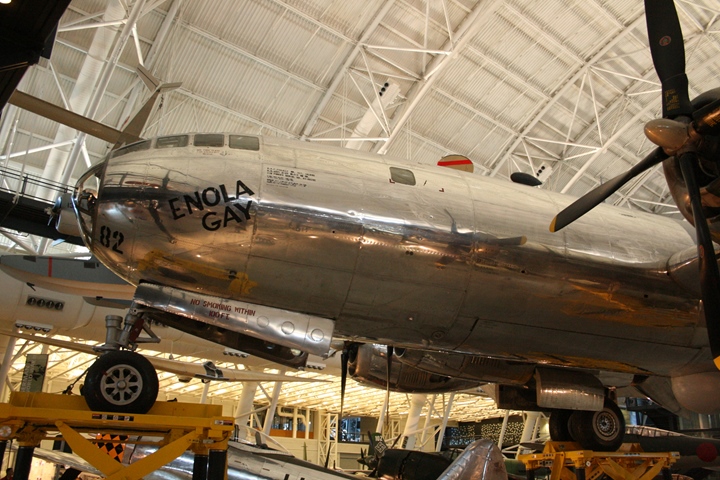
The name "Enola Gay" is written on the
Chrysler DeSoto Division built nose fuselage section. The eighteen
foot long section parting line can be seen about two feet behind the
square window. Chrysler workers installed 50,000 rivets, four miles of wiring and
8,000 different types of parts in the nose section. Behind the nose section are two
Goodyear built bomb bay fuselage sections. On normal B-29s built
there was provision for a Goodrich built auxiliary fuel tank in the rear
bomb bay. For the nose gear and main landing gears the doors were
produced by Goodrich. Author's photo.
Because modifications were made to the
Silverplate B-29s, several of components supplied by the American auto
industry were not included. The bomb bay doors were modified to
accept the large atomic weapons. The bomb bay doors normally
supplied to Omaha B-29s were not used or were modified. It is
unknown. Also, the Silverplate aircraft used
Curtiss reversible electric propellers, and not the normal Hamilton
Standard propeller built by Frigidaire Division of GM .
Nose Section: The photos below
are of the interior of the nose section from B-29A 44-62139 at the
National Museum of the Air Force in Dayton, OH. This A model nose
section is representative of all nose sections built. Most likely
this one was built at the Boeing Renton, WA plant. B-29s built in
Marietta, GA by Bell and Boeing in Wichita, KS had Chrysler built
nose fuselage sections. The photos below show some of the 50,000
rivets, 8,000 parts and four miles of wiring. All of the displays
are behind Plexiglas.
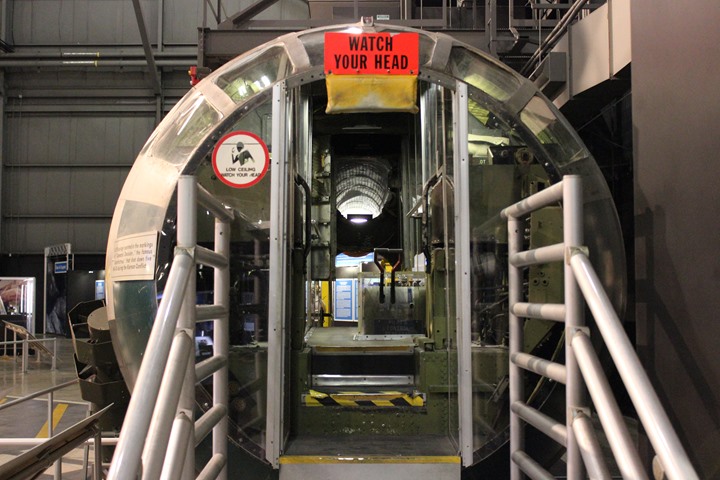
Author's photo.
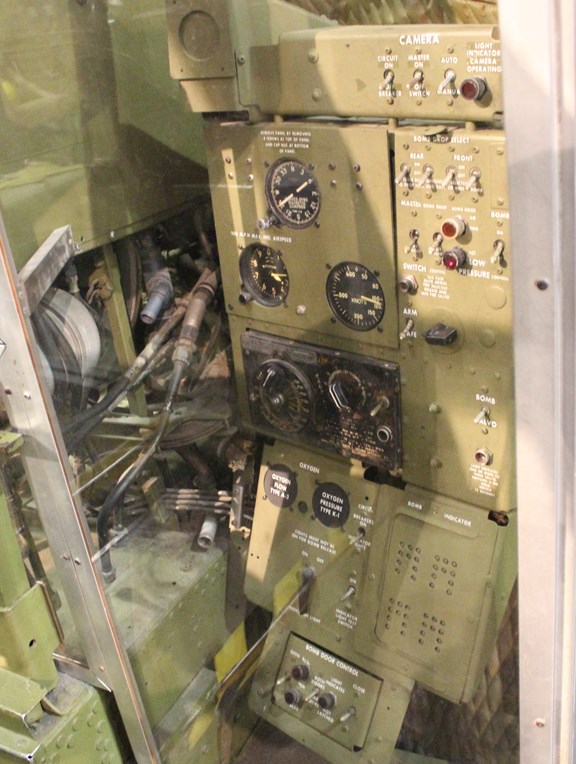
The left or port side of the bombardier's
station. Author's photo.
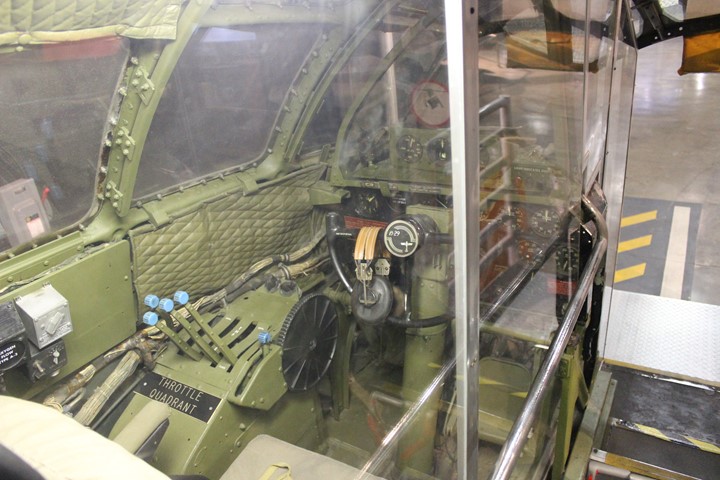
The pilot's station. Author's photo.
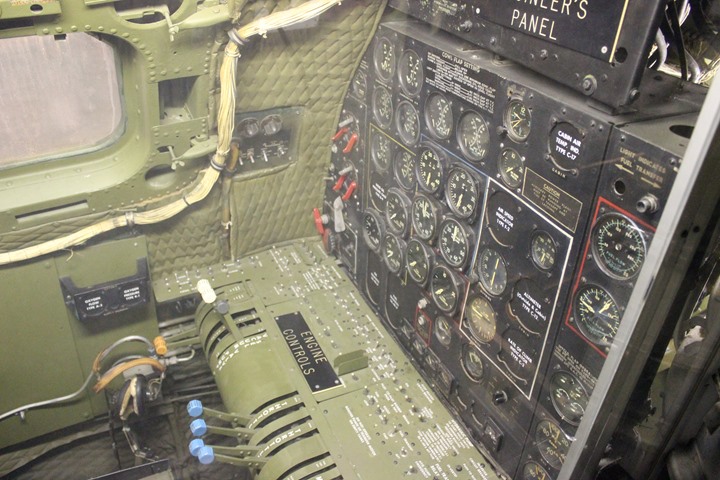
The flight engineer's station.
Author's photo.
Factory Photos:
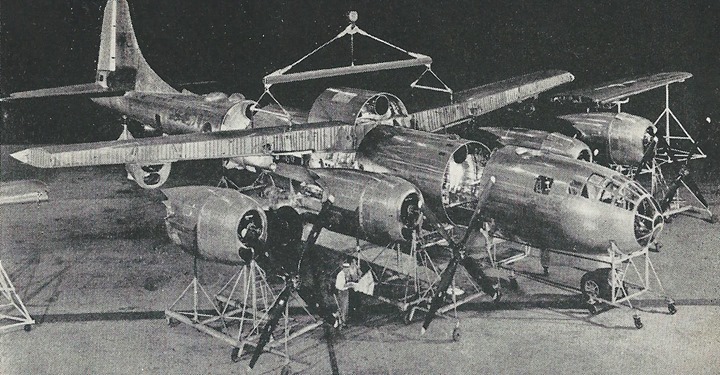
This photo is an exploded view of an actual
B-29, showing many of the main components. The Chrysler DeSoto
nose section is separated from the Goodyear built bomb bay fuselage
sections. The Hudson built rear fuselage sections with the
Goodyear vertical and horizontal tail and control surfaces can be seen.
The main wing center section was built by Martin Omaha but the outer
wing section components built by Hudson are visible. The Fisher
Body engine nacelles have Chrysler built engine cowlings attached.
Frigidaire props are off the Dodge built engines.
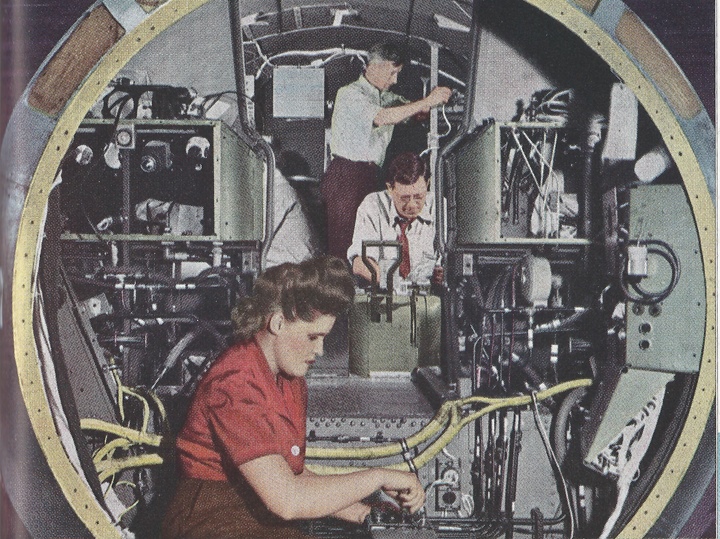
There was more to just stamping out the
aluminum sheet metal pieces and then riveting them together with 50,000
rivets to make the fuselage. DeSoto-Warren assembled all of the
interior of the B-29 nose section, which included four of the eight
miles of wiring in the B-29. The workers shown above are installing
some of the 8,000 parts that went into the construction of the
Superfortress fuselage. The B-29 was the first insulated and
soundproofed bomber and the insulation can be seen in this photo The
fuselage sections were shipped via rail to Omaha using oversized
boxcars, which were foot wider and one and a half foot taller than the
normal boxcar of the period.

Working on B-29 engine cowlings at the
DeSoto Warren Plant in Detroit.
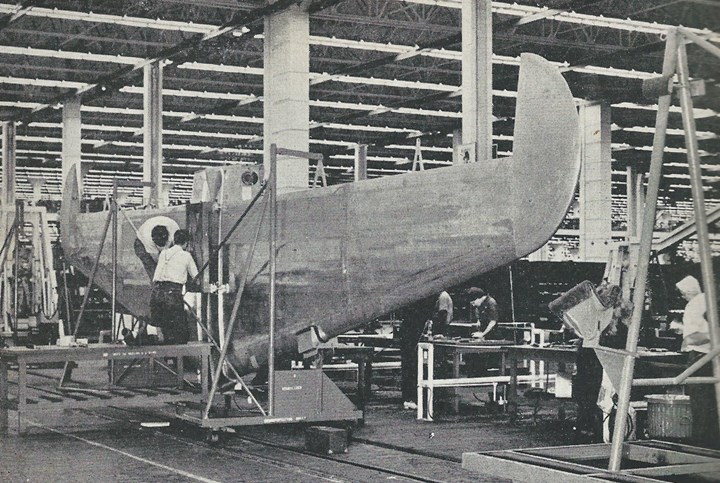
This is the Fisher Body Cleveland plant #2
making horizontal stabilizers. Fisher Body either made them along with
Goodyear, or was a sub-contractor to Goodyear for these particular B-29
components.
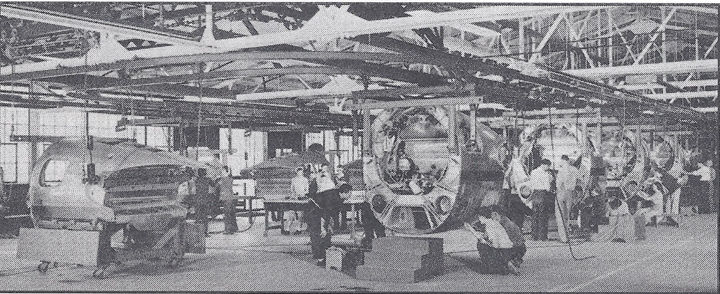
B-29 engine nacelles on the assembly line at
Lansing Fisher Body. My mother worked in this plant during World
War Two. Photo courtesy of UAW Local 602.
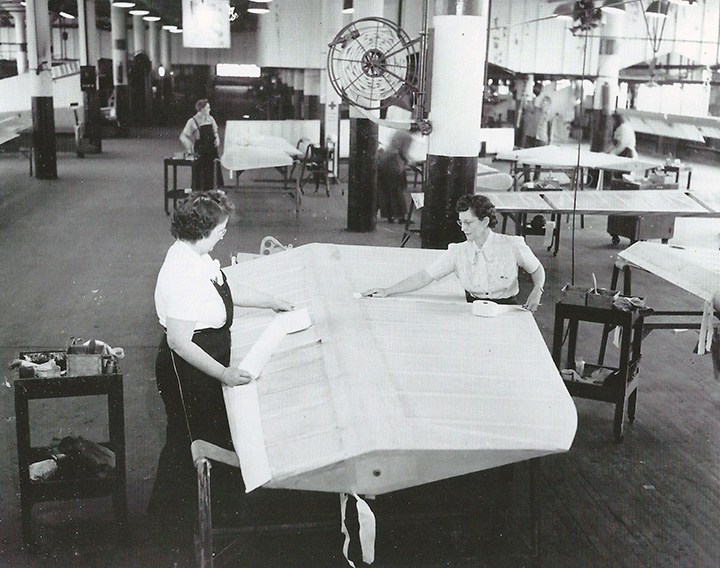
These women are working on a B-29 fabric covered rudder on the Lansing
Fisher Body plant floor. The woman on the left is applying tape
over the stitching that holds the fabric to the aluminum superstructure.
The stitching down the center has already been taped over. Once
this process is complete, a water-proof varnish is applied and then
cured.
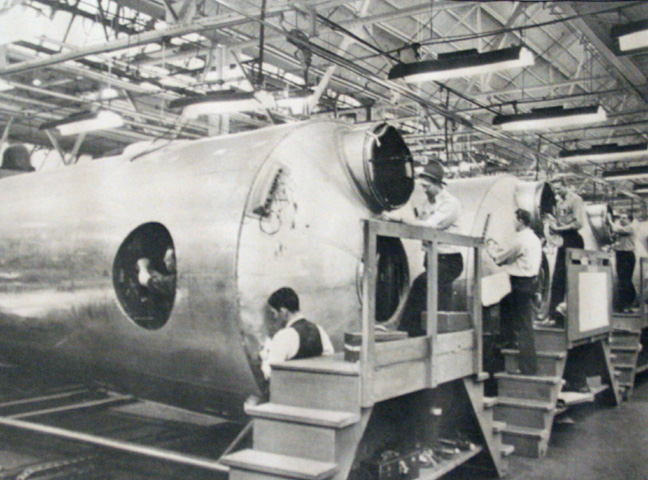
Hudson workers building B-29 rear fuselage
sections.
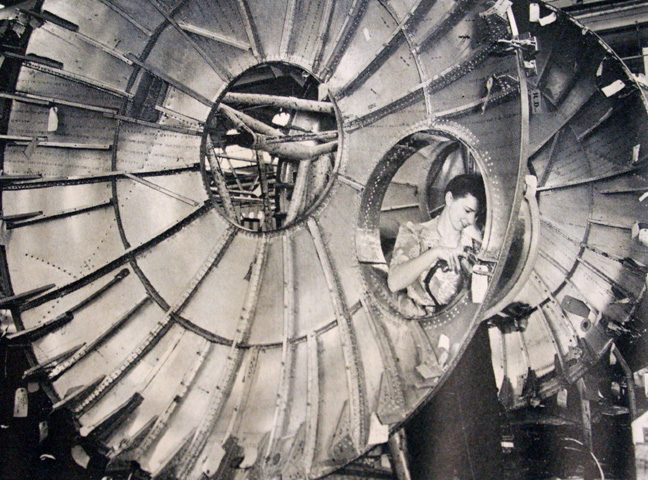
B-29 rear fuselage end caps under
construction at the Hudson plant.
B-29 Components
built by the US Automobile Industry in World War Two |
Manufacturer |
B-29 Components |
Location |
Comments |
|
Briggs Manufacturing |
Aft bomb doors and
forward bomb doors, nose wheel doors, and outer wings. |
31,000 employees in
ten Detroit plants, one in Youngstown, OH and one in Evansville,
IN produced parts for the B-29.
Besides B-29 components the company
also provided parts for the A-20, B-17 and many other war
products. |
Briggs components were supplied to the Martin Omaha, NE
plant for final assembly into B-29s including the "Enola
Gay" and "Bockscar".
Briggs was also a supplier to the
other three B-29 final assembly plants. |
|
Chrysler - DeSoto
and Dodge |
(568) fuselage nose
sections, (559) leading edges, (4,752) engine cowling sets, and
(18,413) R-3350 radial aircraft engines. |
The airframe
components were built by DeSoto on Warren Ave. in Detroit and the R-3350s were built Dodge
in a new, dedicated plant in Chicago. |
DeSoto provided
airfrafme components for the Martin Omaha, NE plant for final assembly into B-29s
including, the "Enola Gay" and "Bockscar". DeSoto also supplied all of the engine cowlings for the B-29
assembly plants in Renton, WA and Marietta, GA.
Dodge
built R-3350 engines went to all four B-29 assembly plants.
Before supplying B-29 parts to
Martin it had previously provided (1,586) nose and fuselage
sections for assembly into the B-26 Marauder. |
|
Firestone |
Wing Fuel tanks
|
The Coshocton, OH
plant built disposable auxiliary fuel
tanks for the B-17, B-24 and B-29, |
The outer wing fuel
tanks consisted of seven cells and held 1,320 gallons of
aviation fuel, while the inner tanks consisted of four cells and
held 1,425 gallons of fuel. |
|
Fisher Body Div of
GM |
(13,772) B-29 Engine
Nacelles - These were the most complex component of the B-29 and
had 1,300 sub-assemblies in them.
Horizontal stabilizers, vertical
stabilizers, rudders, elevators, outboard wing sections, flaps,
exhaust collectors, engine cowlings, tail gun assemblies and rudder pedals, engine oil tanks along with many
other miscellaneous B-29 parts. |
Nacelles were
produced at the Cleveland, OH Plant #1.
Flaps,
vertical and horizontal stabilizers were produced at the
Cleveland, OH Plant #2.
Elevators, nacelles and tail
sections were made in the Lansing, MI
plant.
Parts and Assemblies - Grand
Rapids, MI, Pontiac, MI Ternstedt in Detroit, MI, Cleveland, OH Plant #1, Fleetwood,
MI, Memphis, TN, Central Development, Detroit, MI, Experimental Unit,
Detroit, MI, and
the Detroit Aircraft Unit.
Fixtures, jigs and tooling - Flint #1, Detroit Die
and Machine Unit and Detroit Stamping Unit. |
Fisher Body Division
of GM provided the following components to the Martin Omaha, NB
B-29 assembly plant. For
each engine: Exhaust manifold or exhaust collectors, the
engine nacelles, engine oil tanks.
Fisher Body also supplied the
rear turret assembly, which on the "Enola Gay", "Bockscar" and
the other Silverplate B-29 nuclear bombers was the only method of self
defense. All of the other gun turrets and sighting equipment
was removed to reduce weight.
Many of the B-29 components built
by Fisher Body were supplied to Martin in Nebraska by other
suppliers indicating that Fisher Body B-29 built components were
being provided to the other three B-29 plants, or subcontracted
to the first tier suppliers. These
components would include the engine nacelles as Fisher Body
built enough to supply 86% of the 3,970 B-29s built and Martin
only used 2,124 or 15%. Also horizontal stabilizers, vertical
stabilizers, rudders, elevators, outboard wing sections, flaps
would have been supplied to Bell in Marietta, GA and Boeing in
Wichita, KS and Renton, WA. |
|
Goodyear |
Forward and rear bomb bay fuselage sections,
rudder, vertical stabilizer, dorsal fin assembly, elevator
assembly, and horizontal stabilizer assembly |
Akron, OH |
|
|
Hudson |
(802) rear
fuselages, bulkheads, wing tips, rear turrets |
Detroit, MI |
|
|
Frigidaire Div. of
GM |
(54,737) four Blade
Propellers for both the B-29 and P-47. |
Dayton, OH |
|
|
B-F. Goodrich |
Fuel Tanks |
Akron, OH |
|
|
Libby-Owens-Ford |
Bombardier's glass nose section |
Toledo, OH |
|
|
New Departure
Division of GM |
1,417 roller
bearings for B-29 Fire control system |
Bristol, CT |
|
|
Packard Division of
GM |
Packard supplied
high altitude ignition cable for the B-29 engines. |
Warren, OH |
|
|
In the table below is the production schedule
that the auto companies had to meet for the supply of components for the
Martin Omaha, NB built B-29s. Note that in several months there is
no production or at least no accepted production. It could have
been that there was a parts shortage that did not allow the aircraft to
be finished and accepted by the US Army Air Force. I do think the
work stoppages were intentional.
Aircraft in World War Two were built in Block Numbers,
which had frozen designs and did not allow for any changes to the
aircraft while coming down the production line. This allowed mass
production of aircraft without having to make the constant changes and
improvements that were needed due to information that was coming back
from testing and operational units. When a new block was started
it contained updates and improvements. However, even then to
facilitate production, not all of the upgrades would be included and
afterwards the aircraft would go to one of nineteen modifications
centers for the latest updates. The modification centers were an
important part of the process needed to keep the aircraft production
lines operating in a timely manner. In the case of Martin Omaha it
had its own modification center.
Serial numbers reflect the year the aircraft
were ordered as indicated by the first two numbers in the sequence.
The first B-29 built at Martin Omaha was the 65202nd aircraft ordered by
the US Army Air Force in 1942. The last one off the assembly line
in August of 1944 was the 86273rd aircraft ordered in 1944.
Of the four plants making B-29s during WWII,
Martin in Omaha, NE was chosen to build and then modify the operational
B-29s for the nuclear bomber Silverplate program. Martin was considered by the US Army Air Force to have the best
quality of the four plants. The first fifteen came directly off
the assembly line and went to Wendover Army Air Field, UT, where they
were converted to the Silverplate configuration and then used in
training.
The fifteen operational Silverplates that went
to Tinian were also built at Martin and modified at the adjacent
modification center. Modifications included but were not limited
to replacing the Hamilton Standard Propellers with Curtiss Wright
Electric reversible props, eliminating all of the gun turrets, gun
sights, and gun control computers with the exception of the tail turret,
and modifying the bomb bays to accept the large atomic
devices.
The Martin Plant received the Army-Navy "E"
for Excellent Award on December 13,1943 and then later 3 stars for
on-time delivery. The awards were given for the previous B-26 production
at the plant.
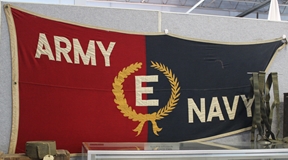
Martin Omaha,
Nebraska World War Two B-29 Production Schedule |
Month |
Number built |
Block Number |
First Serial Number |
Last Serial Number |
Comments |
1944 |
|
|
|
|
|
May
|
3 |
B-29-MO-1 |
42-65202 |
42-65204 |
|
June |
7 |
B-29-MO-5 |
42-65205 |
42-65211 |
|
July
|
0 |
|
|
|
|
August |
8 |
B-29-MO-10 |
42-65212 |
42-65219 |
|
September |
16 |
B-29-MO-15 |
42-65220 |
42-65235 |
|
October |
28 |
B-29-MO-20 |
42-65236 |
42-65263 |
|
November |
0 |
|
|
|
|
December |
50 |
B-29-MO-25 |
42-65264 |
42-65313 |
|
1944 Total |
112 |
|
|
|
|
1945 |
|
|
|
|
|
January |
69 |
B-29-MO-30 |
42-65315 |
42-65383 |
|
February |
18 |
B-29-MO-35 |
42-65384 |
42-65401 |
|
February |
67 |
B-29-MO-35 |
44-27259 |
44-27325 |
The B-29 "Bockscar"
was serial number 44-27297 and came off the Martin Omaha
assembly line in February 1944. |
March |
0 |
|
|
|
|
April |
0 |
|
|
|
|
May
|
33 |
B-29-MO-40 |
44-27326 |
4-27358 |
|
May
|
35 |
B-29-MO-40 |
44-86442 |
44-86276 |
|
May
|
39 |
B-29-MO-45 |
44-86277 |
44-86315 |
The B-29 "Enola Gay"
was serial number 44-86292 and came off the Martin Omaha
assembly line in May 1944. |
June |
55 |
B-29-MO-50 |
44-86316 |
44-86370 |
|
July
|
55 |
B-29-MO-55 |
44-86371 |
44-86425 |
|
August |
48 |
B-29-MO- 60 |
44-86426 |
44-86473 |
|
1945 Total |
419 |
|
|
|
|
Grand Total |
531 |
|
|
|
|
Below are two other B-29s built by Martin
built with US Auto Industry fuselage and wing components.
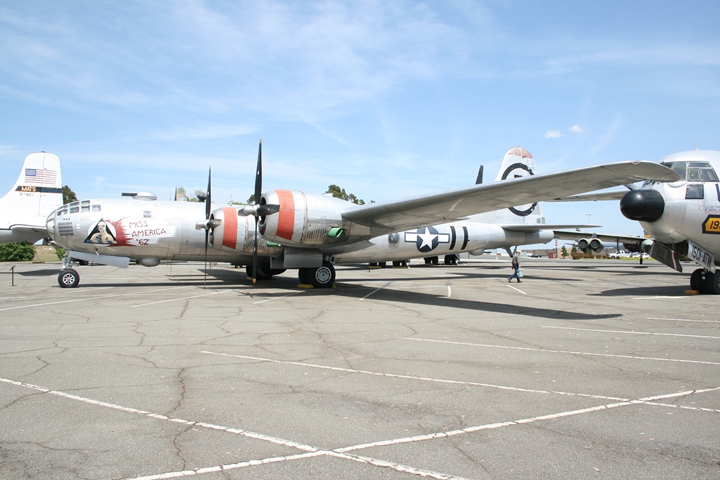
This Martin built B-29 42-65281, seen here at the Travis AFB Heritage Center, came off the assembly line at Omaha,
NE in December 1944. Author's Photo.
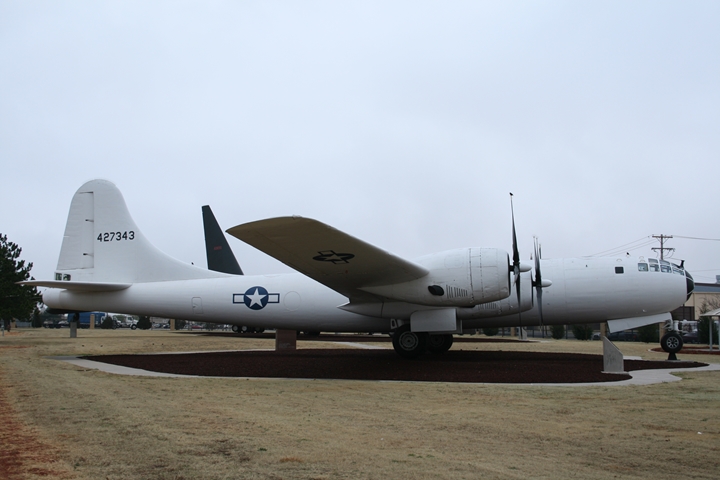
This Martin built B-29 44-27343, seen here at the Tinker AFB Heritage Display, came off the assembly line at Omaha,
NE in May 1945. Author's Photo.
Martin built B-29 44-86408 is also displayed at
Hill AFB in Ogden, UT. Five of the 531 Martin B-29s therefore
still
survive. |