Other Lansing Companies that contributed
to winning World War Two
Dail
Steel Products Company
in World War Two
Recognizing a Company from my Hometown that contributed to the winning
of World War Two
Lansing, MI
1913-1972
This page added
9-23-2021.
Dail Steel Products of Lansing, MI was
originally formed in 1911 as the Dail-Gier Company, located on
North Grand Avenue at Ionia Street. The principal owners of the Dail-Gier Company were Ernest I. Dail and B.S. Gier. In 1913 the
two partners went their separate ways and Dail Steel Products moved to
750 East Main Street, occupying the former Cove Manufacturing Company
factory. Early products of Dail Steel Products were bread boxes
and metal card racks. The company initially had ten employees
which increased to 187 workers by 1948. During World War
One, the company produced products for the war effort. As the
company grew, it became a metal stamping house with customers in the
automotive, home appliance, and agricultural industries.
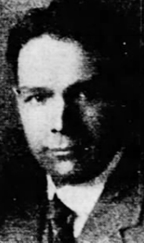
Ernest I. Dail
Before starting Dail Steel Products, Mr. Dail was a postcard salesman.
He invented a revolving metal rack to display his cards. Now these
are found in stores that display all sorts of wares, including
magazines. The metal racks were one of the first products of Dail
Steel Company.
In June 1937 Dail Steel Products had a public
open house of its new office building at the corner of South Hosmer and
East Main Streets to celebrate its 25 anniversary in business.
Another reason for the public open house was that the building had the
company's Dailaire Air Conditioning system installed. The company
wanted prospective customers to come in and experience how well it worked. The
new office building included six offices, a drafting room, a school
room, sales and accounting offices and storage space.
This artist's rendition shows the new Dail Steel Product administration
building.
Dail Steel Company Products: Along
with the revolving metal display racks mentioned above, Dail Steel
Products also manufactured steel shipping boxes that bakeries used to
ship bread as its first products.
In 1914, Dail Steel Products manufactured the
Wolverine Indoor Toilet System for use in dwellings that were not
connected to a sewer system. One potential use for the Wolverine
Indoor Toilet System was for small country schools. Dail Steel
Products specified one toilet bowl for every 20 students. The
company built six different steel tanks with capacities from 142 to 585
gallons. The 585 gallon tank accommodated six toilet bowls or 120
students. The tank was of copper steel construction, not stainless
steel that would be used in similar construction today. The
company supplied a germicide for the system. There was no outlet
for the tank as there is in a modern septic system and the tank would
have had a finite life to it. It is unknown how many units
were sold and installed.
During World War One, Dail Steel Products
could no longer procure the materials it needed for its product line of
the Wolverine Indoor Toilet System. However, the government had
requirements for stamped parts. It was in 1917 and 1918 that the
company began purchasing punch presses and was able to secure government
contracts. This was the transition point at which Dail Steel
Products moved into stamped parts rather than assembled products. After
World War One the company added a new building and focused on supplying
the automobile industry with stamped parts. In Lansing there were
several local customers for its stampings. At the end of World War
One, the Olds Motor Works, the Reo Motor Car Company, and The
Duplex Truck Company were in Lansing. In 1922 the Durant Motor
Company came to town with a new assembly plant on Verlinden Avenue.
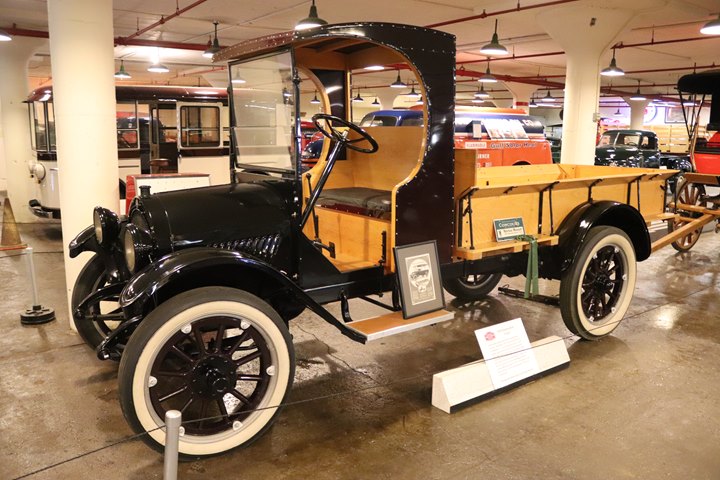
Dail Steel Products could very well have
supplied for this 1919 Model T Oldsmobile 3/4-ton truck. Author's
photo.
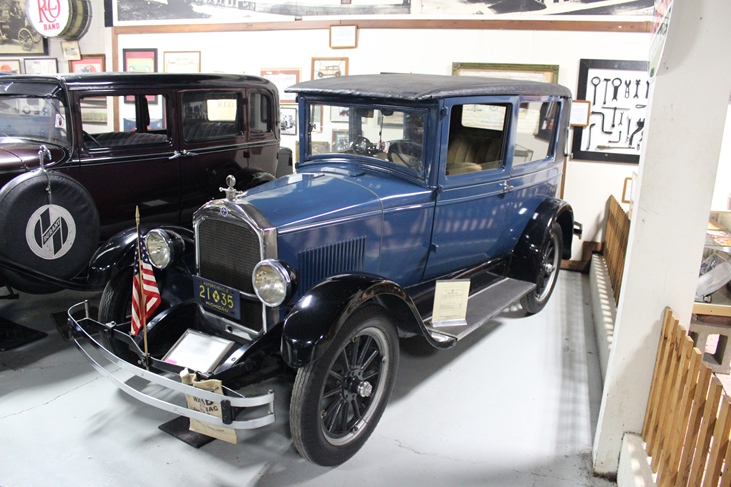
This 1926 Durant Star was built by the
Durant Motor Company. It could also have Dail Steel Product stampings in it.
The Star was the low priced line of vehicles produced by Durant, for
which production ran from 1922 to 1928 at Lansing. Author's photo.
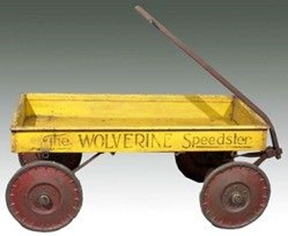
Most of us had a red steel wagon when we
were young. Most of them said "Radio-Flyer" on it. I still
have a Radio-Flyer wagon in the garage for the grandchildren to play
with. What I learned in researching Dail Steel Products is that it invented
the steel children's wagon. In 1920 Dail Steel Products entered
the toy market with the "The Wolverine Speedster" wagon, which
was the first all-steel children's wagon. It was an Ernest I. Dail design.
It was such a success that other companies quickly entered the market
with similar products, resulting in Dail Steel Products exiting the toy
business altogether. Today's wagons are historically linked to Dail
Steel Products and "The Wolverine Speedster." How cool is
this?
On May 21, 1935, Ernest I. Dail was awarded
patent number 2,002,312 for a "Furnace and Air Conditioner." The
term "Air Conditioner" was not the same as how it is currently used,
which is for a unit that takes the heat out of the air and cools a
dwelling. The way Ernest Dail used the term "Air Conditioner"
was to actually use water to clean the air as it moved through the
furnace. This is a quote from the first paragraph of the patent:
"This invention generally relates warm air furnaces of the type in which
air from the atmosphere may be washed or otherwise conditioned and
mechanically propelled to various points of distribution."
The complete patent can be found at this link:
Ernest I. Dail
Patent 2,002,312
Dail Steel Products then started selling
furnaces under the Dailaire name which later used city water or well
water to cool the air as it passed through coils in the furnace.
The downside of this system is that it used an extensive amount of
water. The company notes that the water used in the Dailaire
system in its new administration building was stored in a tank on the
roof that was then used to water the grass. In cold months the
Dailaire system allowed for the furnace to humidify the air that
went into the house.
This twenty page pamphlet published by the Dail Steel Company in 1938
explains in detail the theory behind heating and cooling with a Dailaire
product:
Taking the Mystery out of Air Conditioning
On April 1, 1940, Mr. Bruce McLouth purchased
the heating and air conditioning division of Dail Steel Products and
formed a new company named McLouth Air Conditioning Corporation.
Mr. McLouth had previously been the heating and air conditioning
engineer for Dail Steel Products for six years before starting the new
company and becoming its president. The new company employed Dail
Steel Products'
former engineers and installers from the Dailaire division of the company. After the April
1, 1940 announcement, there is no more information on the McLouth Air
Conditioning Corporation in the historical record.
Prior to World War Two, Dail Steel Products
did more than make metal stampings for other companies. I
personally know that the company built standard furnaces, because my
grandfather had a Dail Steel Products furnace in his basement. I
used to spend a considerable amount of time with my grandfather working
on projects in his basement. I distinctly remember the furnace.
It was typical of the furnaces in many houses in Lansing that were
originally coal burning and then converted to burn natural gas or
fuel oil. The 1934 Cooperative Tractor Catalog shows Dail Steel
Products of Lansing, MI as being a supplier of steel sheet. The
Cooperative Tractor Catalog also had a category for steel stampings and Dail Steel Products was not listed there. In the 1928 edition of
the Cooperative Tractor Catalog, Dail Steel Products was shown as
being a supplier of agricultural tanks.
On April 30,1942, Lansing industrialist and
president of Dail Steel Products, Ernest I. Dail passed away. He was replaced
with his
brother Elmer Dail, who had been general manager of the Jarvis
Engineering Company of Lansing.
The End of Dail Steel Products:
-
In June 1971, there were
rumors that the company would either close or move out of Lansing.
Dail Steel Products had no comment on the matter. By this time Lewis
Dail was president of the company and the address of the company was
now 1000 South Hosmer. It is unknown whether Dail Steel
Products workers were represented by a union. There is nothing
in the historical record of any strikes against the company nor any
other union activity. After World War Two there were numerous
strikes at most of the union represented companies in Lansing which,
for the most part, included all of the manufacturing companies.
Several companies, including John Bean and Motor Wheel, eventually
moved production out of Lansing due to labor issues. So, when
there was word that a company will move out of Lansing area, it was
assumed to be
labor related. So, Dail Steel may have been having labor
problems or its labor cost was too high to compete with non-union
companies. We will never know.
-
In August 1971 the
company put 35 punch press machines and other related equipment up
for sale. The address for the auction was 1000 South Hosmer,
not 750 East Main Street. This is because I-496 was laid right
over Main Street in Lansing. This may have also resulted in
the demolition of the administration building. The
construction of
I-496 may have been one of the causes of Dail Steel Products
closing.
-
In December 1971 the
company had two forklift trucks up for sale.
-
On June 8, 1972, the
remaining equipment of Dail Steel Products was put up for auction. This
was authorized by the company's Board of Directors.
-
On October 8, 1972, Dail
Steel Products was listing its factory for sale or lease. The
factory was described as a 46,000 square foot heavy industrial building with
modern office space. The facility was located on 2.6 acres.
-
In May 1974 the Lansing
Storage Company used the former Dail Steel Products factory as an
auction site. Several other companies in Lansing used the
former Dail facility to hold auctions.
When Dail Steel Products closed, it was the
longest existing family owned business in Lansing. This is such a
sad ending for this Lansing company.
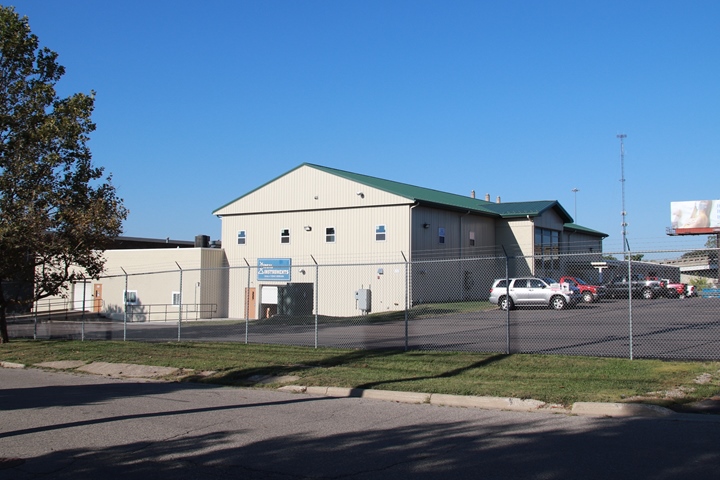
The current building on the site of the
former Dail Steel Products Company in Lansing, MI is now the home of
Ideal Instruments, a division of Neogen Corporation. In 2017
Neogen spent $1.3 million for a complete rehabilitation of the former Dail Steel Products plant. The rehabilitation of the building
added over 39,000 square feet and 25 new jobs. It can be seen in
this photo that the north side of the building was completely redone and
looks very modern. If I had arrived before the work was done, I
would have seen the building like it was when Dail Steel owned and
operated the facility. Author's photo.
Ideal makes precision veterinary drug delivery
instruments in the facility. Ernest I. Dail would be proud of the
fact that Ideal Instrument division of the Neogen Corporation is making
use of his former plant to make high tech products.
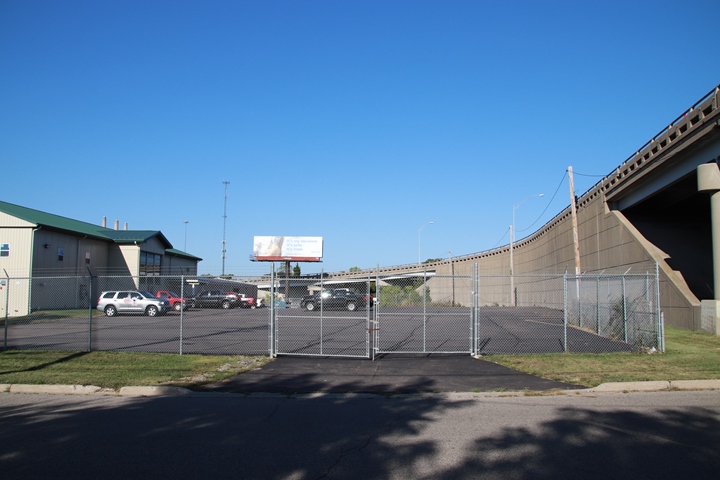
The parking lot was the former location of
the Dail Steel administration building that was built in 1937. It
may have actually been partially located where I-496 was built at in the
late 1960s. At this location I-496 was built directly over East Main
Street in Lansing. This may have resulted in the demolition of the
administration building. It caused the address of the company
to change from a Main Street address to 1000 South Hosmer Street.
Author's photo.
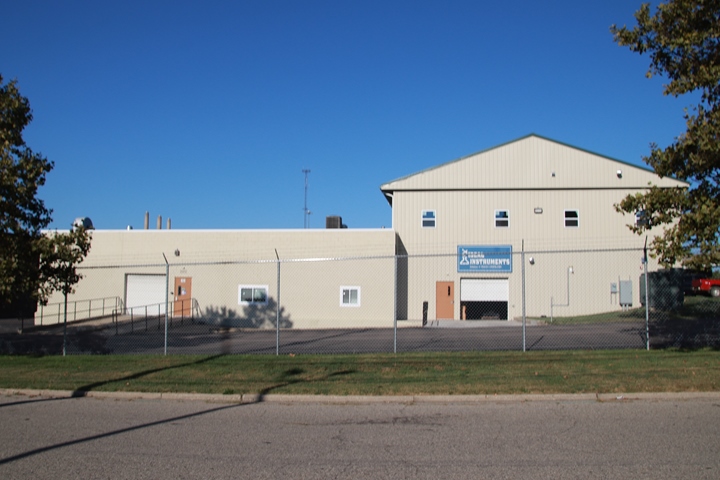
This photo shows where the newly restored
building on the right joins with the original factory building.
Author's photo.
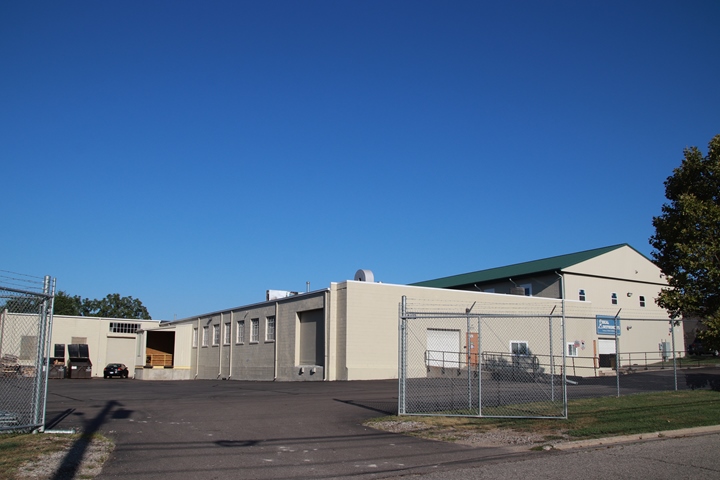
The south side of the complex shows a
building of an earlier construction type. Author's photo.
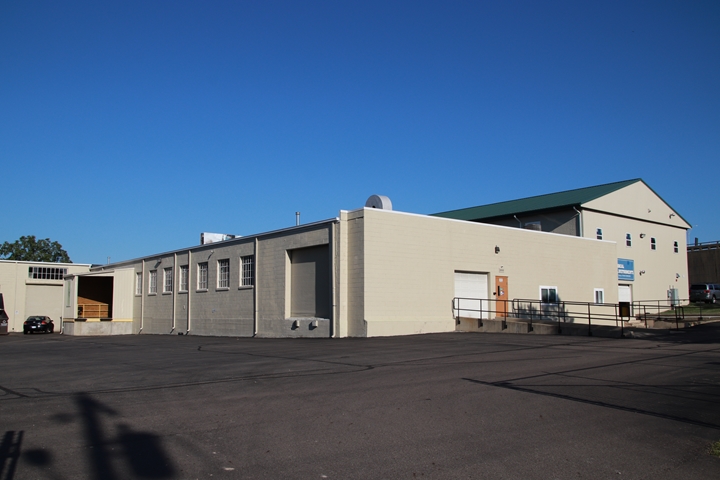
Author's photo.
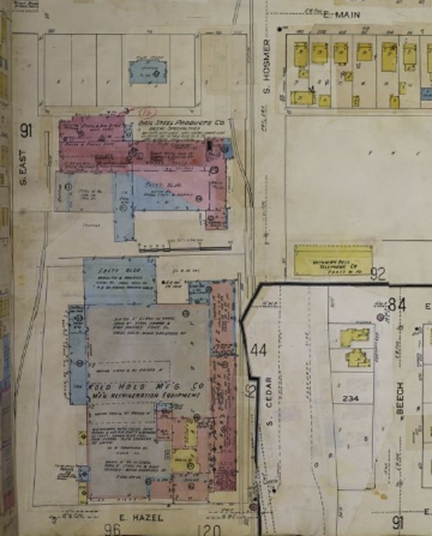
This Sanborn Insurance Company map shows the
Dail Steel Products in 1951 at the location of East Main and South
Hosmer Streets. In 1951 the plant to the south of Dail Steel Products
was owned by the Kold Hold Manufacturing Company. However, from
1915-1945 this building was the home of John Bean, which made
agricultural spraying equipment. John Bean most likely was a
customer of Dail Steel Products for many of the metal stampings it needed in its
products. During World War Two John Bean manufactured chemical
decontamination products for the U.S. Army Chemical Corps which may have
used Dail Steel Products stampings. John Bean also built crash
trucks for the U.S. Navy that may have required Dail Steel Products
stamped parts.
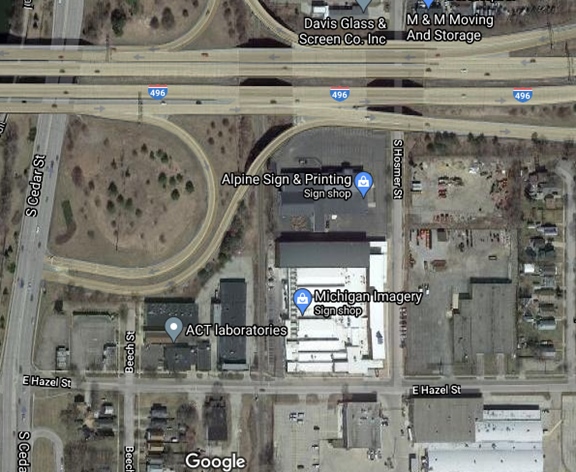
This Google Maps Satellite view shows the
same location as the Sanborn map above does. However, Alpine
Sign and Printing is not in the former Dail Steel Products plant.
This is incorrect. This view shows that I-496 was laid down right
over East Main Street and possibly onto the property of the Dail Steel
Products.
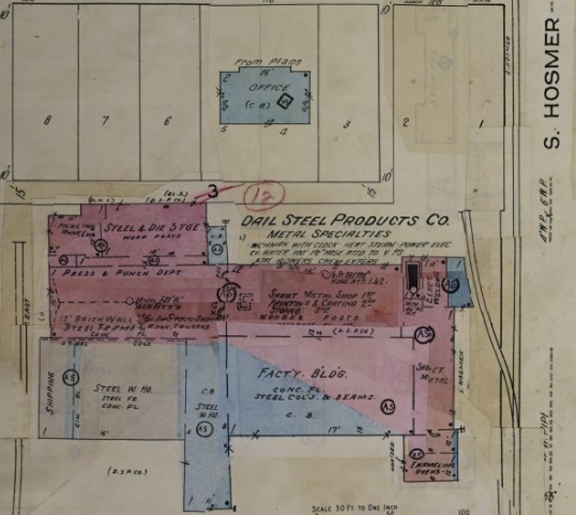
This enlarged Sanborn map shows the detail
of the factory in 1951. The northeast building had two floors for
painting and coating metal stampings.
World War Two Products: Metal stampings
are ubiquitous and are used in many types of products. It is unknown
what stampings Dail Steel Products produced to help win World War Two, as
that information is unavailable. It is known that the company's
resources were 100% dedicated to the war effort. However, if we
assume it was a supplier to local companies in Lansing, there are
several possible products it could have produced during the war.
The following is educated conjecture.
The Reo Motor Car Company, which was just a
mile away from Dail Steel Products, produced 1,424,473 aerial and depth
charge fuzes for the U.S. Navy. Two examples below show how Dail
Steel could have stamped out parts for these fuzes. Making fuzes
was not part of Reo's peacetime product line, as it was a truck
manufacturer, and probably did not have the presses for the stampings used on
the fuzes. Even in peace time, any small stampings Reo needed for
its trucks could have been provided by Dail Steel Products or other
dedicated stamping houses.
Having the stamping house within walking
distance during World War Two was helpful while gas rationing was in force. This allowed the product responsible engineer at Reo and
the tool design engineer at Dail Steel Products to talk face-to-face
about the requirements for the Navy fuzes. It also allowed for
quick review of a sample run to make sure that the Navy inspector on
location at Reo approved the parts. It allowed for communication and
prompt turn-around of new parts to move smoothly and quickly.
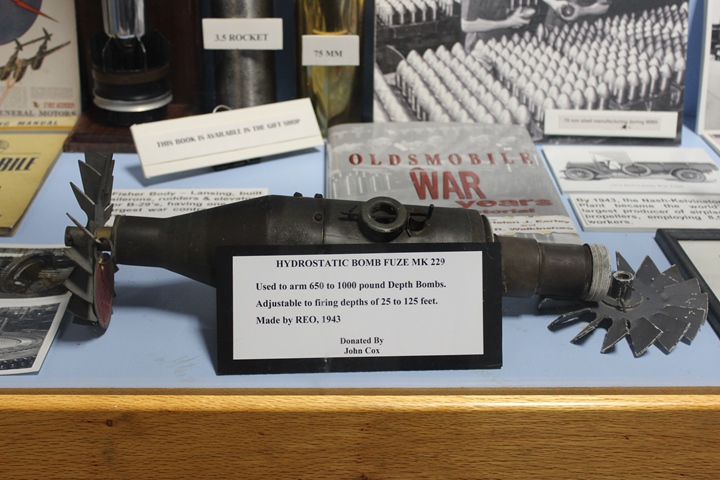
This photo shows the sixteen blade arming vane attached to the tail of a
Mark 229 Hydrostatic Tail Fuze as
a separate piece. The arming van was 5.25 inches in diameter.
Author's photo taken in 2015 at the RE Olds Museum in Lansing, MI.
This Reo-built Mark 229 Hydrostatic Tail Fuze was used by the U.S. Navy during World War Two in its 650 and 1,000
pound depth
charges. Reo built 100,933 of these through July 1944. The fuze
is 16.33 inches long with a diameter of 3.25 inches, while the sixteen
blade arming vane is 5.25 inches in diameter. Depth settings were
made by a hand dial on the device and could be set for 25, 50, 75, 100,
and 125 feet. The small hole on the left end of the body was used
to insert a pin into the device to disarm it. Reo did not arm
the fuzes it built. They were inert when they left the factory.
The units were armed at another location.
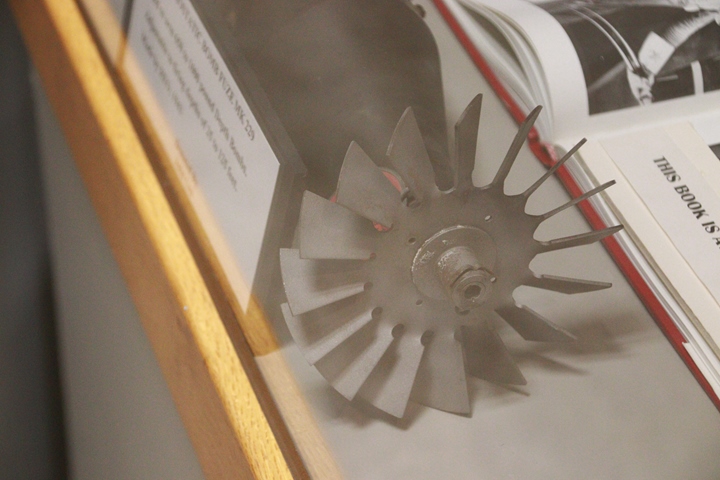
The Olds Museum changes its displays around
for variety. This is the same Mark 229 Hydrostatic Tail Fuze in
2021. This presentation shows the arming vane's three components
of two stampings and a machined or powder metal part in more detail. The two
stampings were good candidates for Dail Steel Products to make. Author's
photo taken in 2021 at the RE Olds Museum in Lansing, MI.
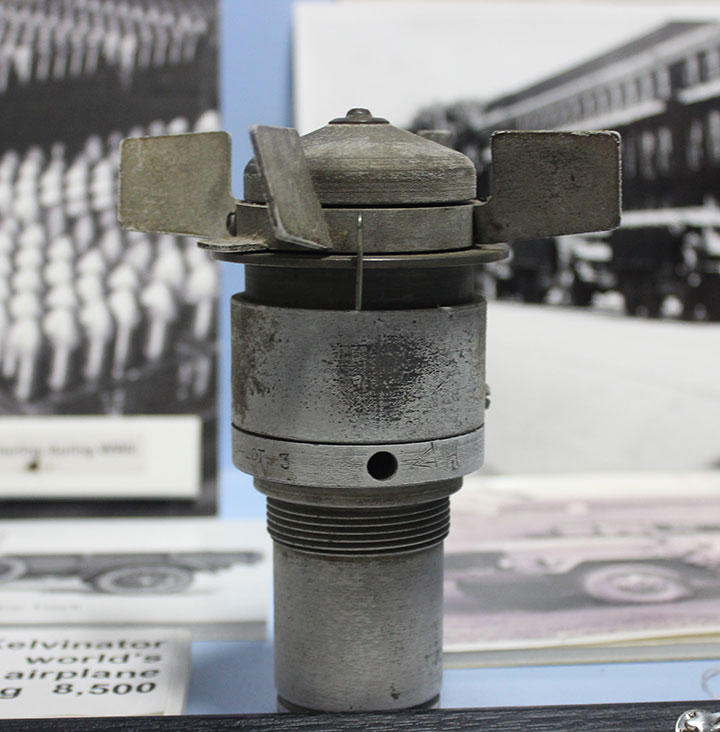
This Reo-built depth torpedo arming fuze was on display at the R.E.
Olds Museum in 2015. Note the cotter pin that keeps the vanes from
spinning until armed, maintaining it in a safe mode. Author's
photo.
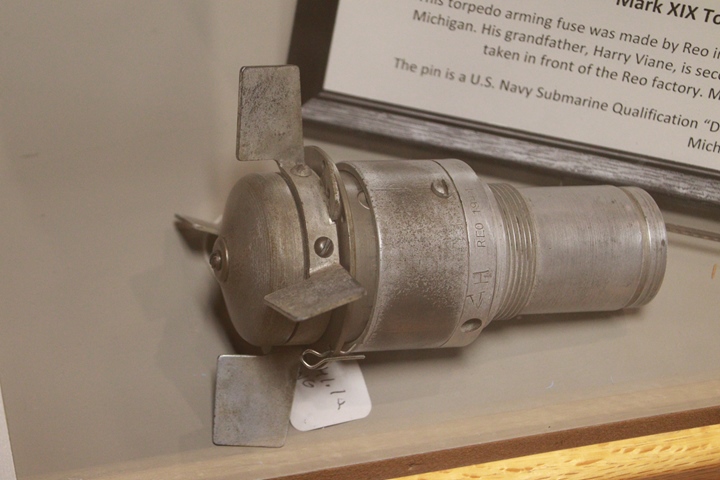
This fuze was also re-oriented when I
photographed it in 2021. It shows more clearly than the
2015 photo that the arming vanes on the device are actually two stamped
parts attached with screws. It also more clearly shows the cotter safety pin.
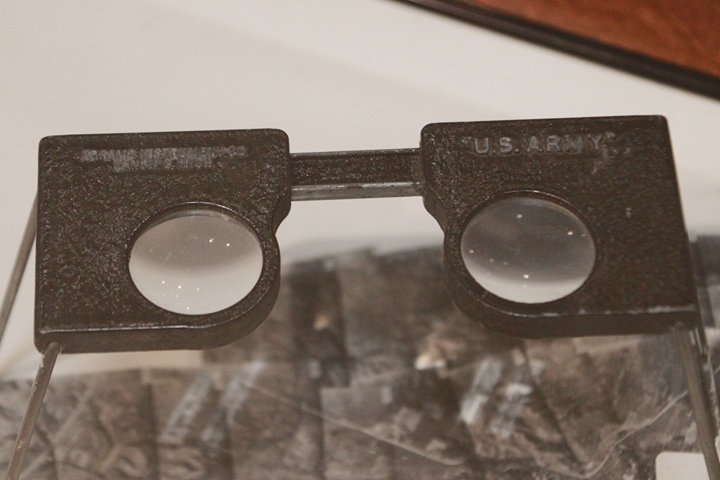
Just over a mile to the north of Dail Steel
Products was the Abrams Instrument Company that made the U.S. Army Air
Force CF-8 stereoscope map reader. Abrams was a small shop and
most likely did not have its own metal stamping capabilities. It
mostly designed the instruments it built and then had other manufacturers
like Dail Steel Products provide all of the components for final
assembly. The embossed black steel frames are steel stamped
parts. Dail Steel Products had the capability on the second floor
of its plant to paint steel
stampings like this. Abrams'
original order for the CF-8 was 26,000 units in 1942. It had other
contracts for them later in the war and continued building them up
through the end of the war. Author's
photo taken in 2021 at the RE Olds Museum in Lansing, MI.
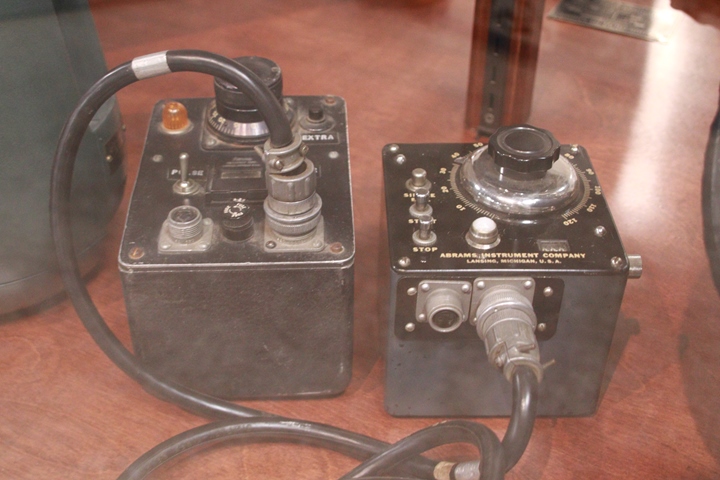
These two Abrams-built instruments on
display at the RE Olds Museum in Lansing, MI have stamped metal covers
and deep drawn metal boxes. The stamped metal covers could very
well have been done at the nearby Dail Steel Products. Dail had
the capability to stamp out and then paint the covers. However,
the metal boxes may have been beyond the capability of the presses that
Dail Steel Products owned. To make these it took multiple steps
from a large tonnage press with a progressive die. Author's photo.
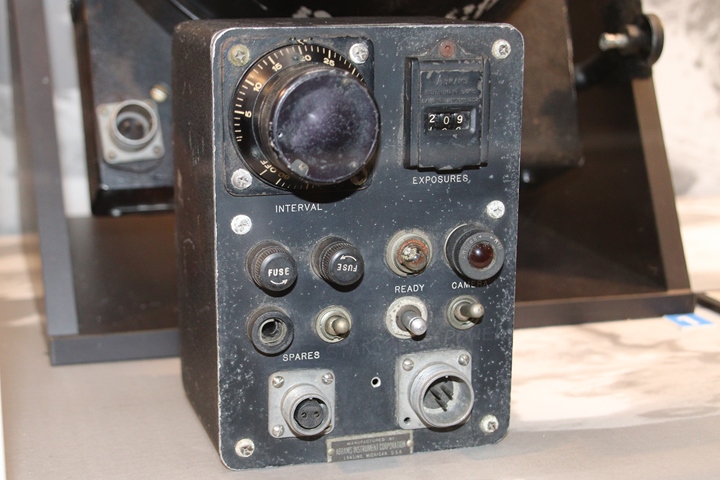
This Abrams Instrument-built intervalometer
on display at the National Museum of the United States Air Force in
Dayton, OH may well have a stamped out face plate by Dail Steel Products.
Author's photo.
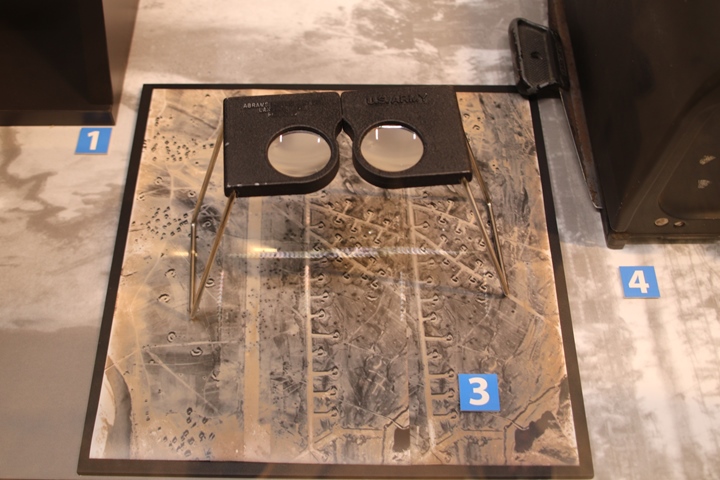
Also at the National Museum of the United
States Air Force is this Abrams CF-8 stereoscope map reader, which could
have a Dail Steel Products manufactured frame. Author's photo.
The National Museum of the United States
Air Force is the largest aviation museum in the world and the biggest
tourist attraction in Ohio. While it is all conjecture, products
that Dail Steel Company may have manufactured for the two Abrams
Instrument Company's products may be hiding in plain sight. Parts
from the company that Ernest I. Dail founded in Lansing, MI in 1913 may
well be on display for the many visitors to the Museum.
Other Lansing Companies that contributed
to winning World War Two
|